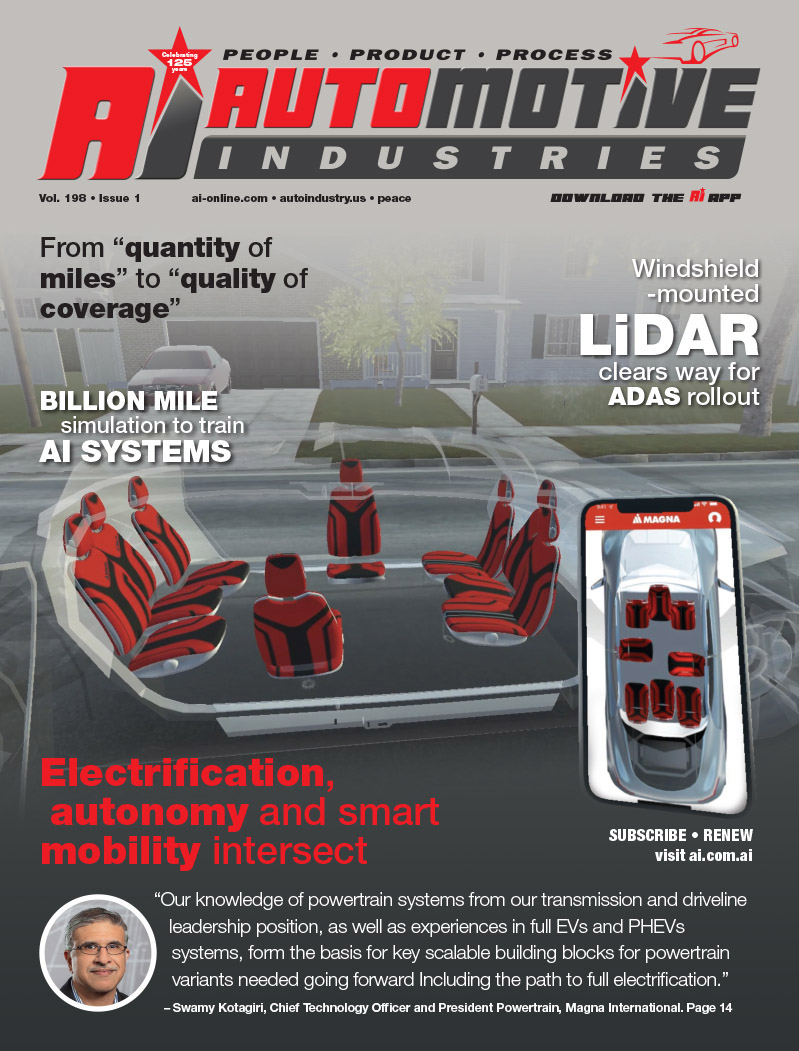
Advances in materials technology are allowing suppliers to meet three of the biggest concerns with carmakers today — reducing vehicle weight, lowering costs and improving fuel efficiency. And they are able to do so without compromising vehicle safety and performance.
New manufacturing processes and forming technologies are helping to make new materials more attractive to manufacturers on a cost basis. And thanks to the efforts of programs like the Department of Energy’s Automotive Lightweighting Program, more and more companies are being introduced to new materials and new applications for materials they might have taken for granted in the past.
“For the last 70 years, mild steel was the king of the hill,” says Joseph Carpenter, technology area development manager, automotive lightweighting materials, Office of Freedom Car and Vehicle Technologies at the Department of Energy. “But today, it’s getting to be a horserace between materials.
“In a lot of ways, we are in an age of cars like the early 1900s,” says Carpenter. “There were a variety of materials used back then — cars made of wood, cars made of steel, there were steam cars and battery cars. No one really knew at that time what the final outcome was going to be. Today, there are alternative technologies on the horizon that could change the auto industry again. We don’t know for sure what the fuel cell systems will be like, or the use of hydrogen for example. As the technologies change, so will the materials. It’s important for manufacturers to keep their options open.”
