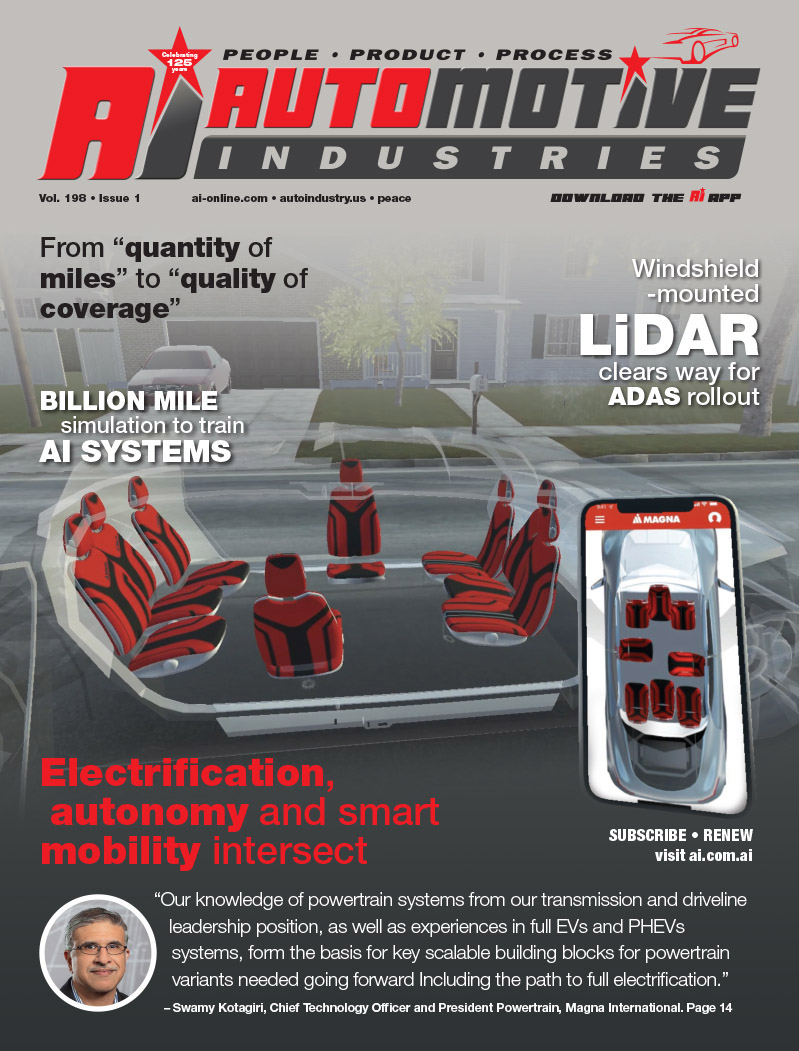
“Squirt” has been defined as the effect produced by dropping an anvil on an open tube of toothpaste. The V-10 TDI-powered Touareg has squirt, plenty of it thanks to the best-in-class torque of 750 Nm (553 ft. lbs.) at 2,000 rpm. Power output is 230 kW (310 hp) at 3,750 rpm. There is no fuel economy vs. performance issue here. With the standard 100 L (26.3 gal.) fuel tank, the 5.0L V-10 TDI powered Touareg will give owners a 600-mile highway cruising range at 23 mpg. And there will be people who buy it for the fuel economy, which is attractive, but most will drive it for the nimbleness of its performance. The only thing that doesn’t move on this SUV package is the fuel gauge.
AI asked Stephan Krebsfanger, product development manager, Volkswagen of North America, what he felt was most important about the engine. “To us it’s the combination of sheer power and luxurious, low NVH driving characteristics. This engine is being shared between the Phaeton and the Touareg in Germany and the Touareg in Germany, the U.S. and the rest of the world.
“It’s an engine that has to basically please two worlds. The world of luxury, the very epitome of luxury as is expected in a sedan like the Phaeton and to have the sheer torque and brute power that you need in the world of the SUV. Bringing those two worlds together is what has been accomplished with this engine.” With a top speed of 130 mph, the V-10 accelerates the 5,825-pound Touareg from 0- 60 mph in 7.5 seconds. Touareg towing capacity is given at 7,716 pounds.It’s all about the engine, this very novel V-10 which is comprised essentially of two inline 5- cylinder engines, Siamese twins, each with its own air intake, exhaust and turbocharger, are connected only at the crankshaft and through the electronic controls. They do, of course, share a common block and crankcase. The cylinder bank centerlines are offset by 90 degrees.
This cylinder layout results in an extremely compact engine design that contains ten 0.5L cylinders within 544 mm of overall engine length. Bore and stroke of the engine are 81.0 X 95.5 mm. This slightly undersquare design is favored for desired torque characteristics. Cylinder spacing is given at 88 mm.
In keeping with the well-defined symmetry of the cylinder layout, the firing order is such that opposing cylinders of each bank follow one another. Thus, the firing sequence is 1-6-5- 10-2-7-3-8-4-9. Being a four-cycle diesel, five cylinders fire every 360 degrees of crankshaft rotation, or one combustion event for every 72 degrees, providing extremely smooth delivery of power to the Touareg’s Tiptronic equipped six-speed automatic from ZF.
