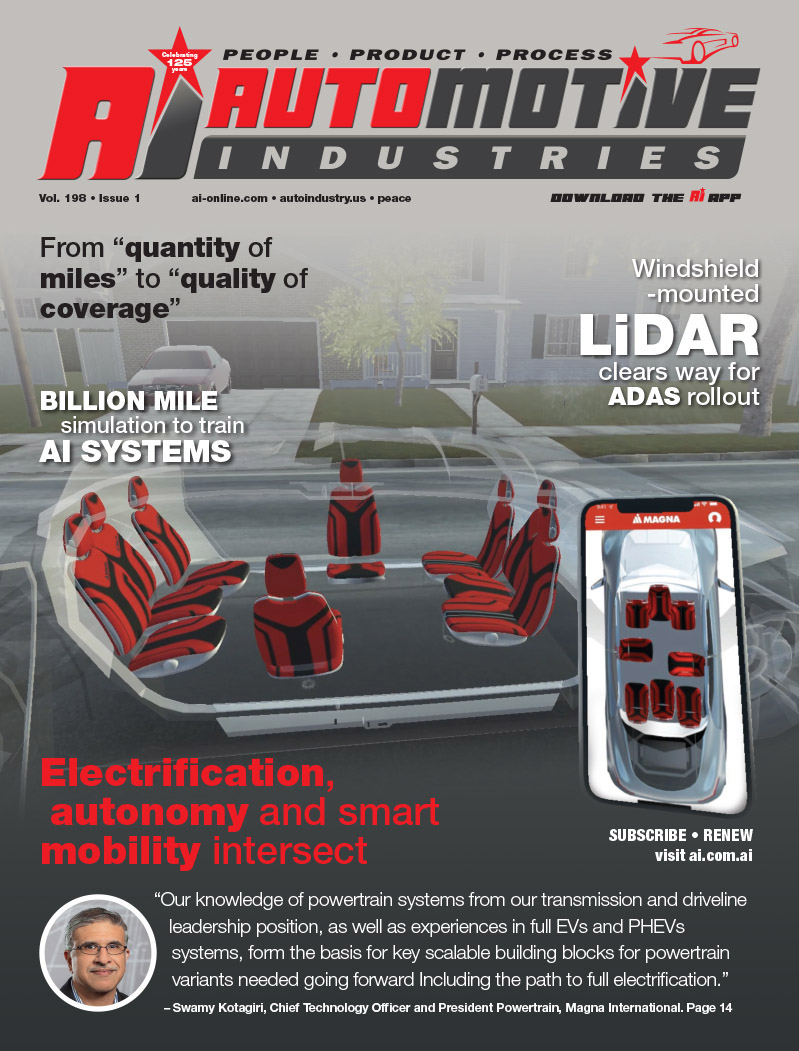
GM explores stationary power applications for automotive fuel cell development.
The road to the commercialization of fuel cell vehicles has taken an interesting turn.
On Tuesday, February 10, 2004, Secretary of Energy Spencer Abraham and Texas Governor Rick Perry threw the switch on the first of some 400 to 500 General Motor’s PEM automotive fuel cell power modules that will serve as stationary power plants, making electricity for Dow Chemical’s Freeport, Texas, manufacturing facility.
![]() |
The first trailer (above) parked on the site of Dow Chemical’s Freeport, Texas, power generation facility houses one fuel cell power unit (below) which will be used to test the purity of the hydrogen produced by the Dow plant. |
![]() |
The trailer is parked in the facilities power station that currently uses cogeneration to produce all of the steam and electricity for Dow’s largest facility with 75 production plants covering some 30-sq.mi.
You might ask yourself what would bring the world’s largest auto manufacturer and the world’s largest chemical producer together to advance fuel cell technology. The answer to that question is a commercially viable agreement that was made in hydrogen heaven.
Hydrogen is a byproduct of several of Dow’s manufacturing operations and up until now, the ‘fuel’ in fuel cell was piped to the power station and used to heat boilers for making steam, sold off to companies like Air Products for resale to industry or vented into the atmosphere. Now some of that hydrogen will be used to run the GM fuel cells.
“We started talking to Dow in late 2002,” says Timothy E. Vail, director fuel cell commercialization, GM fuel cell activity, “and it’s kind of an interesting mix. Dow needed to get more value from its hydrogen strength and we needed a place to put our technology.” Vail says that GM weighed the pros and cons and found that Dow was a good fit.
“From our standpoint the Dow transaction is a positive economic transaction for us … pure profit,” Vail says. “If you take the cost of the unit and the money we’re getting from Dow, (the profit) is marginal. But if you think of all the cost we avoid, building vehicles, running on test stands, scrapping equipment, it’s a hugely profitable deal for us. It’s the same for Dow. If you take its electricity and gas costs, plus the emissions benefits, what they’re doing with this byproduct fuel becomes an economic transaction for them as well.”
While the first unit is a test unit, Vail says that once the industrial-strength hardware is installed this summer, it’s really past the test stage. “This agreement is a true commercial arrangement,” Vail says. “We’re moving forward to install megawatts of power and you don’t do that on a test basis, you’re doing that for economic reasons.”