In Carpenter’s opinion, it’s going to come down to costs. “Lightweighting is a priority for car makers, and so is cost reduction. There are a lot of technically viable materials available today that carmakers can choose from to meet their needs. Magnesium is growing in popularity, as are carbon fiber reinforced polymer matrix composites,” adds Carpenter.
“High strength steel has been demonstrated to provide considerable weight reductions.
And then there are the glass reinforced polymers and the advances in aluminum. This is really an interesting time for material usage in automobiles,” says Carpenter.
As materials have evolved over the years, their usage in automobiles has changed. Following is a look at a variety of materials popular in today’s automobiles and the trends that affect them.
SteelSteel is still the most popular material used in cars today. Some sources put steel as high as 55 to 60 percent of all material found in a typical passenger vehicle. The continued popularity of steel is thanks in large part to advances in high strength steel and improved welding and forming techniques.
“Vehicles have to be stiffer now and more crash worthy and they also have to be lighter,” says Ronald Krupitzer, senior director of automotive applications for the American Iron and Steel Institute. “That’s why we have to have different materials than we’ve had before. Our approach to different materials is in the new advanced high strength steels that, incidentally, act more like a composites than steels. They are a combination of a soft phase and a very hard phase, just like a composite.”
The concept of these materials has been around for a long time but only within the last couple years have car companies gotten serious about actually applying larger amounts of advanced steals.
“We see some lead activities in Europe, at Volvo for example,” says Krupitzer. “There, there has been growing interest in dual phase steel. But also, we see now the Asians and the North Americans also taking these advanced steels onto new platforms. The new Epsilon platform uses a great deal of high strength steel, for example.
“Almost everyone now is developing new platforms and vehicles with higher amounts of these steels. But we are still only about half way there. We’ve got enough grades available now to satisfy most of our current demands, but not enough yet to satisfy everything. But we’re getting there. We have some grades that are produced with some product history, and we have other grades that are under evaluation and some that haven’t even been evaluated yet.” According to Krupitzer, advancements in steel are convincing car manufacturers to take a hard look at steel design, but in the lightweight context.
“They are looking at what they can achieve with the new steels that are out there. Advanced high strength steels are in fact more expensive per pound than traditional steels, but the mass that you can reduce by using the high strength steels is about equal to the price increase. So you can apply new, more expensive high strength steel and take out a certain amount of mass. So then you are buying less of it and you have a vehicle that still costs about the same as it did before, but it weighs less,” says Krupitzer.
New design methods like tailor welded blanks, laser welded blanks and laser assembly processing are improving the strength of advanced steels.
“We have found that vehicles have the potential to be stiffer and more durable. We’ve gotten data on weld fatigue that shows the higher strength endurance limits of the higher strength steel. So the potential is there if we can figure out the best way to use them in actual components.”
Powdered MetalThe automobile industry is the largest market for powdered metal. According to the Metal Powder Industries Federation (MPIF), approximately 70 percent of powdered metal production in the U.S. goes into the automotive market. The typical U.S. car contains about 37.5 pounds of powdered metal, compared to 16 pounds in the average European car and 15.8 pounds in the average Japanese-built car. The MPIF puts powdered metal parts in SUVs at more than 50 pounds. According to MPIF statistics, in the 2003 model year, powdered metal usage in the average North American car is expected to increase to 40.5 pounds.
“Usage of powdered metal in automotive applications has gone up in the last three to five years,” says Peter Johnson, director of PR and government affairs at the MPIF. “Big volume powdered metal parts are connecting rods, bearing caps, cam caps and transmission carriers. The biggest trend right now is matching the properties of wrought materials. Powdered metal parts are becoming higher strength and getting into new and higher strength applications.”
