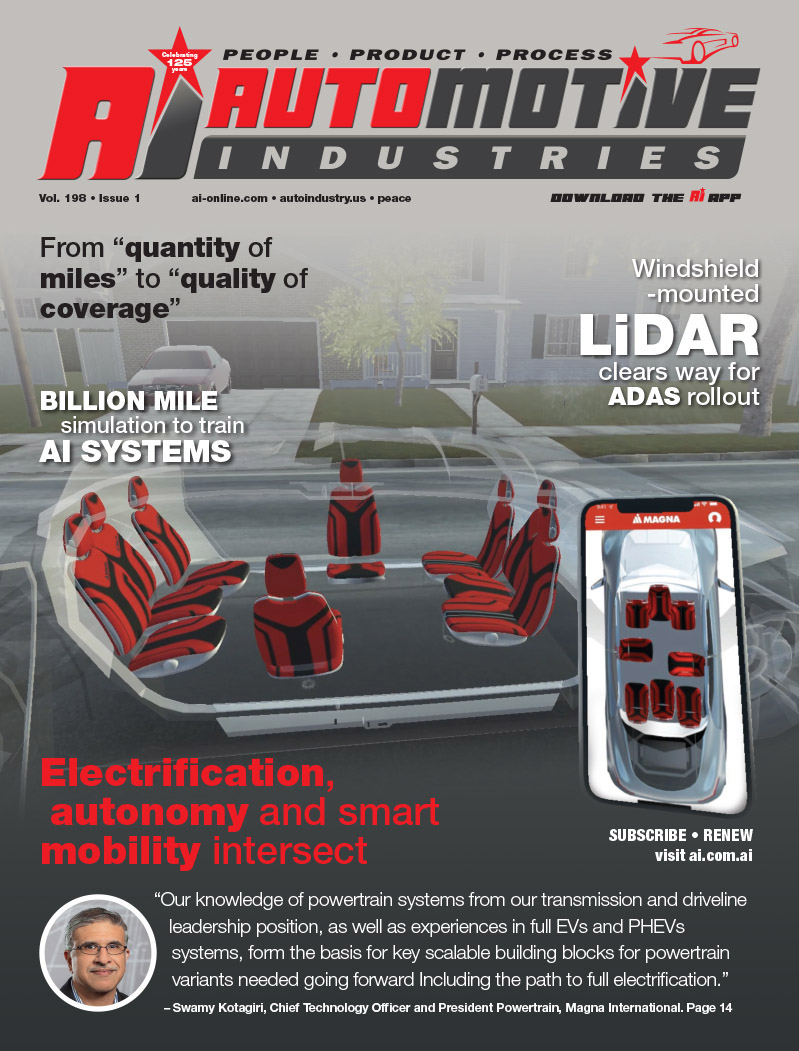
![]() |
Ford’s Windsor, Ontario, Canada, engine plant is the first online with the new flexible powertrain manufacturing system. |
Beginning with the launch of the new Ford F-150, Ford is building a network of flexible engine and transmission plants designed to “respond quickly to market needs, while improving quality and manufacturing efficiency.”
With quickness to market and shortened retooling times as goals, Ford is hoping that its global flexible manufacturing strategy will give it a competitive advantage and most importantly, save money.
Ford is planning to launch 65 new products over the next five years and expects to save as much as $2 billion over the next decade through the use of flexible manufacturing.
Three main elements are at the core of Ford’s flexible manufacturing strategy for powertrains: common engine architectures; communized manufacturing facilities; and modern, flexible, computer numerically controlled machine tools (CNC machines) that can be easily retooled and reprogrammed to perform new tasks with minimal disruption to production.
The new CNC machines were installed last year at Ford’s Windsor, Ontario, engine plant to manufacture its new 3-valve cylinder head for the 2004 Ford F-150 pickup. The same type of flexible CNC machines are being installed at its Lima, Ohio, plant to manufacture Ford’s new 3.5L, V-6 engine, as will be installed at Ford’s Cleveland Engine Plant No. 1 in 2004 and at Ford’s Romeo Engine Plant in 2005. The new flexible manufacturing system is also being installed at the company’s Dagenham and Bridgend engine plants in the U.K. later this year.
![]() |
Ford uses virtual manufacturing techniques to eliminate any problems long before any actual materials are involved. |
![]() |
“We are setting up our systems so that we can quickly respond to our customers and the demand of the market by being able to change from one product to another, or to instill upgrades within an existing family. We are making sure that our facilities are able to run more than one type of architecture down the line, in order to flex with the demand.”
The advantage of CNC machining is that rather than requiring a complicated process of removing old-style dedicated cutting or boring machines and installing new ones, the CNC machines can be retooled and reprogrammed internally, with little or no interruption in production.
