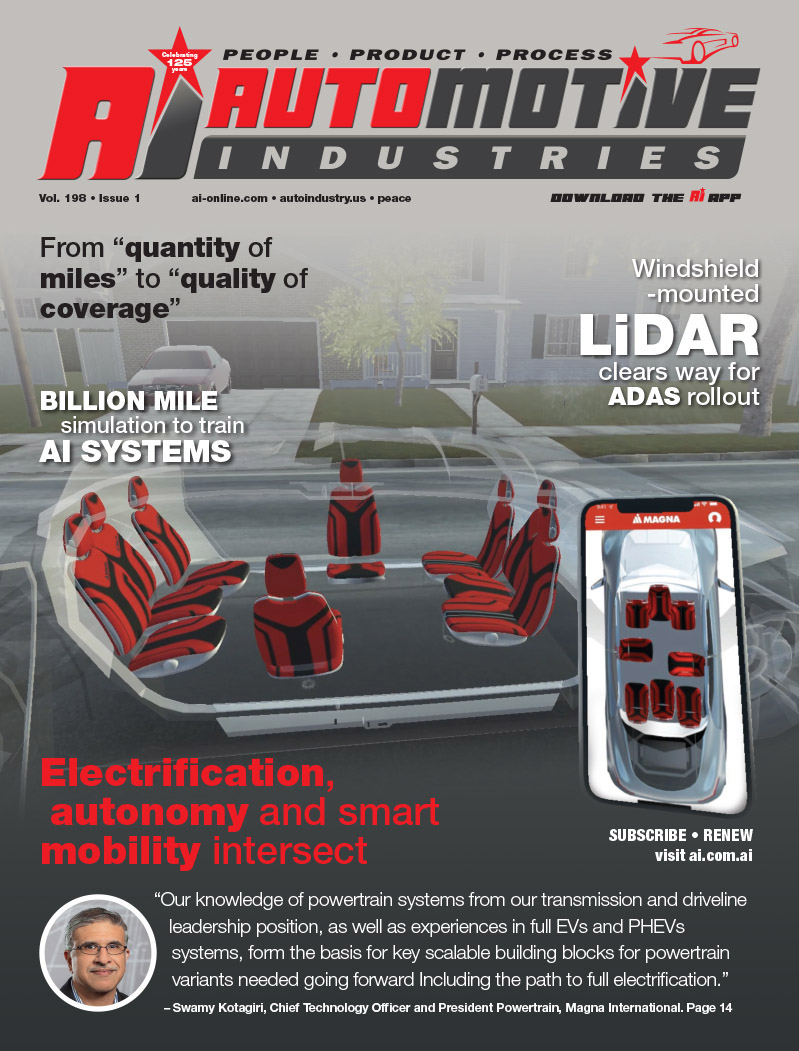
Ford’s Norfolk, Va., assembly plant introduces the next F-150 and a new flexible manufacturing system.
![]() |
This red F-150 Lariat 5.4 Triton is not only Job 1 for the new truck but is powered by Ford’s 100 millionth V-8 engine. No one at Ford is talking about where this historic truck will end up. The sticker shows that it’s slated for delivery to Prestige Ford/Lincoln/Mercury in Ponding Mill, Va. But rumors say that it may end up in the possession of a third generation Ford family member. |
“There’s been no vehicle more important to Ford Motor Company,” says chairman and CEO William Clay Ford, Jr.
Members of the launch team, on hand for the unveiling, couldn’t agree more. They say that this is the most intense launch they’ve ever been involved in.
Frank Davis, chief engineer for the F-Series says that this launch differs from previous launches in that the plant was involved well ahead of the actual launch date.
“(Plant manager) Mike Hom and I have been living together for the last 18 months,” says Davis. “Mike has been involved with the program much sooner than any plant manager has before. He’s been involved all the way from the confirmation prototype phase.” Hom also brought UAW product specialists to a large launch team that already included Ford engineers and representatives from the supply chain, as well as people from the Kansas City, Mo., and Dearborn, Mich., plants which are next in line to launch the new truck. The UAW workers assembled the confirmation prototypes and did assembly on the plant floor with the production workers as well. “They’ve got a lot of experience with the vehicle,” says Davis. “That’s a big, big deal.” The first production prove-out models were built in January.
“One of the things that this program has done better than anything else,” says Davis, “is deliver.” Davis says that the confirmation prototypes and first production prototypes were the best the company has ever seen. “That’s really based on the plant’s involvement,” he says.
The launch team has been in place at Norfolk since January and the extended launch program will keep engineers on site through the end of the year to make sure the quality indicators are just right.