“The automotive industry is looking to powdered metal as a more cost effective way of making products,” says Michael Miller, vice president of sales at Chicago Powdered Metal. “Using powdered metal is a more cost effective process because you make parts to net shape and eliminate machining or other secondary operations. The trend over the last 10 years is to try and replace casting and machine forging with net shaped powder metal parts. The challenge is to make powdered metal parts with higher performance and better mechanical properties.”
As trucks get bigger and torque levels get higher and engines get more sophisticated, manufacturers tend to want to put these powertrain products in a smaller envelope. The components inside have be able to take higher loads.
“They can’t make the engine compartment bigger,” says Miller. “So products have to be thinner but have the same performance. That’s one of the challenges that the powdered metal industry is responding to pretty well. There have been a lot of successful powdered metal products. There’s been a trend to basically convert carrier assemblies that were previously machined cast into powder metal.”
Miller adds that new powertrain technology is a challenge to the powdered metal industry. CVT technology, for example, drastically reduces the number of parts needed for a transmission.
“Everyone has to adapt,” he says, “whether it’s plastic or steel or powdered metal. As technology evolves, there is going to be a natural shakeout. The industry has to keep pace. It has to keep evolving and finding new applications and meet the requirements the customer wants.”
CopperCopper content in automobiles has gone up thanks to increased electrical and electronic content. Today, a North American passenger car or light truck contains between 56 and 58 pounds of copper per vehicle, according to the Copper Development Association (CDA).
“The auto industry is under the three main constraints, which is they want to keep costs down, keep weight down and keep the volume of space that anything takes up to a minimum,” says Robert Weed, vice president, automotive at the CDA. “The cost is very obvious and so is the weight with the CAF? standards. The volume concern, not immediately obvious, makes a lot of sense when people think about just how crowded engine compartments are now, how consumers are looking for more space in the trunk, and how difficult it is to take any of the room between the liner and the structural roof of the car and the headliner to do anything.
Weed points out that those three drivers are giving the copper industry challenges in that the materials are expected to do more. “There is a lot of miniaturization if you will in the electrical and electronic components so that you’re dealing with something that is much smaller, yet still has to be as robust. So we would expect that even with the cost constraints, there will undoubtedly be more emphasis on alloys that provide better performance.”
Weed is confident that as automobile technology continues to advance, its success in other industries will allow copper to increase its market share within the automotive realm. “The auto manufacturers, the OEMs and their Tier 1 and Tier 2 suppliers, will be undoubtedly looking for systems of alloys, plating and probably even the plastics that provide them with an electric connector system that is more robust. Fortunately, the copper industry has been doing this for a number of years for consumer electronics.
The robustness had not been the same primary driver that it is with the automobile companies but the miniaturization and drive to lower cost and drive for improved performance as far as quality and connectivity has been going on in consumer electronics for quite a while. So the copper industry is well positioned with the knowledge that they have and the amount of funding that they’re putting into R&D to be able to cope with the requirements for the auto industry.”
Wood addresses other factors that influence copper consumption in automobiles, pointing out that copper increases as the amount of cast aluminum in a car goes up. Copper is used as an alloying element in the cast aluminum alloy, for example. “And we see a considerable increase in the amount of copper being used because of the increase in aluminum cylinder heads and engine blocks,” Wood says.
Alternative materials such as plastic optical fiber are attempting to cut in to copper’s automotive market share, but Wood is confident that copper usage will continue to increase, despite emerging competitors.
“The main thing that is going to drive increased copper content in cars is the need to conduct electricity. I don’t really feel that it was the need to send data signals that drove the increase in copper. The engineers were just extremely clever and most of the automotive engineers are very good at being able to find multiple functions for a component to perform. And so if they could send signals over the copper wires that carried electricity they were more than happy to do it because saved them having to put in additional wiring systems and design additional signal circuits. As they require those higher data transfer rates that make the plastic in the fiber optics look attractive, they still are going to have to conduct the electricity to the basic function they are trying to perform. So the copper is still very much going to be needed and undoubtedly still going to increase in content in vehicles. When fiber or one of those plastic materials takes some market share away from copper, the overall amount of copper in the car is still increasing because copper is being used for an electronic or electrical application.”
