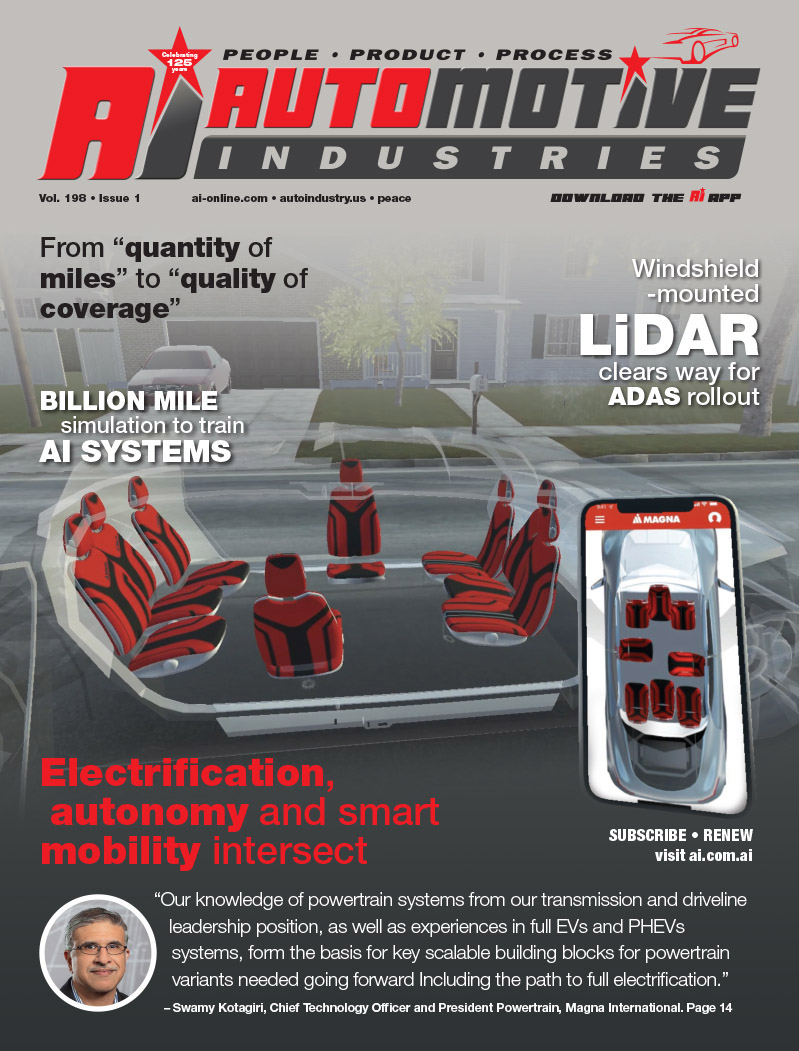
Customers are beginning to make greater demands for quieter automobiles, and because of this, automakers have begun to attack sound inside the passenger compartment with greater ferocity. Thanks to advanced engineering capabilities and improvements in materials technologies, what used to be thought of as an uncontrollable source of unwanted sound is now fair game in the quest to reduce interior noise. From front and side windshields, to tire wells and the engine compartment itself, nothing has been left unexplored when it comes to finding new ways to ensure a quieter driving experience.“There is an increased sensitivity toward noise, from a personal standpoint and a societal standpoint,” says Daniel Maguire, technical director , active systems, at Cooper Standard. “You see increasing links between noise and vibration and fatigue, noise and hearing loss.
There is a technical interest coming about, and you also have personal interest. In the very high-end vehicles especially, it’s clear that the companies are devoting significant effort in the development of the vehicle to minimize the noise and vibration harshness that exists in these vehicles. And that is something that is of late. When you look at a highend vehicle and consider the amount of attention and money that is spent on the vehicle’s ride quality and NVH characteristics, it is significant and very well representative of the importance that you see.”
Cooper Standard’s product line includes passive and active vibration control components that are intended to reduce both vibration and the noises created by the vibration within the vehicle.