Vail says that the Dow venture will help to advance GM’s fuel cell program in a couple of areas. Dow has been dealing with hydrogen for decades and has shared that expertise with GM, which Vail says, has advanced the fuel cell program immeasurably.
And for a fraction of the cost of building 400 to 500 fuel cell-powered vehicles, GM can run the same number of units in a real-world environment which, in turn, will build the supply base and develop expertise in manufacturing and production engineering, ultimately bringing costs down to the commercialization goal of $50 a kilowatt by 2010.
“It’s just incredibly expensive to build and maintain a fuel cell automobile,” Vail says. “If you want it for PR purposes, that’s great, but if you really want to deliver in 2010, you cannot be relying on vehicles for your early volume, you’ll go broke. You’ll spend all of your money on your vehicles and not your R&D program.” Dow has its own reasons for finding alternative energy sources.
Dow uses natural gas to manufacture all of the electricity needed to produce heat and power for the Texas facility and is tied to a highly controlled natural gas market. Tommy Block, vice president of Dow’s operations in Texas says that the site’s natural gas bill in 2003 was $1 million dollars a day higher than the 2001 bill.
“We have to find ways to cut a million dollars in cost every day just to stay even with where we were in 2001,” says Block.
Since hydrogen is a byproduct of Dow’s manufacturing operations, that fuel is virtually free and that makes fuel cells look real good from an economical standpoint.
Dow also finds the technology’s lack of emissions an asset worth investing in. The company is situated in an area known as the Huston Galveston corridor, a very heavy industrial area populated by 10 other large industrial facilities, all creating enough NOx to earn Huston the dubious honor of being ranked as having the dirtiest air in America by the Environmental Protection Agency. As a result, the State of Texas has instituted some very aggressive NOxreduction initiatives, so Dow and its partners in the corridor are all interested in finding ways to reduce NOx.
“We’ve actually been contacted by just about everybody,” Vail says. “For us it’s much more of a supply constraint than a market constraint. If we had more modules in production we could sell to everybody in the Gulf coast.”
While Vail says that GM is still 100 percent focused on delivering the fuel cell automobile to the marketplace by 2010, he won’t rule out the Dow exercise as possibly leading to other industrial applications. Using automotive power for industrial applications is hardly a new venture for GM. The company’s internal combustion engines can be found powering lift trucks, industrial wood chippers and stationary irrigation pumps among other things.
Vail says that there’s a raging debate in the industry on whether a PEM automotive fuel cell is right for stationary applications. While other fuel cell technologies, like solid oxide and molten carbonate have the theoretical ability to run for long periods of time as well as achieve higher efficiency numbers, the companies developing these fuel cells are heavily dependent on government financing for R&D and at the mercy of an industry that won’t consider fuel cells until they can deliver 45 percent efficiency at $200 a kilowatt. “Without that big automotive volume pull,” Vail says, “it’s going to be a real challenge to get that technology to be robust enough and cost effective enough.”
Vail says that because PEM fuel cells will be plentiful, durable and very cost effective, they will be filling niche applications where long run times aren’t as important.
“Once you get to the automotive cost points or even two or three times, $150 a kilowatt, you are cheaper on a capital cost basis than any technology, even diesel,” Vail says. “Couple that with very high efficiency (45 to 48 percent) and no emissions and noise and you’re going to see that there’s going to be a whole host of new opportunities for these things.” The PEM cell’s performance characteristics make it ideal for backup systems in what Vail refers to as the premium power market.
“Our fuel cells can ramp very, very quickly,” Vail says, “they can go to full output in less than 30 milliseconds.”
While that’s not quite as fast as the eight to 10 ms start-up times of most premium power applications, it’s still faster than the five or 10 minutes needed for a diesel startup. Vail could also see a PEM module replacing the battery pack in a diesel generator, turning it into a one-of-a-kind compact uninterruptible power supply.
And cost is less of a factor in the premium market where $1,000 a kilowatt is a competitive price.
Vail says that as GM ramps up to an automotive production run of 25,000 or more and capacity is no longer a constraint, then you’ll see General Motors actively pursue stationary industrial opportunities.
“That market’s very attractive to us,” says Vail, “and we’ll be working in that market and making some announcements perhaps as early as this year.”
Vail believes that if PEM technology takes hold like the automakers think it will, it will become as cheap as today’s internal combustion engines but at an efficiency level that competes with combined-cycle turbine technology with the added benefit of zero emissions.
“I think it will fundamentally change the way power is delivered in the U.S. as well as developing countries,” Vail says. “If you have a distributed energy source that is on par with, or within at least 15 percentage points of what existing combined-cycle plant technology is, that will fundamentally change the way networks are designed and built.” The question then, becomes when and those numbers range anywhere from five to 25 years. Whatever the time frame Vail believes that stationary applications will rapidly outpace automotive applications in the early days.
“The commercial buyer will buy based on economic rationale where a retail consumer will be less interested in adopting new technology,” Vail says.
More Stories
Your Guide to Filing a Car Accident Claim
Steps to Take Immediately After a Car Accident
What Makes SUV Cars More Prone to Accidents?