MagnesiumThe cost of magnesium is causing auto makers to take a closer look at new applications for the material. The Department of Energy puts the cost of magnesium at about $.57 per pound, down from the normal $1.40 to $2.00 per pound.
According to the DOE, you can use a half or third of magnesium to do the same job as steel. And in some cases, the cost of magnesium is cheaper than steel.
“Cost reduction is a major concern at the Big 3,” says Richard Opatick, executive vice president of the International Magnesium Association. “Magnesium gives you all the structural capabilities of the other metals that are available, but at a fraction of the weight. And magnesium offers a flexibility in design, in that you can cast some parts as one solid piece, such as an instrument panel. Some of the cast magnesium instrument panels replace pieces that may have anywhere from 12 to 20 pieces of welded steel. Thanks to the drop in price, folks in the automotive industry are reconsidering magnesium. In addition to instrument panels, magnesium has been used in intake manifolds, valve covers, seat frames, steering wheels, door frames. The lower price will only expand the applications.”
TitaniumA few years ago, titanium was just finding its way into motorcycle exhaust systems, mainly the outer shell of the muffler can on motorcycles in Japan, to the tune of 20 tons a year. Today, titanium usage is in the 400 to 500 ton per year range and is making gains in the automobile marketplace in the form of springs, exhaust systems, engine valves and connecting rods.
“There have been some major developments in the motorcycle world that have helped move titanium away from just being a cosmetic outer shell,” says Kurt Faller, president of Timet Automotive, a division of Titanium Metals Corp. “We’ve now proven that titanium can survive in the motorcycle world all the way into the header tubing bolting, right up to the exhaust port on the bike. It’s really pushed titanium into much higher temperature applications.”
The Corvette is the only car in North America riding on a titanium exhaust, but Faller predicts that to change. “We’ve got prototype through durability testing on a variety of applications and platforms on the exhaust side and in the not too distant future, we’ll see more than the Corvette with titanium exhaust.”
Suspension springs are another growing application for titanium. “A few years ago we started looking for a way to come up with a lower cost chemistry to target the automotive market, and did so with a spring alloy that we’ve named Timet Metal LCB,” says Faller. LCB is designed to provide the mechanical properties of the expensive aerospace alloys but with a lower cost chemistry and a little bit lower cost for manufacturing. Timet introduced the LCB on the 2000 Volkswagen Lupo FSI in the suspension spring in that car.
According to Faller, there has been growing interest in the use of titanium in connecting rods. “All of the Ferrari 12 cylinder engines use titanium connecting rods. The Porsche GT3, which is now just been identified come to North America, uses titanium connecting rods and has since it was introduced in 2000.
“We see growing interest for titanium connecting rods. We see titanium connecting rods being introduced in more than one vehicle in the 2005-2006 time frame and that is exciting.”
AluminumAluminum usage has grown to roughly 275 pounds per average vehicle made in the U.S., according to Aluminum Association. That’s up from about 250 pounds in 1999. Most of the aluminum, about 80 percent, is cast aluminum, with engines, transmission cases, water pump cases, suspension components and steering knuckles making up most of the cast aluminum parts.
“Sixty-five percent of engines built today are aluminum, and that will continue,” says Richard Klimisch, vice president, auto and light truck group at the Aluminum Association. “You get a lot of the weight out of a vehicle by using aluminum, improving fuel economy. I think you find that most new engines will be aluminum.”
Klimisch estimates that about 50 percent of the weight on a component is saved when it is converted from iron or steel to aluminum.
“Our selling point for aluminum is that customers can have the size and lose the weight by using aluminum. U.S. manufacturers are obsessed with cost cutting and it’s a tough time to penetrate the market right now. The biggest hurdle for aluminum is 100 years of steel in the auto industry. There is much more experience in the marketplace with steel than aluminum. Cost plays an issue as well.
