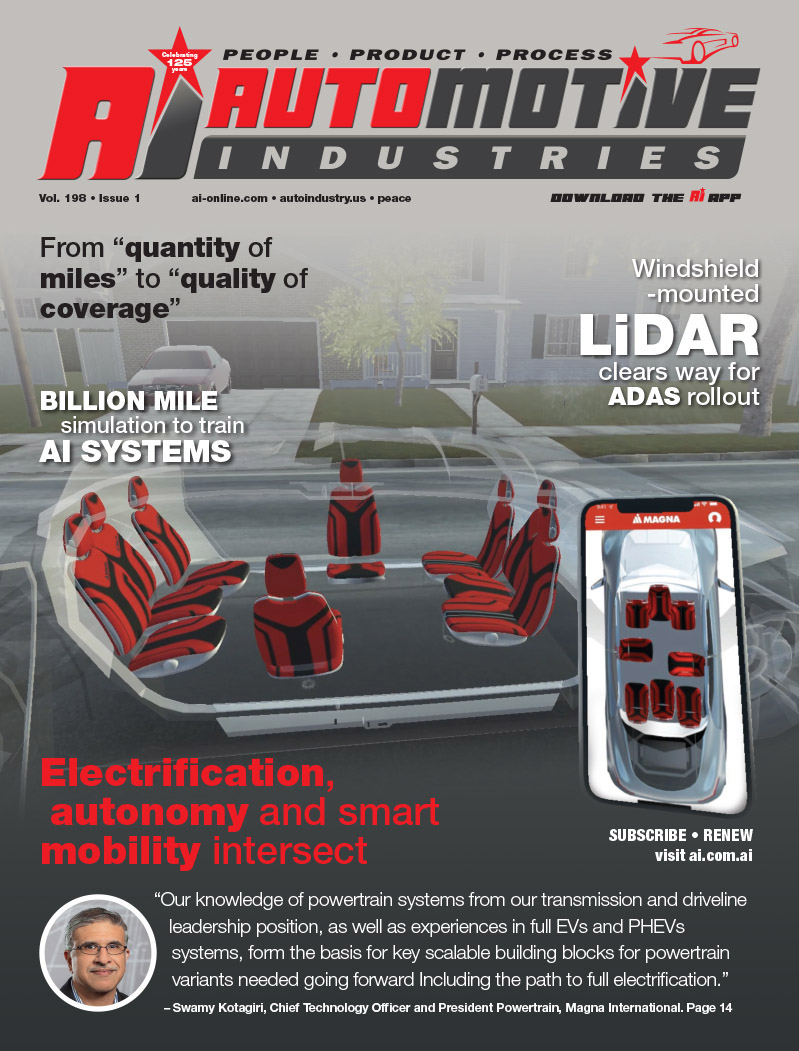
With the Carrera GT, Porsche AG is not only producing one of the world’s most exotic production supercars, but is also setting new benchmarks for the use of advanced materials.Virtually every component of the GT is designed with a single purpose in mind; to create a road car with performance, dynamic, material and structural qualities only matched by the most exotic of today’s race cars.
The high technology deluge starts with the fact that the GT is the world’s first production car to feature a monocoque chassis and engine/transmission mounts made of carbon fiber-reinforced plastic, a design principle Porsche plans to patent. As well as exceptional structural rigidity, the extensive use of carbon fiber keeps the weight of the 181.5 inch-long GT down to 3,043 lb. This compares well with the car’s only real competitor, Ferrari’s Enzo. Though the Italian supercar is actually 44 lbs lighter than the Porsche, the Ferrari should have a weight advantage because its roof is fixed, whereas the German contender has removable targa panels.
The powerplant of the mid-engined Carrera GT is based on a 5.5L naturally aspirated, 68-deg, V- 10 race motor that Porsche originally developed for competition in the 24 Hours of Le Mans endurance race. Bumped out to 5.7 liters, the production version develops 604 hp at 8,000 rpm and 435 lbs.-ft. of torque at 5,750 rpm. A 6-speed manual transmission routes power to the rear wheels. GT program manager, Michael Holscher, says that a paddle shift transmission like that in the Enzo was considered but rejected because it was not fast enough acting. Porsche claims a 0-60 mph time of 3.9 seconds and a top speed of 205 mph.
Close attention to downforce and underbody aerodynamics helped the Carrera GT achieve such a high maximum velocity, with a fully clad carbon underfloor providing ground effects together with the rear diffuser and air flow ducts.
