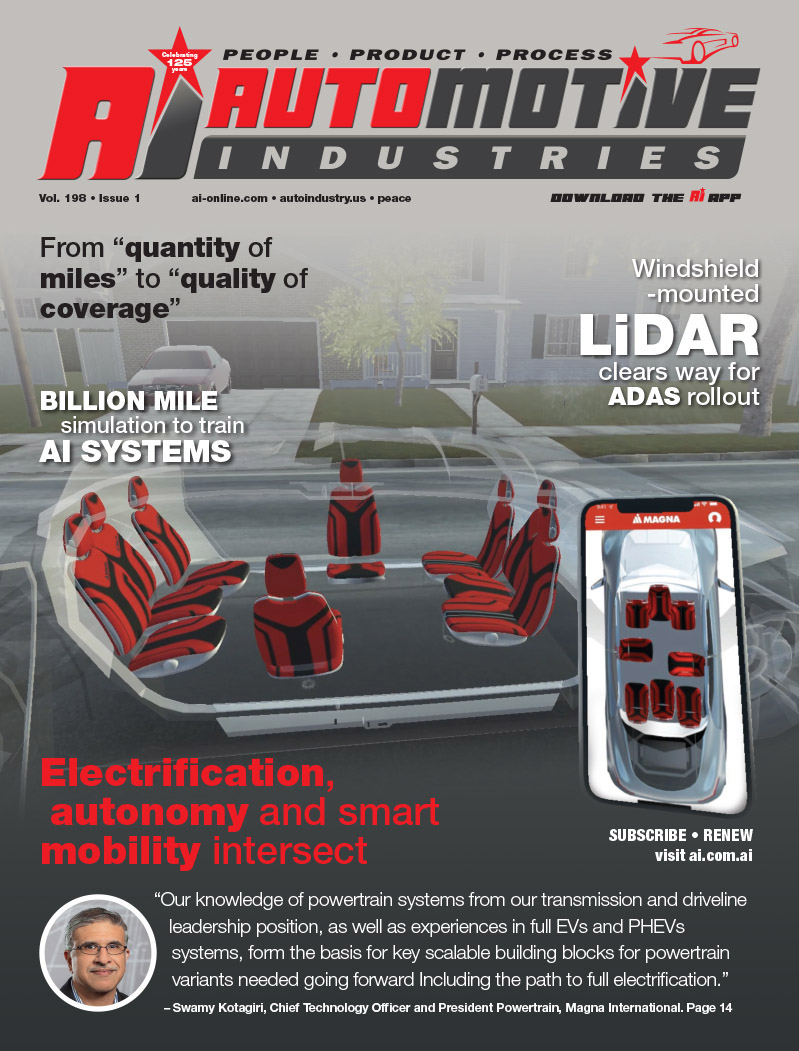
Molecular science develops a stronger, lighter weight composite that’s finding its way into many areas of the automobile.
![]() |
Nanocomposites are being used for the side molding on the 2004 Chevrolet Impala, General Motor’s highest volume car. |
Nanocomposites are made on the same length or order of magnitude scale as the molecule (1 millionth) rather than using micron (1 thousandth) sized fillers, as is the case with normal composites.
Clay was chosen as a filler, in this case, due to the inherent layering in the material. It exists in nature as a series of layers separated by ions. This clay must be manipulated on that same scale.
The example made by Will Rodgers, a staff research scientist for GM about this manipulation of the clay was: “Think of a notepad. The sheets of paper in a notepad, just stacked up… With the right processing conditions and the right chemistries it is possible to peel those sheets off one by one so that now they exist as individual sheets rather than a conglomerate of clay.
“Once you think of it on that level… a normal micron-sized filler has an aspect ratio of about 5 (length to thickness) these nanocomposites could have aspect ratios of nearly 75 to 100 (length to thickness) or even 200 to 500. That change in aspect ratio is what allows for modulus improvements, the strength improvements. These are both directly related to the aspect ratio of the ‘sheet.’”
To give a clearer idea of the size/scale of the nanocomposite filler materials, 100,000 of the aforementioned theoretical sheets stacked on top of each other would roughly equal one human hair’s width.
GM partnered with Basell and Southern Clay Products to move its Nanocomposite program forward. Basell is a producer of polypropylene resins for plastics and Southern Clay Products specializes in clay specific to use in Nano-tech applications. GM decided to work with Southern Clay to ensure that the manipulation of the clay on the molecular level was worthwhile.
If manipulated improperly you have nothing but a low filler content conventional material with none of the advantages that can be garnered from a nanocomposite, namely better rigidity from less material on the whole and the accompanying weight savings.
Nanocomposites made by GM are made from the same type of extruders that are used to make conventional composites and according to GM, they actually can be run off the same line.
The extruders needed to be fine tuned to make running Nano/conventional composites, a process that was facilitated by the companies that GM partnered with, Basell and Southern Clay Products. The materials do have a large processing window. There are several conditions that will allow for more production flexibility as far as manufacturing logistics.
The first commercial use of the thermoplastic olefin nanocomposite materials from GM was the step assist on the 2002 Chevrolet Astro and GMC Safari vans. The next initiative within GM for nanocomposites was the side molding pieces on the 2004 Chevrolet Impala, GM’s highest volume car. GM estimates use of over 500,000 lb. of nanocomposite material a year.
In the case of the nanocomposites used in the Impala side moldings, GM reports a weight savings of seven percent as well as a better overall surface quality because the filler is so small it doesn’t hinder the surface of the part. The small fillers are also said to improve marring resistance. Usually when a stone hits a rocker panel, the white that appears is the eye being able to see the filler. In the case of the nanocomposites this effect should be lessened due to the inherently smaller filler size.
Right now GM is mainly looking at exterior trim applications for this technology. Side moldings, fascias and rockers are par for the course at the moment but the next obvious place to go would be the interior of the car. Dashboards, door inners and pillar covers could all possibly be replaced by nanocomposites.
No parts are used unless they are equal to, or cheaper than, what is currently available to GM, according to the company. And it is based on that credo that nanocomposites are being used by GM. Further, as with any new technology being applied to the automotive industry, the economics make more and more sense as the marketable uses for a product grow. That is the space currently occupied by materials engineered on a molecular level.
More Stories
Best Wheel Size for Off-Road Adventures: What People Get Wrong
Trusted Auto Collision Repair That Restores Both Performance and Peace of Mind
What You Need to Know About Tire Pressure in Winter vs Summer