Aluminum is still somewhat more expansive than steel, even though you only need to use half as much aluminum.”
Wrought products, such as extrusions and sheet based products are the next target for aluminum applications in the auto market. “There are a lot of specialty, low volume vehicles that are all aluminum,” says Klimisch. He sites the Audi A8 as an example and refers to the Jaguar XJ as a kind of breakthrough, in that it is a sheet based unitized body so there is no frame.
“The Audi uses a space frame, and there is a big argument about the best way to use aluminum, as a space frame or a unibody,” says Klimisch. “Most of the high volume vehicles are unibody, so some of the manufacturers, like Ford for example, have been particularly strong in their belief that the way to do high volume is with unibody, which is sheet based, whereas the Audi uses more extrusions and castings in the body.
“As we get into more concerns about side impacts, they are putting in sub frames. To do that, to put in that kind of structure, you almost have to go to aluminum because otherwise you are getting into big time weight.
“Manufacturers will tell you that you’ve got to use aluminum because they are putting more and more into the car, like airbags or padding, for safety related issues. All of that adds weight. To keep the weight in check, they have begun converting some parts from steel and iron into aluminum.
“The future and the present is influenced by fuel economy and safety,” adds Klimisch. “The main issue is to improve fuel economy without compromising safety. We believe that we have the answer to that, because aluminum is so strong that you can in fact make vehicles that are lighter, without compromising safety.”
PlasticThe use of plastics in automobiles is continuing to increase. Technology improvements have caused it to become lighter and stronger, making it a serious contender against other materials. The typical amount of plastic used today is about 260 pounds per vehicle in North America, with that amount expected to go well over 300 pounds by 2010, according to the American Plastics Council (APC). “The biggest trend in plastics right now is lowering weight and reducing costs,” says Bruce Cundiff, director of automotive for the APC.
“Plastic, as a family of materials, has the lowest weight. And because of the capability of combining parts with plastics, it reduces costs in addition to just reducing initial costs. Generally the reliability of plastic is greater. It does not rust, for example, and when designed correctly, it tends to last longer. So it can reduce warranty costs.” Plastics are used differently between North America and Europe, for the most part, because in Europe, gasoline prices are as high as $4.00 per gallon, says Cundiff.
“It’s not that it is used more or less, it’s that the cars themselves are generally smaller in Europe because the economics driving vehicle size is the price of gas. There are some differences, but by and large, the plastics used in Europe are the same ones that are used here.” Cundiff predicts plastics will find their way into new automotive applications.
“In the past, you’ve seen a lot of plastics used in non structural applications,” he says. “If you look at the interior of a vehicle for example, it is essentially owned by plastics. All the way from your door panels to your pillar covers to your seats, your urethane foam seating, your nylon carpeting. “On the exterior,” Cundiff says, “plastics essentially own the bumper systems, the exterior bumper systems, the fascias, and allow the energy management behind the fascia.
“Where you don’t see plastic used with the current architecture is in structural applications. There are a few exceptions, but in general I think that is going to be the trend in the future. You are going to see improvements in the technology as far as energy management and strength using plastic composites that will be making some inroads in the architecture of a car into the structure. I think that is going to be big trend as we go forward.
“The barriers to having that go overnight are the current investments that the OEMs have at their assembly plants in metal working equipment. From a business perspective, if I were an EOM and it costs only $1.50 per gallon of gasoline, there is really no incentive to scrap my investment in metal working and welding and assembly techniques that are currently in place to go into a new architecture that is still unproven at this time.”
Usage of polyurethane in automobiles has remained consistent.
“The biggest thing with polyurethanes is that they are getting lighter,” says Kevin Buck, automotive marketing specialists at Huntsman Polyurethane. “The trends in polyurethane follow those in plastics — reduce weight and reduce costs. As we reduce the weight, we take great care to maintain the physical property capabilities of the systems themselves.
