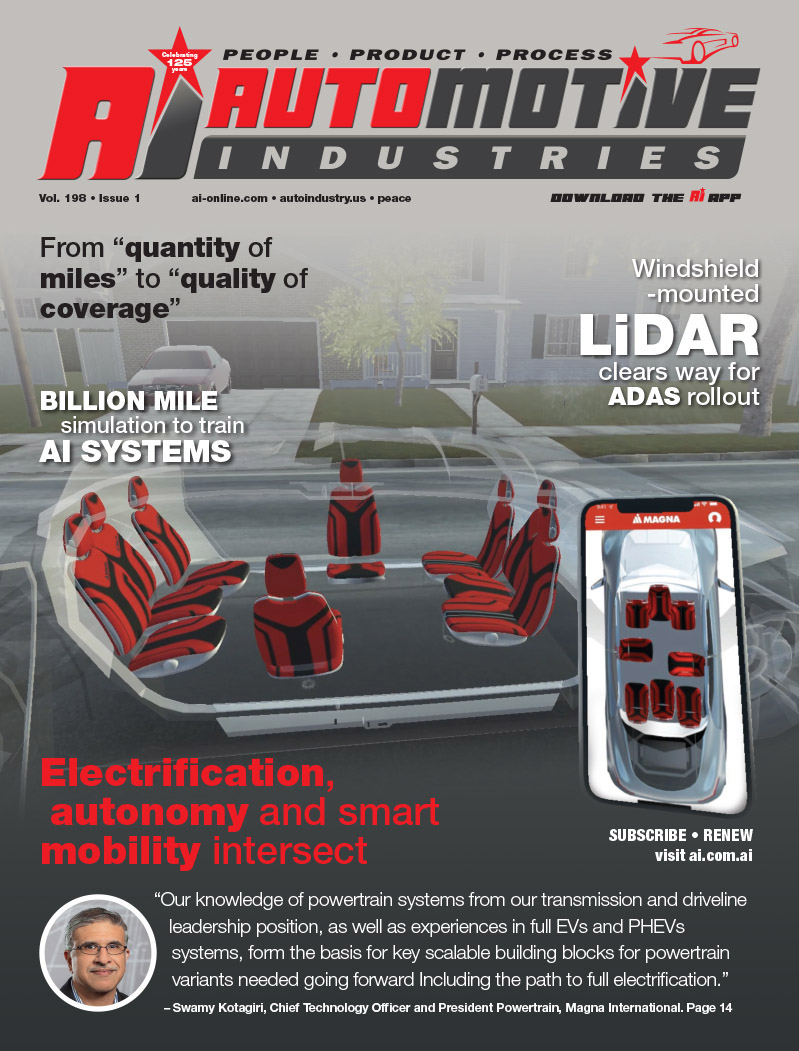
Mahle presents variable valve timing system, all-plastic oil filter.
![]() |
Mahle’s variable valve timing product aims to be a simple, robust, low friction design capable of functioning reliably over the life of the engine. |
Recently, German engine component specialist Mahle GmbH presented its contending technology. In contrast to the hydraulic or hydromechanical valve timing adjusters on the market, including the improved two-stage valve stroke adjustment systems or the continuous adjustment system used by a number of up-market car builders, Mahle reports that it has aimed for mechanical systems that offer low production costs while matching the performance of competitive systems.
To this end the company is working simultaneously on several approaches, ranging from two-point stroke adjustment and continuous stroke adjustment to continuous variation of stroke and valve opening time. Functional testing of these systems has already been carried out and the first test in a complete engine took place in 2003, according to Mahle.
In addition to the adjusting function per se, Mahle reports that its product objectives also address aspects like simple, robust design, low frictional losses, reliable functioning over the entire service life of the engine and applicability in existing cylinder head designs. The system should also be suited to use on both diesel and gasoline engines on either the inlet or exhaust side, or both.
Following successful functional testing, one of Mahle’s new VVT systems is to be tested in cooperation with a leading engine manufacturer. At the time of this writing, market launch and series production would be possible in two to three years, the company states.
![]() |
The Mahle all-plastic oil filter is part of a multifunctional module comprising the oil cooler, the oil feed to the turbocharger, major components of the crankcase ventilation system, a pressure control valve and temperature sensors for lube oil and cooling water. |
For example, the new filter is instrumental in a doubling of oil change intervals to 18,600 miles, and its materials are chosen to withstand temperatures of up to 302 degrees F and pressures up to 290 psi. In the applications cited, the all-plastic filter forms part of a multifunctional oil module that also contains the oil cooler, the oil feed for the turbocharger, major components of the crankcase ventilation system including a three-cyclone oil mist separator, a pressure control valve and several temperature sensors for lube oil and cooling water.
A further major development goal, the company states, was to position the filter to facilitate easy maintenance. On the Audi vee configuration engines, it is located upright between the cylinder banks where it also serves as a crankcase cover and can be readily accessed from above. An emptying system prevents oil fouling during maintenance work, Mahle states.
More Stories
Your Guide to Filing a Car Accident Claim
Steps to Take Immediately After a Car Accident
What Makes SUV Cars More Prone to Accidents?