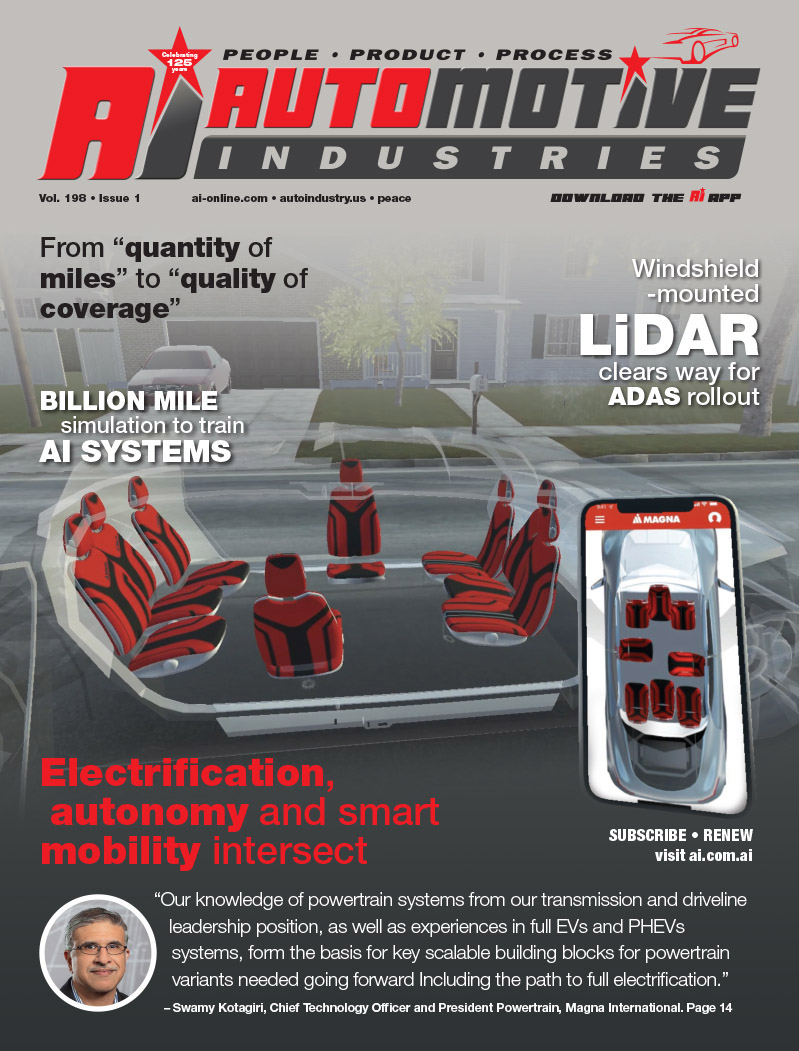
Conventional hydrides limit HO2 development.
There is a growing consensus among industry experts in Tokyo that conventional metal hydrides and pressurized hydrogen storage systems cannot meet the fueling requirements of fuel cell vehicles.
Research results reveal that the hydrogen absorption rate of most commercially available metal hydrides is 2 percent, far too low for economical operation and making it virtually impossible to meet the targeted 312 mile range.
One of the strongest critics of metal hydrides for fuel cell vehicles is hydride expert Seijirau Suda, professor of chemical engineering at Tokyo’s Kogakuin University and president of Materials Energy Research Institute (MERIT), a small research company.
Suda, interviewed recently at his campus office, participated in a U.S. Department of Energy ‘workshop’ that comprised 45 hydrogen experts from U.S. universities and national research institutes along with three foreign professors from Germany, Sweden and Japan. Their focus: hydrogen production, storage and usage. The workshop was organized under the auspices of the Bush administration ‘Freedom Car and Fuel Initiative.’ Suda strongly endorses the Energy Department’s conclusions that government funding should not support research in liquid and/or pressurized gaseous hydrogen, including ‘conventional’ metal hydrides. Funding should go toward future and innovative technologies such as ‘light metal hydrides’ including sodium-aluminum hydrides (NaAlH4) and sodium borohydrides (NaBH4).
It is also premature to make major investments in carbon nano-technology for automotive applications.
“Hydrogen storage capacity has not yet been confirmed. There still are no standard procedures that can confirm the materials’ properties and characteristics,” Suda says.
He notes that sodium-borohydrides have far greater hydrogen absorption potential than conventional metal hydrides: NaBH4, according to Suda, can generate up to 10.8 percent of hydrogen by hydrolysis on a weight basis (i.e., the weight of stored hydrogen as a percentage of the weight of the total storage system).
“As a result,” he says, “NaBH4 has a weight, size, cost and power control advantage over metal hydride and liquid hydrogen and a weight, size and cost advantage over pressurized hydrogen.” Despite his support for borohydride research, Suda does not expect ‘light metal’ storage materials to be affordable for fuel cell vehicles for another 20, perhaps 30 years. However, he believes borohydrides might be available within three to four years for ‘mini’ fuel cells to be used in laptop computers and cellular telephones. Suda believes that within five years the cost of a mini-fuel cell with 100cc displacement could be brought down to $2.
In the auto sector, Suda says Toyota and Millenium Cell Inc. are investing heavily in borohydride R&D.
Meanwhile, Suda feels NEDO’s support of ‘compressed’ hydrogen is yet another example of throwing money at a problem with little chance of success. Suda says that even if pressure levels increased to 1,000 MPa, cars will not be able to carry 5 kg (11 pounds) of hydrogen and travel distances of at least 500 km.
He also does not feel it is possible to reduce fuel cell and/or vehicle weight sufficiently to compensate for storage limitations of metal hydrides and compressed hydrogen.
Although Suda believes Japan is the world’s most advanced country in fuel cell technology, particularly in the automotive sector thanks to Toyota and Honda, he expects the U.S. to pull ahead in hydrogen storage technology.
“Until we solve the hydrogen storage problem,” he concludes, “it is not possible to establish a hydrogen infrastructure within 20, even the next 30 years.”
This article was provided exclusively to Automotive Industries by J•REPORTS, a new information service offering in-depth coverage of automotive technology based in Tokyo. For additional information about this and other studies and prices, contact jreports@attglobal.net
More Stories
Your Guide to Filing a Car Accident Claim
Steps to Take Immediately After a Car Accident
What Makes SUV Cars More Prone to Accidents?