![]() | ![]() | ![]() |
The lower powertrain support is loaded into the autoclave for the eight hour baking process. | The stainless-steel lower control arm for the rear suspension is being TIG welded. | Unmachined brake discs are being loaded into the furnace for carburizing. |
For the first time on a production car, the 19-inch front and 20-inch rear wheels are made through a magnesium forging process. As such, the GT wheels are more than 25 percent lighter than cast aluminum wheels. Race car style suspension includes spring/damper assemblies connected to the inside of the chassis and operated by stainless-steel pushrods and pivot levers.
Porsche is already known for its use of ceramic composite brakes, but the GT goes a step further with the world’s first production car use of ceramics in the clutch assembly.
Holscher explains: “By combining a newly developed ceramic material with specially matched friction facings, we were not only able to retain the relatively simple, well tested twin dry plate clutch design, but also develop a component with a performance potential that is by no means exhausted in this application.” The double-plate dry clutch disc is just 6.7- inches in diameter and plays a key role in enabling the engine and gearbox to be located very low in the car. Along with a dry sump, this lowers the overall center of gravity, which enhances the car’s handling characteristics.
![]() | ![]() ![]() | ![]() ![]() |
Short fiber resin is packed into a brake disc mold. | A ceramic clutch disc (top) is cut with a water jet at 3,000 bar pressure. Plasmatron welding of the deep-drawn aluminum tank. | Porsche engineers (top) view a Carrera GT FE (finite element) model on the 3D screen. A blank is laying next to the fininshed part (bottom). |
Inside the GT, the emphasis on weight saving is borne out in the design of the seats, which are constructed of magnesium, composite carbon and kevlar fibers, another production car first. Trimmed in leather, these seats weigh 23.6 lbs., about half that of a conventional seat.
Porsche’s use of carbon fiber in the body and chassis of the GT extends to the doors, covers and fenders, as well as the underfloor and parts of the interior. This consistent use of carbon fiber combines very low weight with a high standard of dimensional accuracy and body stiffness. As a result, the GT boasts a chassis weighing just over 220 lbs. Most components are up to 40 percent lighter than comparable conventional parts.
![]() | ![]() | ![]() |
The carbon fiber tub uses H400 stainless-steel deformation elements front and rear. | The full carbon fiber underfloor is part of the ground effects package. | The push-rod front suspension is mounted to the monocoque bodyshell. |
Produced at the same small Italian company that supplies Ferrari’s Enzo, the carbon fiber components in the GT go through an elaborate and time-consuming production process. Each part takes about one week in production and requires up to 400 individual operations. At the beginning of production, carbon fiber tissue units impregnated in artificial resin are placed into production moulds. The specific type of resin and fiber used, as well as the flow of fiber and the thickness of the threads in the fiber mats, depend on the subsequent function of the component involved in the car. An additional layer of aluminum or plastic honeycomb material up to one inch thick, depending on the demands made of the component involved, is stuck on to the mats with the help of an adhesive film, further layers of impregnated carbon fiber tissue being laminated on afterwards. Aluminum inserts are then laminated on additionally at specific points in order to subsequently fasten additional components to the load-bearing structure. Finally, the mould is sealed airtight by means of a cover foil and placed in an autoclave high-pressure furnace at 6-8 bar and at temperatures of 300 degrees F. In the process, the resin systems form a polymer and, via the adhesive films, bond the honeycomb or plastic on to the carbon fiber. This baking process may take up to eight hours.
![]() |
The Carrera’s seats are constructed of magnesium, composite carbon and Kevlar fibers and covered in leather. |
![]() |
The 5.7L, 604 hp V-10 is based on the 5.5L V-10 LeMans racing powerplant. |
In terms of torsional stiffness, the Carrera GT sets a new standard for open-topped cars. Attention to passive safety involves use of steel reinforcing tubes in the A pillars. Inside the passenger compartment, all surfaces relevant to safety, such as the dashboard, seats and door trim, are topped with Kevlar synthetic fiber to avoid the formation of splinters.
Front and rear crash protection is provided by arms, made of high strength austenitic stainless steel (H400), which project from the carbon fibre chassis. These arms have special deformation profiles for efficient absorption of impact energy. Aluminum inserts connect the arms to the chassis at the front and the engine/transmission support frame at the rear. The bumper system is made up of an extra-strong aluminum crossbar and impact tubes.
Production of the Carrera GT is under way alongside the Cayenne SUV at Porsche factory in Leipzig. At the rate of two per day, Porsche will build a total of 1,500 GTs over three years. Already 1,000 of the GTs, priced at €500,000 have been pre-sold and Porsche expects at least half of the total production to end up in the U.S.

More Stories
Best Wheel Size for Off-Road Adventures: What People Get Wrong
Trusted Auto Collision Repair That Restores Both Performance and Peace of Mind
What You Need to Know About Tire Pressure in Winter vs Summer