“Our entire product line goes to vibration control, but then noise control as well,” says Maguire. “The reasoning is that if I’m sitting in a car and the engine is running, because it is a piece of rotating machinery, it is creating some broadband noises, but more significantly it is creating a lot of tonal noises at varying frequencies. I’m sitting in my vehicle and I’m hearing noise and that noise is propagating through the firewall and up to me.
The vibrations that are caused from the engine are propagating their way through the mechanical system. The vehicle is essentially a collection of devices that are waiting to be excited by particular frequencies of energy and they are going to make noise.”
Maguire compares it to a pebble in a pond. “You have engine noise and muffler noise, but then also noise that is created by vibration of the engine and muffler. It’s that composite that creates the whole spectrum of noise that drivers and passengers are subjected to.”
Cooper Standard’s goal, according to Maguire, is to isolate the engine from the rest of the vehicle, in part because of direct connections to the occupants of the vehicle, but also because “everything in the vehicle is a musical instrument waiting to be excited. The less energy that is making its way through the vehicle, the less excited the structures.”
Cooper Standard isn’t the only company that is targeting the engine as the main source of noise and vibration. Headquartered in Europe, Carcoustics Inc. offers blow molded engine encapsulation as a solution for quieting the passenger compartment.
![]() |
Carcoustics uses blow molded engine encapsulation to not only quiet engine noise, it can also be tuned to a specific acoustic standard. |
Ebbitt is seeing a lot of people ask about high temperature materials that can be put directly on the engine. “When you have something making noise, all of the energy is concentrated into that one spot. And then as it propagates away from there, it takes up more and more real estate as that noise propagates. If you want to get the noise where it is all concentrated, you have to go directly to the source.”
Carcoustics offers acoustics throughout the entire vehicle, including the engine compartment, the interior and the trunk.
The company is currently exploring the wheel wells and the body board for additional noise reduction within the passenger compartment.
![]() |
Carcoustics has added an acoustical feature to the wheel-house liner to help reduce the amount of road noise that enters the passenger compartment. |
Another area being explored for noise reduction by Carcoustics is the dashboard vents. “These days vents are the loudest points in an automobile,” says Hoffman. “To make a phone call in the car, you have to turn the air down and sweat through the call. Carcoustics is intensively working on noise abatement between the air outlet and the vent system. We have produced absorption function on the way between the vent and the interior of the vehicle, working with HVAC companies to fine tune this so that it will be a very efficient system to prevent the noise from entering the vehicle.”
Carmakers are beginning to realize that interior noise levels are directly equated to perceived quality. Products such as Carcoustics blow mold engine encapsulation can actually be tuned to a specific acoustic standard.
“Acoustics is a way for carmakers to differentiate their products,” says Hoffman. “To quiet a BMW is one thing. To tune the acoustic solution so that it sounds like a BMW is another.”
“The consumer is perceiving a higher quality vehicle when it’s quiet inside,” says Thomas Laboda, automotive market development manager, films, at Solutia Inc. Solutia addresses sound at the windshield with a variety of film products, the most recent being its Vanceva Quiet, an interlayer designed to be laminated between two pieces of glass, suitable for all glazing positions.
“I’m seeing laminate glass as one of the major trends in noise reduction and the reason is that engineers are fighting for tenths of decibels,” says Laboda. “All of a sudden they can swap out the side glass, change the windshield and get six decibels of noise reduction. Everyone used to assume that you had to live with the sound that came through the windows.
Now all of a sudden it’s possible to change a glass and gain a major reduction in noise. If you look at the vehicles that have launched purely based on acoustics, the Buick Rainier, Lincoln Navigator, Lincoln Aviator and the ultra luxury packaged Lexus LS430 all offer laminated glass. When you change from tempered to laminated glass, you get a significant reduction in noise because in the past, the windshield was always the weakest link of where the sound was pouring into the interior.”
An added benefit to laminated glass, according to Laboda, is weight reduction, an ongoing struggle for carmakers as more and more components are added to vehicles, such as entertainment systems, navigations systems and other increasingly “essential” items to today’s drivers.
While he couldn’t offer specific weight comparisons between laminated and tempered glass, Laboda offered an example of Vanceva Quiet’s weight reduction capabilities.
