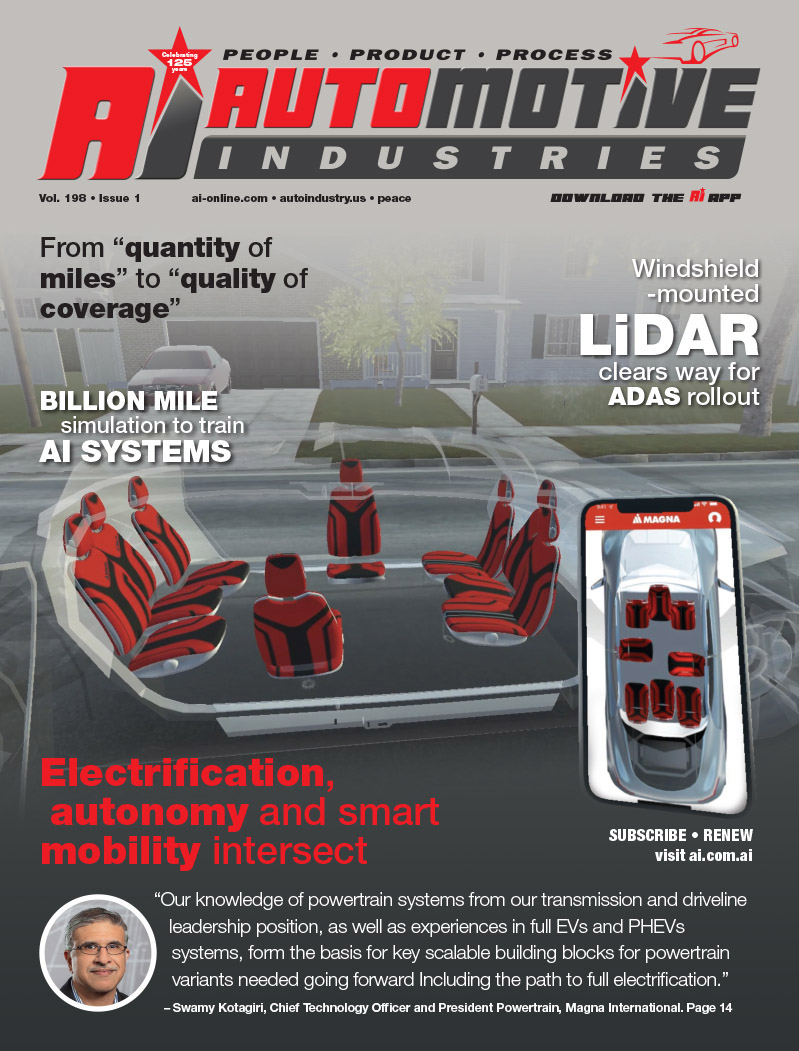
Tower is developing technology for joining aluminum that could change the way cars are made.
![]() |
Tower’s friction-stir welder joins aluminum suspension components designed for Lincoln limousines. |
Art Scafe heads up Tower’s advanced new product development group. Formed a year-and-a-half ago, the group investigates the potential growth for new technologies. Two of those technologies, roll-bonding and friction-stir welding are already beginning to make an impact.
Roll bonding dates back to the ’50s and has just recently found its niche in the auto industry in the manufacturing of heat shields. Tower automotive produces about 9.3 million heat shields a year.
Roll-bonded panels are made from two sheets of aluminum that are bonded together by heat and pressure. The two rolls go through a scrubbing process to make sure that no dust or particles are trapped between the bonded sheets. One side is silk screened with a graphite pattern and the two are rolled together, physically merging the sheets where there is no graphite. The process reduces the thickness of the finished sheet by about 60 percent. The flat sheets are placed between two steel plates and inflated with compressed air at about 900 to 1,000 PSI forming a tread-plate-like pattern. Scafe says that the roll-bonded panels have better torsional rigidity than flat sheets at half the weight.
An additional benefit to the process is that the air pockets give you some attenuation of sound.
“We’re investigating the possibility of actually injecting sound-deadening foam in the air pockets,” Scafe says, “to increase the physical NVH capability.”
While heats shields are normally small items, Tower is producing large roll-bonded floor panels for the production Ford GT sports car. Tower is supplying the left and right floor panels and a removable shear plate that fits over the center-tunnel-mounted fuel tank. Ford has also asked Tower to quote on the two panels that make up the rear bulkhead and a small one at the top of the tunnel.
![]() |
The two large castings will be joined together, cut to size and bushings will be added (above). Note that the seam is nearly invisible when the part is cut and polished. |
![]() |
Roll-bonded panels (above) found their way into the auto industry as heat shields. Tower sees potential for interior panels. Roll-bonded panels offer a 50 percent weight savings over solid sheets. |
The trick to using the harder metal is a process called regression heat treating. Used by other OEMs on extrusions and heavier pieces, Tower is the first to use it on sheet stock.
