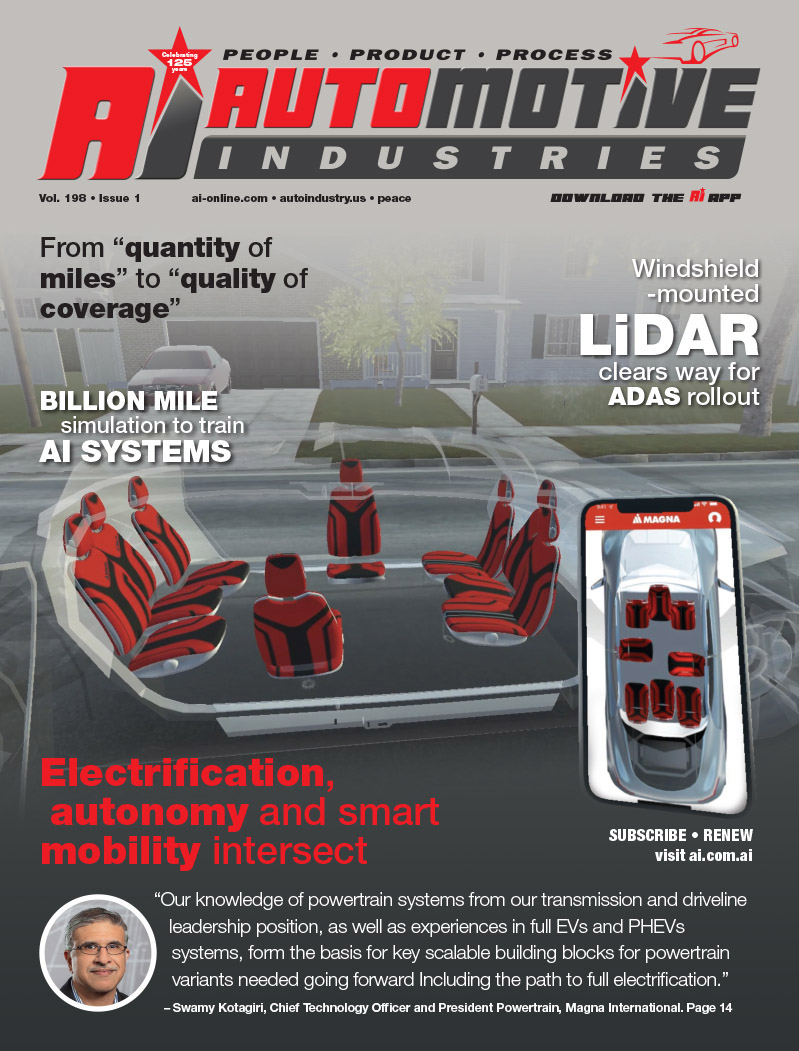
Smart Lesson In Quality
Carbuilders and suppliers strive together in Smartville Nation.
![]() |
Three of Smartville’s 2,200 employees assemble one of four different Smart models built at the French plant. |
As they eat, workers from the automaker and suppliers alike can chew over how much bonus they will lose if the re-work station is too full.
It’s a concept, along with many, many more which could soon be finding its way across the North Atlantic. Plant managers from across DaimlerChrysler in general and Jeep in particular, are regular visitors to Smartville — so called because the plant comprises 14 buildings and is shared with six systems suppliers: Magna Chassis & Uniport, Surtemal/Eisenmann, Siemens VDO, Dynamit Nobel, Cubic Europe and Thyssen Krupp.
The production concepts in Hambach, in the Lorraine region of France, just two hours drive from DaimlerChrysler HQ in Stuttgart, Germany, will also be making their way across the South Atlantic.
A new Smart SUV, to be called the “formore,” and due for launch in the United States in 2006, is to be built at the DCX plant at Juiz de Fora, in Brazil.
This factory currently produces the Mercedes-Benz A-class but will become the center of worldwide production for the SUV. According to Helmut Wawra, Smart’s head of design and engineering, most suppliers for the project will be European.
“Because of the size of our engineering department, it is important suppliers have the ability to carry out engineering work close to us in Germany and have plants in Brazil, this is the case certainly for the Tier 1 suppliers.”
The United States will be the main market for the Smart SUV taking 50 percent of production. Wawra says: “It will obviously be a very important car for our brand because it will be the first Smart car in that market. With the federal regulations involved, we will not be introducing any other Smart products there until the next generation City Smart (now called fortwo).”
Between now and launch at the Detroit Auto Show in 2006 there are a lot of tests to be passed to meet ES Federal regulations. “Emissions tests are particularly time consuming and it is a challenge to squeeze it all in to the time schedule,” added Wawra.
