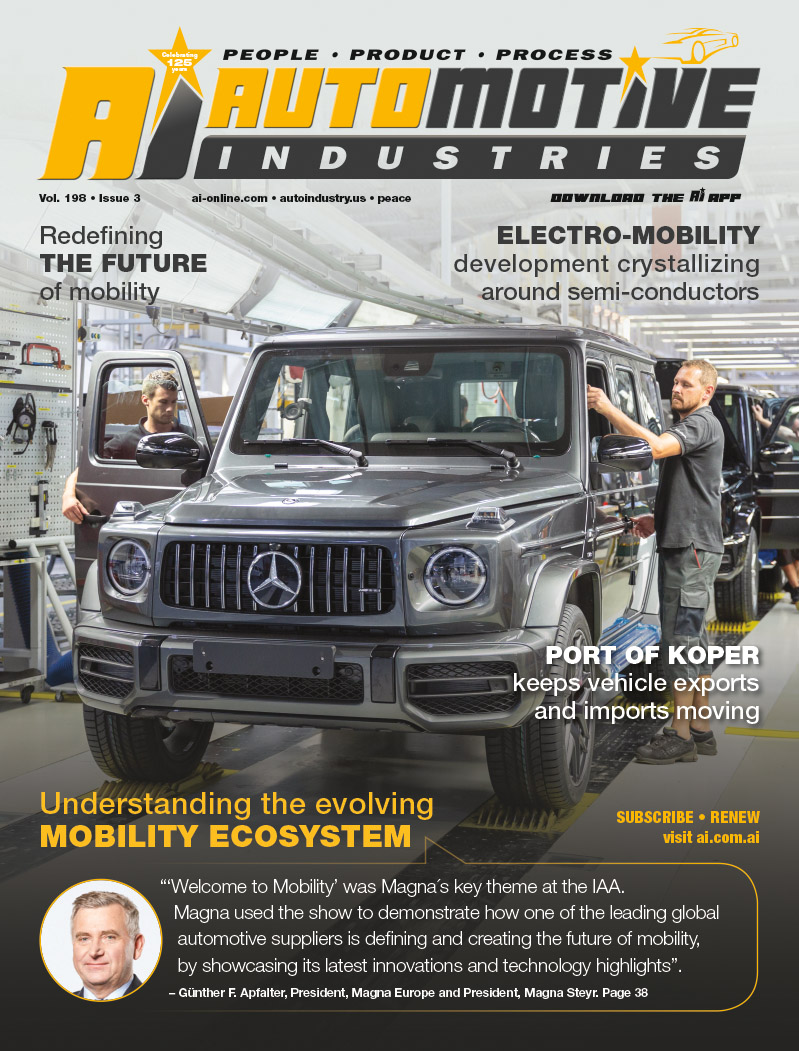
Electric rear-drive Smart roadster is only one of the development tools at WaveCrest’s disposal.
![]() |
The power electronics fit into the floor of the vehicle’s trunk. Schaum says that they will get much smaller as development continues. |
Preparations are underway for an afternoon grand opening celebration with name tags neatly lined up and information stacked on a nearby table. But what catches my attention is the dark blue Smart roadster that’s sitting up on a hoist in the backroom. The roadster is the latest tool in the development of a commercially-viable wheel motor for the auto industry.
“We picked the Smart roadster because it’s a rear-wheel-drive vehicle and we were able to remove the DaimlerChrysler powertrain and install our powertrain with minimal alterations,” says Richard Schaum, vice president and general manager of vehicle systems for WaveCrest Laboratories.
“We didn’t have to change any sheet metal. We didn’t even change the stack for the convertible top.”
From above, the Smart roadster looks no different from any other Smart, but one look underneath reveals some interesting differences. The Smart is equipped with WaveCrest’s Adaptive Motor System, a series of electronic controllers, mounted in the floor of the trunk, that power two 88-pound wheel motors.
The Smart’s tube suspension we extended by about 10 inches and the track bars were moved back to make room for the wheel motors. The system is powered by 10 sets of MOSFETS, solid state controllers that handle the high levels of current needed to power the coils inside the motors.
“At this level of development there are actually five levels of coils,” says Schaum. The MOSFETS are mounted to aluminum extrusions that are cooled by the vehicle’s liquid cooling system.
![]() |
This Smart roadster will be used to develop WaveCrest’s wheel-motor technology. |
The wheel motors are air-cooled. Air is brought in from a cold spot inside the vehicle so the system won’t be exposed to dust or water. A small fan is used to blow air into the tubes. The brake rotors are about 0.5 inch thick drilled for ventilation and scalloped for asthetics.
The Smart mule uses four nickel-metal hydride batteries to power the system that will be replaced by WaveCrest’s own battery technology when it is ready.
The Rochester Hills facility will also have an algorithm test-bench which will simulate a vehicle with four wheel motors.
More Stories
Best Wheel Size for Off-Road Adventures: What People Get Wrong
Trusted Auto Collision Repair That Restores Both Performance and Peace of Mind
What You Need to Know About Tire Pressure in Winter vs Summer