![]() |
Product-specific tooling is mounted on vertical trays, horizontal gates and robot arms. At Norfolk, only 20 percent of the tooling is product specific. Model changeovers can be made by changing the trays and reprogramming the robots. Skilled trades need only disconnect the power and hydraulic lines, use a lift truck to slide one tray out, slide the other in and reconnect the power. Changing out tooling can take anywhere from four hours for a small vertical tray to eight hours for a larger horizontal gate, a time savings of about 70 percent over the old method. |
![]() |
All 3,500 welds are done by robots. The 256 Kowasaki robots come in three sizes and are used for material handling, welding and sealing. All of the tools are either electric or pneumatic. Ford says that the next step will be to change over to servo-driven weld guns. All critical sheet metal for the F-150 is stamped at the Woodhaven and Dearborn, both Mich., stamping facilities and shipped by railcar to Norfolk, Va. Woodhaven and Dearborn will also supply the Kansas City, Mo., and Dearborn assembly plants. Ford has brought some sub-assembly back into the plant. Floor pans and pickup boxes are now built in-house. The supply chain for Norfolk is linked on-line to the plant’s weekly scheduling system. By having suppliers ship only the number of parts needed to meet the schedule, Norfolk can reduce on-site inventory to about 10 hours of off-line components and two hours of line-side parts. Russo says that there is a push right now to build a supplier park around Norfolk. Ford would like to have the plant’s primary suppliers set up shop within a 100 mile radius of the facility. |
Ford’s flexible manufacturing system divides the body shop process into 16 distinct functions, or cells, built from just 294 standard components off of a standardized footprint. Each of the 16 cells determines a segment of the building process. There are three different welding cells, two cells with different types of tool trays and one for applying adhesives or sealant — even the pallet that transports the body is counted as one of the sixteen cells. Each process in the body shop is a subsystem built up from the appropriate type and number of cells needed to complete the process. If a process has four steps, then the appropriate cells are chosen to carry out those four steps.
The cells are all configurable, having standardized connections for electricity, air, water and hydraulics. Only product-specific tooling is changed and robots and computers are reprogrammed to accommodate different models and mixes.
“We took a tremendous amount of complexity out, which helps the launch process, the maintenance process, the uptime and the whole reliability and integrity of the system,” says Roman Krygier, group vice president, manufacturing and quality.
In the case of Norfolk, F-150 bodies ride on adjustable underbody pallets with tooling specifically designed for that vehicle. Both the regular cab and SuperCab ride on the same pallet, though the SuperCab pallet has an added section bolted to the back. The SuperCrew has its own pallet. Frank Davis says that the F-150 is the first vehicle specifically designed for the new manufacturing system, utilizing a common architecture design. This will allow Ford to run different variations of vehicles down the same body lines with minimal changeover time.
As the pallets transfer down the line, a signal is sent to the specific cell which tells the robots in that cell what body style to weld. Ford’s flexible body shop is able to handle two platforms with up to four derivatives off of each platform. Space has been engineered into the body shop at Norfolk in the case that additional platforms need to be added.
William Russo, director, manufacturing engineering vehicle operations, says that if Kansas City wanted to add a model that Norfolk was currently building, production could be ramped up in about six months. The flexible system can also be used to increase volume by doubling up cells.
Ideally, Ford could run front-wheel drive, rear-wheel drive, unibody and body on frame vehicles down the same line, though Krygier admits that they probably wouldn’t build cars in a high-volume truck plant like Norfolk.
“But as we go through cycle plans and look at opportunities,” Krygier adds, “we can shift to different product or go to a derivative that looks completely different. It’s not inconceivable to do an SUV on the same line as the pickups.”
Russo says that Ford is converting the body shops to the new system as they do model changeovers. The Kansas City and Dearborn truck assembly plants will be on-line next year, followed by the Chicago, Ill., assembly plant Freestyle, 500, Mercury Montego) in 2005 and Auto Alliance International in Flat Rock, Mich., (Mustang and Mazda 6) in 2006. By mid-decade, about half of Ford’s body shops, trim and final assembly lines will be flexible. That number will grow to 75 percent by the end of the decade.
The flexible manufacturing systems cost about 10 to 15 percent less to install than hard tooling, plus there is an added 50 percent savings in changeover costs as a result of the standardization and re-use of equipment.
With significant savings in equipment costs and a reduction of floor space needed for the new body shops, Ford expects to save up to $2 billion over a 10-year cycle. Krygier says that the system also offers the opportunity to leverage plant capacity.
When all of Ford’s plants are standardized, Ford will have the ability to change the mix of models across facilities.
Russo says that one of the as-yet-unused advantages of the flexible manufacturing system is a reduction in the number of platforms. Ford currently has 48 platforms, and while Russo won’t give specific numbers, he says that the number will be reduced into the teens by the end of the decade.
Along with all of the body shops, Ford is going to a cell-based flexible approach in its paint shops as well. Ford will have about 31 cells in the paint shop that will be able to handle multiple car and truck body styles.
“If you’re going to have a flexible body shop,” says Krygier, “then you’d better have some flex in paint or you’re just going to move your constraint from one area to another.” Ford will also institute common build procedures in the trim and final assembly operations allowing them to adapt quickly to option and content changes.
More Stories
Best Wheel Size for Off-Road Adventures: What People Get Wrong
Trusted Auto Collision Repair That Restores Both Performance and Peace of Mind
What You Need to Know About Tire Pressure in Winter vs Summer