“Another trend,” says Buck, “is that we are beginning to see quicker cycle times, so that we can make more parts with the same fixed capital investment in terms of tooling.” Plastic optical fibers are growing in popularity in the automotive community thanks in part to companies like Digital Optronics. In the past, heat has been a barrier for plastic optical fiber usage. Today, Digital Optronics has come up with a product that is compliant to 125 degrees C.
“In order to bring plastic optical fiber into the engine compartment, it really needs to be able to withstand 125 degrees C,” says James Walker, CTO at Digital Optronics.
“Today, most, if not all, plastic optical fiber in automobiles is used in the passenger compartment. We have a technology that we are developing that is able to withstand temperatures that will allow it, for the first time, to be used in the engine compartment.”
Walker puts the global amount of plastic optical fiber used in autos at around 12 million meters, “and that number will likely grow to 50 million meters or more within a few years at an 80 percent growth rate,” Walker says. “Plastic is going to save on weight and cost and fuel efficiency, but also usher in new capabilities in terms of audio and visual with high data rate gains in the automobile.” Digital Optronic’s grated index fiber, Walker says, can transmit information at a rate of several gigabits per second over 100 meters.
GlassThickness reduction is among the leading trends in automotive glass. PPG Industries is developing a product it calls Safe and Sound glass that is about 16 percent thinner than when it introduced its first auto glass product, according to Ed Littell, director of emerging technologies, automotive OEM glass business, at PPG Industries.
“Our Safe and Sound product is laminated, offering improved ingress resistance because of the plastic inner layer,” says Littell. “If you compare a standard 3.9 millimeter side window with a 3.9 millimeter Safe and Sound window, the Safe and Sound window is actually lighter. So now you have a window that is saving weight above the beltline, which is particularly important with SUVs.” PPG is providing Safe and Sound for the Lincoln Aviator.
The proliferation of glass roofs is another trend Littell sees shaping the auto glass marketplace. “The idea of increased visibility is driving that trend,” says Littell. “Windows are stronger and lighter than they have ever been. There has been a real expansion of the glass in vehicle areas. The trend has been to use more glass. The growth of SUVs and crossover vehicles illustrates a design trend where you’ve got glass now going completely around the automobile. We are taking the advantages of glass, which is its strength and its flexibility, and are able to fabricate thinner plies on the side glass.”
Pounds of Material in a Typical Family Vehicle
Material | 2001 | 2000 | 1999 | 1991 | 1985 | 1977 |
Regular Steel, tube, bar, rod | 1,349 | 1,373 | 1.399 | 1,341 | 1,481 | 1,995 |
High- and Medium strength steel | 351.5 | 339 | 328 | 240 | 217 | 125 |
Stainless Steel | 54.5 | 53 | 50.5 | 37 | 29 | 26 |
Other steels | 25.5 | 22.5 | 25 | 41.5 | 54.5 | 56 |
Iron | 345 | 352.5 | 358.5 | 431 | 468 | 540 |
Platic and plastic composites | 253 | 248.5 | 245 | 238 | 211.5 | 168 |
Aluminum | 256.5 | 245.5 | 235 | 166 | 138 | 97 |
Copper and Brass | 46 | 46 | 45.5 | 46 | 44 | 38.5 |
Powder metal | 37.5 | 36 | 34.5 | 23.5 | 19 | 15.5 |
Zinc die castings | 11 | 11.5 | 12 | 17.5 | 18 | 38 |
Magnesium castings | 8.5 | 8 | 7 | 3 | 2.5 | 1 |
Rubber | 145.5 | 144 | 141 | 135.5 | 136 | 150 |
Glass | 98.5 | 98.5 | 97 | 86 | 85 | 87.5 |
Other materials | 131 | 110 | 102 | 78.5 | 99 | 128 |
Source: AMM from industry reports
More Stories
Best Wheel Size for Off-Road Adventures: What People Get Wrong
Trusted Auto Collision Repair That Restores Both Performance and Peace of Mind
What You Need to Know About Tire Pressure in Winter vs Summer