“With some of our new CNC systems that we are putting in, we are running on universal adapter plates,” says Geary. “We’ve set a kind of square boundary that we are using with all of the automation, all of the clamping, and by changing that adapter plate and by changing programs and tools, we can run different products down that same line.
“We’ve got systems where we are tracking our tools,” Geary adds. “We’ve got microchips set up within the tool holders so we track the tools as they leave the setup crib, onto the CNC machines. We get good tool life data off of that, as well as quality information and we track that tool right back into our tool setup cribs. So we are constantly learning as we go forward. We are making sure that the right tools go in the machines at the right time through that technology as well.”
In order to monitor quality during production, each engine built at Lima, Romeo, Cleveland, Dagenham and Bridgend will develop an engine “birth history” that allows plant engineers to track every stage of production, so any quality control issues can be tracked back to its source and affected parts taken out of production.
“We are using microchip technology to create the birth history,” says Geary. “Each cylinder head for example gets attached with a birth history through microchip technology. As it goes through the flexible CNC, there are over one million possible paths that head can go through as it proceeds through the system. So we track that head all the way along the system — exactly what machine it went in. We know what tools were in the machine when it went through that machine.
“In the past, if you ended up with a quality issue at the end of the line, you had to take times of when you think it started, or perhaps you have evidence of a part that had a particular quality issue, and then you have to go back further to make sure you’ve captured all of these. And then there is a large sorting process you would have to go through to identify good parts and bad parts. With the birth history system, we know exactly which are the good parts or the bad parts.”
While Ford’s engine birth history helps trace problems that might have occurred during the manufacturing process, James Cheng, section supervisor, virtual manufacturing for manufacturing engineering, powertrain operations, Ford Motor Co., is using virtual manufacturing to eliminate problems long before any actual materials are involved.
“We have 3-D CAD models of the machines, of the fixtures themselves, the spindle, so we can simulate the whole process. We can virtually machine a part,” says Cheng. “The model would have ordered the machine CAD geometry, the picture and part, and we can do animation or simulation to see how the machine will cut the part. Remove the metal. We can also calculate the cycle time.
![]() |
Newly-CNC-machined Ford F-150 3- valve heads roll down the line at the Windsor, Ontario, Canada, powertrain manufacturing facility. |
According to Cheng, the virtual manufacturing tool deployed by Ford Powertrain is based on E Manufacturing software from Tecnomatix Technologies Ltd., a provider of software for manufacturing process management solutions headquartered in Israel, with offices around the globe.
“It is a web-enabled solution that is the core for our virtual machining strategy,” Cheng says. “We use it to balance our production line, as a means to allocate operation according to machine specification, enabling us to optimize our productivity with the least number of machines.”
Common plant layouts are another key enabler to Ford’s flexible manufacturing system. According to Ford, engine plants that are thousands of miles apart are getting the same floor plant, the same manufacturing machinery in the same layouts, in order to standardize production.
“What we’ve done is we’ve given the teams a challenge to not only have common processes, but also have common suppliers,” says Geary. “So the exact same machines that are going in North America are also going into our European plants. They are making different products, but we are using the same automation suppliers, the same CNCs, the same gantries, and so those companies are learning with us as we go forward on commonality.
“As we launch our new facilities, we will evolve, but we won’t go through huge revolutions like we used to. In the past, we used to lay out a transfer machine and the next team that came in to do the next head had a different idea of how they wanted the machine. It probably went to a different supplier to buy the machine tool from, and we’d start all over, creating a new transfer line and going through the learning curves again, around the initial failure modes and what has to happen in order to put corrective actions in place for those.
“Now, we are replicating but also evolving,” adds Geary. “If we find an issue, then we are going to make corrective actions to improve that.” Standardized layouts and the use of identical CNC machines in each plant help Ford reduce the number of spare parts it has to keep on hand at a given plant. According to Geary, the new plants typically have one set of shared common spares for each cell for each system, than each machine, resulting in inventory cost savings.
Another advantage to identical CNC machines, says Geary, benefits plant employees.
“Now when we train a new employee on a CNC machine, we train them once on a machine and they know how to operate almost all of the machines,” says Geary. “In the past, if we trained someone on a transfer line, we taught them a specific operation and they could only run that operation. Now there is some flexibly for them in the amount of operations and parts of the business that they can participate in, as well as the learning curve for them — once they’ve learned one, they’ve learned them all.
“We’ve also gotten feedback from employees in the plants where we’ve already launched the flexible manufacturing system and they see this as job security. Ford doesn’t have to buy new transfer lines anymore. It’s reprogramming and buying new tools.
Employees see the potential of being able to evolve with the products into the future.”
More Stories
Your Guide to Filing a Car Accident Claim
Steps to Take Immediately After a Car Accident
What Makes SUV Cars More Prone to Accidents?