Since the metal is under some stress while it’s being inflated, the T6 alloy has to be softened before inflation. The aluminum is heated to 550 degress Celsius and must be quenched with water. Extrusions need to be quenched within 10 seconds of coming out of the oven but the thin panels tend to cool so quickly that a nozzle-filled tunnel had to be built that quenches them immediately. The sheet is now in a state where it can be easily formed, minimizing warping and creating the right properties for inflating. The finished panels are then aged to the T6 condition.
While automakers are interested, Scafe doesn’t know the extent of the market for rollbonded aluminum panels at this time.
“We worked with Ford to do a roll-bonded package shelf for the Jaguar XJ, but the problem was we were starting with the current design. To really get the structural roll bonding to work you have to start with that as the intended process when you do the design,” he says.
The heavy trucking industry has shown a lot of interest in the process. Aluminum cab manufacturers could replace heavy flat stock with roll-bonded panels. Scafe says one truck manufacturer has already inquired about friction stir welding floor pans onto the aluminum frame.
Tower has been involved in friction stir welding for several years now. The process is very simple. A tool is attached to an electric motor spun at 500 to 1,500 rpm. The bit looks a quarter-inch threaded machine screw though Scafe says that the design of the threads is critical to the operation. The friction heats the two metal surfaces and literally stirs them together. The result is not only a weld is clean and burr free, but a weld done without gas, adders or filler materials. It’s also extremely environmentally friendly process. The welding tool can be mounted on stationary machinery or mounted to a hydraulicdriven robot. Tower has a double-tip ESAB machine, the only one in existence as far as Scafe knows.
With a double stir you can weld from both sides at the same time. Though the tips don’t actually touch, the stirring action causes the weld to join in the middle, forming an hourglass shape. Tower is using this machine to weld the aluminum tunnel to the extrusions that hold the floor panels. The single-seam friction-stir weld not only looks sharp, but also seals the gas tank from the interior of the car. Tower has welded half-inch thick material and has experimented with welding 1-inch thick aluminum. The company also is working a tool that’s driven by a servo motor that allow the tips to be hollowed out so coolant can flow right to the tip. “We found through our trials that cooling that tip is critical,” Scafe says. “If you keep the temperature down you get a nice smooth burr-free weld.”
Tower participated in a trial with Ford Motor Co. to test the feasibility of using tailor- welded aluminum blanks. Tower was one of three companies that were asked to prepare 1,000 blanks. The MIG welder and laser welder never got to 1,000 samples in the allotted time.
Ford did a forming trial with the friction-stir welded blanks a year ago last December.
“Out of a thousand panels we knew that there would be 10 to 15 that were going to split,” Scafe says, “because they banged the fixture with the robot and we knew that weld was not on seam. The exact ones we told them that would split, split on the seam. Everything else formed perfectly.”
Friction-stir welding was used on a suspension piece designed for Lincoln limousines.
![]() |
Tower is working with Ford on the Ford GT production car. The GT utilizes rollbonded aluminum panels for the interior floor and fuel tank access panel. The center tunnel is friction-stir welded to the frame extrusions. |
“They were far, far more durable than anything Ford ever expected,” Scafe says.
Prior to the limo, Tower was ready to go to production on a friction stir-welded link for GM’s Epsilon platform. Tower made several prototypes before the project was cancelled.
Friction stir welding is licensed through the Weld Institute in the U.K. and cut its teeth in the aerospace industry. Boeing first used friction stir welding to build Delta rocket boosters. Traditional gas metal arc welding was a very time-consuming process and created quite a lot of repair and scrap.
“When Boeing went to friction stir-welding,” Scafe says, “they went to zero defects and zero scrap.”
Though Tower has used the process to manufacture low-volume suspension components, friction stir welding is still in its infancy. Scafe says that with energy prices where are and with the increase in the usage of aluminum, friction-stir welding could potentially be the future joining process for both the OEMs and automotive Tier Ones. But he cautions that the process has to be a part of the early design stage.
“You can’t just say, here’s our product show us how you can weld it,” he says. Scafe agrees that sometime in the next five years you’ll see products coming to market that were designed to utilize friction-stir welding as the joining process.
For every electronic play-toy you put in a vehicle you have to take weight out somewhere,” Scafe says. “The Jaguar XJ has 3,500 in the underbody. I think that there is a to get rid of most of those by using friction stir welding.”
Additionally, friction-stir welding has been on steel.
The tool wear is a problem but I think just a matter of development time. If can get the kind of mechanical properties of a friction stir welded joint in steel as do in aluminum,” says Scafe. “I think you quite a unique process there.”
Scafe says that 3-D welding is the thing the OEMs need to look at from the standpoint of an aluminum body in white. has developed software that can program a friction-stir-tipped robot to follow a complex contour.
It’s our plan to continue to look at what can do to supply sub-assembly using that process,” Scafe says. “It will grow to the point where they’ll be able to incorporate it into aspects of their body shop.”
More Stories
Your Guide to Filing a Car Accident Claim
Steps to Take Immediately After a Car Accident
What Makes SUV Cars More Prone to Accidents?