He said that Smart would not have its own retail chain in North America but will almost certainly use the Mercedes-Benz network. “Our colleagues at Mercedes-Benz have a lot of experience in the North American market from things such as Federal regulations to the special expectations of the consumers in the United States.
“When we introduce the SUV, it will be a small car with some special design features but it will be instantly recognizable as a Smart and that is what we are working on right now.” This will include the Smart DNA: Two tone color, the combination of steel and plastic, interior textiles use and the unique shape and features of the instrument panels.
Wawra added: “We have to look at all the expectations consumers have for an SUV and apply them to our brand. At the moment people in the United States have no expectation of what Smart is.”
In January this year Smart started production of its first four-seater, the forfour, in Born, the Netherlands, a plant shared with Mitsubishi.
Back in Smartville, things have moved on since the plant opened in 1998 producing just one model with 250 part numbers and a choice of four colors for the plastic body panels.
Now with the Smart fortwo and cabrio plus the Roadster and Coupe, there are 2,000 part numbers and much more complexity in the number of specifications.
“We have grown up very quickly,” says Plant Manager Klaus Fischinger. “We have now gotten used to working with our supplier partners and have refined and optimized the manufacturing process.”
It has not always been easy. The idea of sharing the assembly responsibility with supplier partners was revolutionary and has been ultimately successful, but Fischinger said there were doubts in the beginning.
“Each company has its own philosophy and each was worried as to how that would correspond. We meet every month to discuss how we have been doing and how we plan to work in the following month.
Smartville employs around 2,200 people. Hambach was chosen because DaimlerChrysler wanted the plant located in the middle of Western Europe. The plant is 6.2 mi. from the German border and it is an area that has changed nationalities several times through history. While 95 percent of the staff are French, most speak German.
Total investment in the plant stands at more than $650 million, including all systems suppliers. Wages in Smartville are the same whether you work for Smart or one of its partners, only the benefits may be different.
Body panels are produced by Dynamit Nobel where General Manager Hartmut Hensel boasts that there is virtually no waste. Plastic is recycled and used on black parts which are not seen on the car while even the paint changes are used to create some of the weird and wonderful dual colours for some of Smart’s unique body panels — this negates the need to completely clean out the paint tanks at the end of each color run.
Between 10 and 12 percent of all panels made are for the aftermarket or replacement — not necessarily because they are damaged, but so that people can change the color of their car. A complete set of panels costs around $600 and can be changed within 35 minutes — all you need is a screwdriver.
Another innovation is that nothing actually belongs to Smart until the car is signed off the line. It is when the bar code is scanned that suppliers are paid.
Theoretically the factory owns the car for just a few minutes before responsibility is handed to Mosolf the distribution logistics provider. In fact the plant usually hangs onto the vehicles for a day to give it a re-work buffer.
One part of Smartville’s quirks will definitely not make it to the United States: There is no air conditioning at the plant because it’s bad for the environment.
Although a special airflow system helps keep things bearable in mid-summer, last year’s heatwave in France did mean the glass lifts which run up the outside of the building had to be sealed off.
If anyone had got stuck in one they would literally have become a French Fry.
![]() |
The Slingshot concept that debuted at the 2004 North American International Auto Show is based on the Smart roadster platform. |
Slingshot Salvo The United States has already had a glimpse of what Smart can do. The Chrysler Slingshot concept on stand at the Detroit auto show in January is based on the Smart Roadster platform — but it will not make it to market. Smart Design and Engineering Chief Helmut Wawra said: “The Slingshot was a very exciting concept, but it does not meet Federal requirements. What it does is show how Smart can fit into the DaimlerChrysler group in terms of research and new model development across all the brands. “Slingshot is a great idea, a sports car with the fuel consumption of our City Coupe. The idea was to show the United States government what is possible in terms of reducing fuel consumption without having to invest in expensive hybrids.” Does Wawra think diesel can make it in the United States? “There has to be a change in perception,” he says.” The diesel engine is still perceived as dirty, smelly, noisy and slow. They are big barriers to overcome. But sales of Mercedes-Benz and Volkswagen diesels are growing in North America and we expect the passenger car market to grow slowly. “The advantage of a diesel over hybrids is that it is a known quantity. There is still a lot of development work to be done on hybrids and the technology is changing and evolving all the time. Diesel has a proven track record and is reliable.” |
This article was provided exclusively to Automotive Industries by Interchange, a U.K.-based automotive business agency and consultancy servicing media and corporate clients. Anthony Lewis is a partner in Interchange and can be contacted via e-mail at ajlewis@compuserve.com.
More Stories
What You Need to Know About Tire Pressure in Winter vs Summer
Essential Features to Look for in ADAS Calibration Systems
Your Guide to Filing a Car Accident Claim