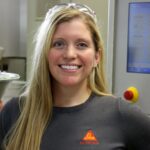
Adhesives are replacing mechanical joins across an increasing number of components and applications as OEMs strive to reduce weight for both internal combustion and electricpowered vehicles. An example is the 2021 Ford F-150, which has an aluminum-alloy body.
Automotive Industries (AI) asked Leslie Wolschleger VP R&D Sika Automotive USA to tell us how SikaPower®-550 G came to be specified for the new F-150.
Wolschleger: Sika has been a global supplier to Ford Motor Company for decades. We have been working with the Ford Research Center on innovative projects for many years, supplying a full range of acoustic, reinforcement and direct glazing products to Ford globally.
SikaPower®-550 G structural adhesive was developed with Ford to provide increased durability, superior open time in an uncured state and a wider cure process window (mainly time and temperature). The developmental targets were verified together with Ford, first by screening previous generations of SikaPower® products and then through further development for both aluminum and steel bodies with improvements to meet new and higher standards for crash performance. Ford conducted benchmark studies on many of these SikaPower® samples at both lab and full vehicle scale.
This enabled the material property requirements at a lab level to be verified in real world conditions. The collaboration process involved other Tier suppliers and substrate coating companies.
Coatings of the crash grade aluminum substrate is a critical aspect for durability in the F-150.
Our partnership with the coating supplier helped to ensure our adhesives are compatible with the coating. It provided confidence that we had the correct chemistry to enable chemical bonding to the substrate that stood up the loads seen in a crash event. We were able to fine-tune intimate property relationships between the adhesive and the substrate to ensure a cohesive fracture profile and eliminate substrate failure.
AI: What design challenges did the adhesive help to overcome?
Wolschleger: The targets for adhesive performance were challenging as specifications normally met by multiple adhesives were condensed into one. A vision for the adhesive was that it could be used on both aluminum and steel applications, and in all areas of the vehicle. While adhesion and impact modifications were needed to meet crash performance criteria, we also needed to ensure full coverage in hem applications. Thus SikaPower®-550G contains glass beads to ensure full wet out of the bonded area after application. The beads also ensure there is a constant bond line thickness in the adhesive joint guaranteeing consistent bond performance. The addition of glass beads along with fine tuning of mechanical performance, while maintaining corrosion resistance, makes the SikaPower®-550 G suitable for hem-flange bonding applications as well.
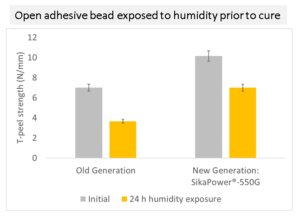
During the vehicle development phase, CAE modelling was heavily used to predict overall vehicle performance. The modelling informs the design and usage of the adhesives. The use of glass beads enabled the final vehicle crash performance to match CAE predictive results.
Further, weldability and rivetability screening was needed with material that contained glass beads to ensure the presence of the beads would not interfere with traditional mechanical joining methods. Humidity resistance is also a key factor for adhesive performance. The new SikaPower®-550 G demonstrates an improvement in humidity resistance prior to cure and excellent stress durability of the bond under static load in a corrosive environment after cure.
The durability of the adhesive when subjected to both static loading and a corrosive environment introduced a new challenge for the SikaPower®-550 G development team. This required maximum corrosion resistance and the ability of the adhesive to withstand a static load while being cycled through corrosion accelerated conditioning. This stress durability test inflicts maximum and challenging punishments on a cured adhesive in a lap geometry that is held under a constant static load. Lap specimens are cycled, each cycle lasting one day, through humidity and salt conditions. SikaPower®-550 G surpasses the previous generation performance in the number of cycles it can hold its’ bond at both low and high temperature cure conditions. It also not only meets the specification but exceeds it.
AI: Has this paved the way for increased use of adhesives in the automotive industry?
Wolschleger: The automotive industry and supplier networks are becoming more aware of how structural adhesives can be used to improve not only crash performance of the vehicle, but also durability and resulting occupant comfort. We have seen a significant number of automotive manufacturers and vehicle platforms using SikaPower® structural adhesives throughout the vehicle body.
Not coincidentally with that we are embracing more collaboration between Sika and our OEM customers, especially in the early vehicle design phase to maximize the benefit of our products that enable their program goals: lightweighting, ease of manufacturing (cycle time reductions) and improvement of overall vehicle performance.
AI: What about at the component level?
Wolschleger: We have observed an increase in the use of structural adhesives at the component level. As sub-assemblies are often prefabricated outside the OEM assembly plant at a Tier supplier, the superior pre-cure open time performance of SikaPower®-550 G becomes important.
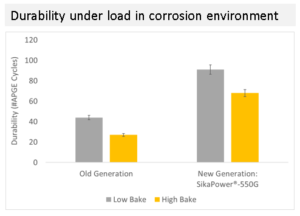
SikaPower®-550 G wet out and coverage performance remains constant and moisture uptake is improved during transport. Once processed and cured at the OEM, resulting material performance and cohesive failure modes meet industry standards and requirements. While SikaPower®550 G is a shining star, additional SikaPower® adhesives have been developed for component level assembly.
To address the growing number of mixed material bonding applications, we have introduced an entire line: SikaPower® MBX (Mixed Bonding eXcellence) structural adhesives for such use. Our latest innovation is SikaPower
®-510 G MBX. It is used to join the boron steel torque box (designed to strengthen the vehicle’s unibody construction) to an e-coated aluminum front rail assembly on the 2020 Ford Explorer and Lincoln Aviator.
SikaPower® MBX also enabled corrosion mitigation for the mixed metal combination, as well as protection from thermal delamination during the e-coat process.
AI: Do you think adhesives will replace mechanical bonds?
Wolschleger: We will see more mixed material bonding in the future, where adhesives will be used with a wider array of substrates, both metallic and non-metallic. For metallic applications, the mechanical properties can be fine-tuned to the application and have an added benefit of preventing galvanic corrosion when bonding metal substrates.
In mixed metal/ non-metal joining, already there are production vehicles which use adhesive to bond carbon fiber reinforced plastic (CFRP) with metal substrates in their body structures to achieve lower weight targets. Sika believes there will more instances of similar applications as automakers get more aggressive with lightweighting efforts.
While the use of adhesive can help to decrease mechanical joining points, and to add strength to the joints by transferring energy across the total bond surface, the approaches serve complementary purposes in assembly.
AI: What else should automotive designers know about advanced structural adhesives?
Wolschleger: Advanced structural adhesives are built on chemistry that is proven in the industry and enables durability and corrosion resistance over the life cycle of the vehicle. What excites me is that this technology is used to not only improve driver comfort, but more importantly safety. An impact modified adhesive in a joint, such as SikaPower®-550 G, absorbs more energy in less time than a mechanical weld in a crash event.
The energy is transferred as designed by the OEM to facilitate the best possible outcome in a crash event.
Automotive design is an iterative process enabled by technology advancements; vehicles throughout history have become lighter, stronger, more comfortable and safer for their occupants. By progression recent body structural designs have evolved from all-steel, to a mix of aluminum and steel, and with the latest advancements, a mix of different metal and non-metal substrates. The use of advanced structural adhesives helps these newest vehicle designs to come to life.
Our message to automotive designers is that you now have more freedom in designing body structures with a wider array of material choices, and we welcome collaboration to make design challenges from dreams into reality.