Containing the violent combustion forces of a diesel is always a challenge and VW has met that challenge with unique engine architecture. The block and heads are of lightweight hypereutectic aluminum alloy.
The bottom side of the block carries the top member of a cast iron bearing tunnel. An underslung aluminum alloy crankcase carries the bottom half of the bearing tunnel. The bearing tunnel, of course, contains the crankshaft and has six main bearings.
![]() |
Volkswagen’s 5.0L V-10 turbodiesel cranks out a whopping 553 lb.ft. of torque at 2,000 rpm giving Touareg work-truck towing ability. |
There are two schools of thought with respect to linered- vs. parent-bored cylinders for diesel engines. While some still regard linered cylinders to be more durable and rebuildable, others regard them as a Band-Aide on manufacturing processes. If you can hold manufacturing tolerances tightly enough, parent bored is simpler, requires fewer components, facilitates tighter packaging and more effective cooling.
Riding in these parent-bored cylinders, aluminum pistons have a sombreroshaped entrant bowl and cast-in cooling channel, which is jet cooled with the piston at bottom dead center.
Strengthened with brass bearings, piston pin bosses and connecting rods, small ends have a trapezoidal shape and thus more bearing surface area to absorb combustion forces, a premium engine feature. Connecting rods are fabricated from sintered metal and feature an angled split on the big end. Another interesting feature is an offset pin bore. This causes the piston to shift to the opposite cylinder wall just before top dead center greatly reducing piston slap (aka: noise).
![]() |
To prevent tension in the cylinder block, the cylinder heads, cylinderblock and the end bracket are screwed to each other using tie rods. |
With the 90 degree layout and offset crank throws, second-order vibrations are reduced. The crankshaft also has a viscous type torsional vibration damper. Engine oscillation is held to a few thousandths of a millimeter.
A helical gear set drives the camshaft in each cylinder bank and all engine auxiliaries including a duplex oil pump, scavenging pumps, 34 coolant pump, ac compressor, power steering and alternator. The engine fan is electrically driven. No timing chains or belts needed here, just gears and shafts.
Helical gears provide longer gear teeth in less space saving space and weight. They are also a factor in reducing NVH.
The overhead cam in each bank of cylinders drives the intake and exhaust valves as well as the unit injectors. There are two valves per cylinder. Heads are of cross-flow design. Intake ports are on the inside of the V and exhaust ports on the outside of the V.
Orchestrating the control of the engine is the new generation EDC16 electronic engine management system from Bosch. It’s a dual control with a 32-bit microprocessor for each cylinder bank working in a master-slave processing mode. The EDC16 controls all aspects of combustion including the boost from the twin turbochargers.
These are variable geometry turbos that expose more compressor vanes surface at slow speed and gradually less surface as engine speed increases. Turbos are closely coupled to the exhaust ports. Turbo vane position is electrically driven, controlled by the EDC16. This cuts down on turbo lag and provides the right boost over the entire operating range. These turbos are not wastegated.
Known as “Pumpe D?se” in Germany, but unit injectors here, the fuel delivery system from Bosch is capable of injection pressure of 29,700 psi (2050 bar).
According to Dr. Marcus Parche, vice president of diesel system marketing, Bosch GmbH, one attraction of unit injection is that each combustion event is separate from the others, free of standing waves in the fuel lines and other fluid dynamics. Conditions are normalized at each cylinder before each combustion event.
Other advantages? The start and duration of injection can be tuned easily; such stunningly high pressures cannot be achieved by other methods currently; injectors are cam driven but actuated by fast-acting solenoids; injection can be of extremely short duration with pilot injection and a soft ramp up in pressure lowing noise; they are extremely compact combining pump and nozzle together.
![]() |
Pump-jet injectors feature increased injector pressure in the partial load range, where injector pressure is increased by an alternative piston with a larger stroke. The larger stroke and the throttling effect of the inflow hole between the jet spring space and the fuel channel increase the pressure in the jet spring space further increasing injection pressure. |
In a presentation during the recent Touareg North American rollout, Parche couldn’t fathom how Americans can just pass on the superior performance of the modern diesel, the opportunity to get 30 percent more torque from a comparable size diesel vs. gasoline engine, achieve 30 percent fuel savings, and reduce CO2 emissions by 20-25 percent as well.
Salute Volkswagen for providing most U.S. citizens the opportunity to see what modern DI diesels are all about. Though equipped with cooled exhaust gas recirculation and oxidation catalytic converter, the Touareg is a 45 state + Canada SUV, not available in California and several Northeastern states.
Too bad for them. They are missing out on some of the highest level engine technology ever available here or elsewhere. The V-10 TDI-powered Touareg raises the bar, to 2,050 bar in fact.
More Stories
Best Wheel Size for Off-Road Adventures: What People Get Wrong
Trusted Auto Collision Repair That Restores Both Performance and Peace of Mind
What You Need to Know About Tire Pressure in Winter vs Summer