![]() |
Laminated glass is a growing solution to quieting noise from the windshield. Vanceva Quiet is an interlayer developed by Solutia that is designed to be laminated between two pieces of glass, suitable for all glazing positions. |
“Customers are looking for better sound quality and certainly there is a tremendous response by the OEMs and the integrators to recognize that and find solutions,” says Dan Sophiea, segment manager for Dow Automotive. “Customers are demanding quieter vehicles. I think there’s a very good effort to improve the acoustics. It’s well thought of in advance. It’s designed into the vehicle at the very beginning.”
![]() |
Vanceva Quiet was recently incorporated on the Buick Ranier. |
Dow Automotive offers acoustical foams under the name BetaFoam that are cavity filling materials for the body structure. They go into any body cavity structure, but are typically used in the rockers and the pillars, for example. Predictive modeling plays a large part in the design of quieter vehicles.
“You need testing to validate the model,” says Sophiea. “You need to be able to generate empirical data. The NVH community has done an excellent job of developing the right models and the suppliers like Dow are doing an excellent job of developing the right material properties so that the correlation is fairly high.”
“Ten years ago, we didn’t really know materials that well from an analytical standpoint,” says Ebbitt. “If we were looking for something new, we would make it and test it and then decide if it performed how we had hoped. There was a lot of cut and try. Today, there are a lot of analytical tools to guide us as we are coming up with new materials. We can actually try out a lot of stuff on the computer first and then we can see if something will work in a particular application.” Thanks to companies like LMS International, all of the guesswork can be removed long before a component is ever manufactured.
“It’s important to realize that new car design does not happen from a blank sheet of paper,” says Mike Albright, business development manager, engineering services North America at LMS International. “It happens in an environment of legacy products, early stage prototypes, the competitive benchmarks and all kinds of ongoing process in the test domain that make data available in various forms.”
LMS provides the testing systems, multidisciplinary virtual prototyping software, engineering services and collaborative engineering tools. The company provides the software tools needed to make noise and vibration engineering decisions as early in the design cycle as possible.
![]() |
Dow Automotive offers acoustical foams under the name BetaFoam that are cavity filling materials for the body structure. |
![]() |
Sysnoise predicts sound waves and the structural vibration induced by fluid loading effects onto a structure. The program calculates a wide variety of results such as sound pressure and radiated sound power, acoustic velocities and intensities, contributions of panel groups to the sound, energy densities, vibro-acoustic sensitivities, normal modes and structural deflections.
LMS Test.Lab is a dedicated measurement solution for noise and vibration testing and analysis. Designed for laboratory automation, LMS Test.Lab focuses on performing specific measurements such as engine run-ups, real time octave tests, modal impact tests, if necessary in the local language. Various applications can be rescheduled into a new dedicated measurement workflow. Templates launched from the user’s desktop describe complete testing procedures including measurement setup, layouts with reference curves and operator directives.
Noise and vibration is a reality around the globe, but how it is perceived varies depending on where the vehicle is going to market.
“Outside of North America, there is more of a focus on pass-by noise. In essence, let’s eliminate the noise near the source and thereby reduce the level that is transferring into the vehicle,” says Kevin Buck, marketing manager at Huntsman Polyurethane. “To address this, formulations designed for the engine undertray and covers, engine side insulators and bonnet liners have been developed. It is anticipated that as the vehicle platforms become more global, the pass-by focus will become more of an issue in North America.”
Huntsman Polyurethane specializes in the supply of polyurethane technology for use in automotive applications, including flexible foam technology for front and rear seats, sound insulation/acoustic, headrests, armrests, structural technology for door panels, rear shelves/package trays and elastomeric technology for use in steering wheels and interior trim as well as semi-rigid technology for use in applications such as dashboards and energy absorbing foam.
Noise and vibration standards will become more universal as product development becomes more global. The U.S. government may not be as demanding about vehicle noise control as Europe, but ultimately, the market will continue to push NVH issues, not politics. Customer demands for improved interior sound quality will only increase, even as changes in material technologies continue to expose new areas within a vehicle for reducing noise and vibration.
More Stories
Best Wheel Size for Off-Road Adventures: What People Get Wrong
Trusted Auto Collision Repair That Restores Both Performance and Peace of Mind
What You Need to Know About Tire Pressure in Winter vs Summer