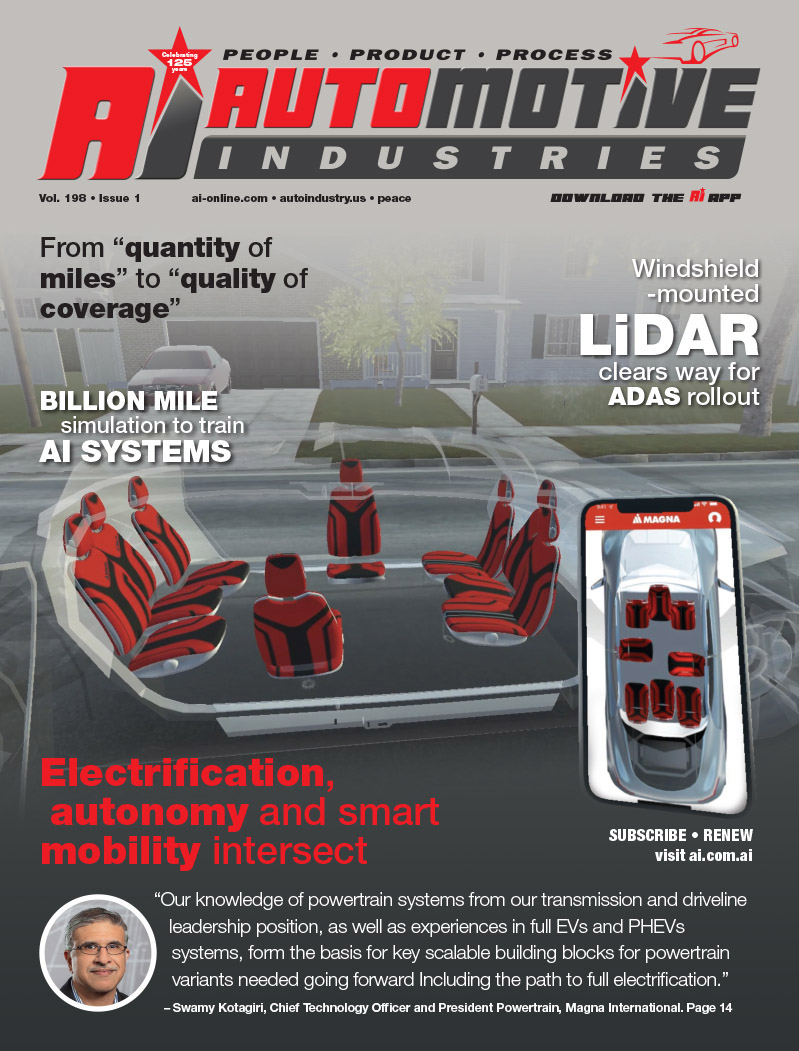
Advanced flexible machine tools virtually eliminate changeover times.
General Motors recently rolled out a trio of new manufacturing technologies to help stay on top in its never-ending pursuit of quality.
![]() |
Phil Bojda, senior research engineer with GM R&D, prepares to load the Agile Machining Fixture into a CNC cutting machine. The Agile fixtures not only add to greater flexibility but can cut tool changeover from several days to several minutes. |
Typically, GM’s machining operations have been designed to process one specific product because the clamps and fixtures that hold the parts cannot facilitate more than one application. But the past is gone.
The new technology is aimed at powertrain components for the time being. Cylinder heads have already been run off an R&D mockup of the system and there is talk of using it for transmission cases as well. GM is forecasting a low-volume application in a powertrain plant for the first quarter of 2005.
The Agile Machine Tool is a combination of a CNC cutting tool, the Makino A99, which houses a large upright “tombstone” that is magnified. The fixture elements are then attached to the tombstone at “low” magnetic setting to hold them in place. Once all the fixture elements are in place the setting is then bumped up to the ‘high’ setting, for machining. This differentiation in magnetic levels was something that GM had to work closely with the supplier on, since it was fundamental to how the system was to operate.
The magnetic field on either setting never extends out more than one inch from the surface of the “tombstone” fixture, eliminating any threat to workers and not attracting any kind of debris.
“The fixture elements on the Agile Machining tool are clamps, supports and locators. Locators are the key to the whole operation because they are the reference points that the fixture is built on,” explains Pulak Bandyopadhyay, lab group manager, Manufacturing Systems Research for GM R&D.
While the flexibility of this new system would seemingly be the biggest upside, there is also the matter of the changeover times. While run-of-the-mill changeovers on such a tooling operation would be anywhere from hours to months depending on circumstances, the predicted changeover times for the Agile Machine Tool are in the neighborhood of five to ten minutes.
GM is also bringing some other technology into its manufacturing processes to help ensure quality. One of these new systems GM calls the Video Variance Monitor (VVM).
VVM, a computer-based vision system, is already online in 22 body assembly plants in the U.S., Canada and Mexico.
VVM uses a digital video camera to capture cycles and transfers the digital video to a computer. GM-developed software allows the dimensional engineers and toolmakers to visualize the entire sequence frame by frame. Once at that point, root causes can be more easily located and fixed.
Accompanying the VVM is the Variation Reduction Adviser. The VR Adviser is a webbased software tool aimed at helping employees resolve quality issues. This system is online, currently, in 11 GM body shops throughout North America.
Not unlike an internet message board, the VR Adviser allows employees to log in and communicate with fellow GM workers in an effort to share problem-solving data on various parts and operations. Under a topic, there’s room provided for comments from the employee experiencing the problem as well as space for responses from their compatriots at the other 11 plants. The system is also set up to allow for attached pictures and video files to help further illustrate what the problem is, or how to fix it. GM estimates that the VR Adviser program could save them up to $15 million a year.
More Stories
Best Wheel Size for Off-Road Adventures: What People Get Wrong
Trusted Auto Collision Repair That Restores Both Performance and Peace of Mind
What You Need to Know About Tire Pressure in Winter vs Summer