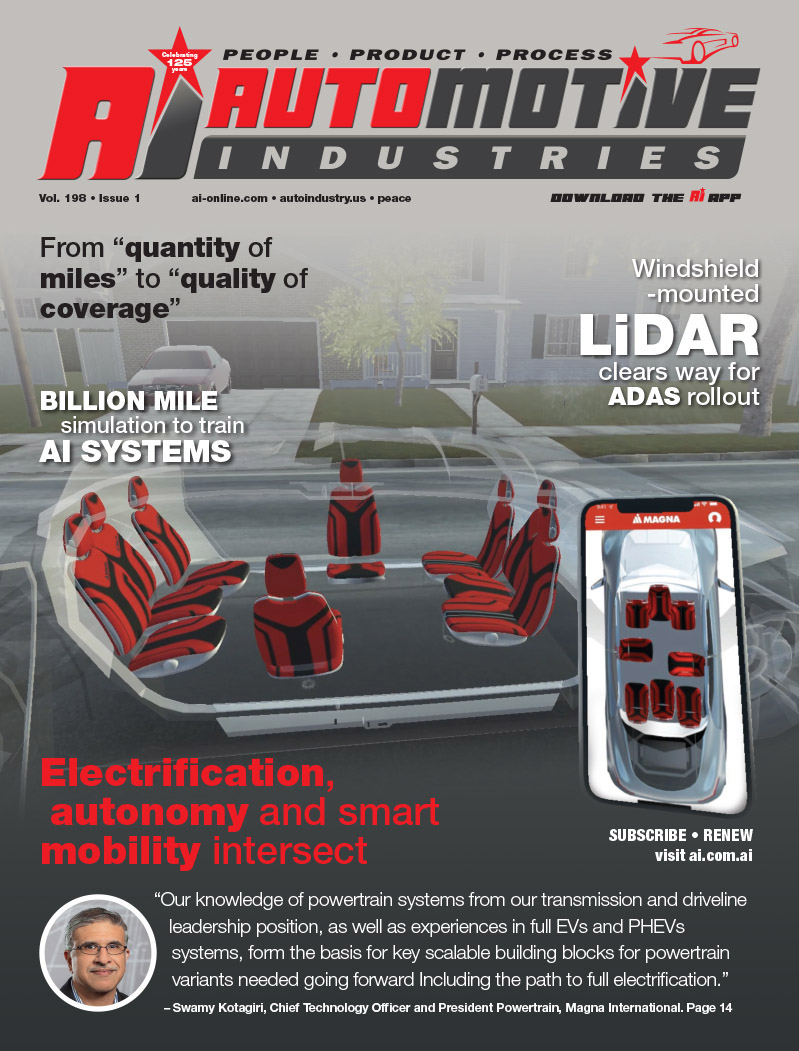
Automotive interiors are a hotbed in the consumer’s demand for vehicle personalization, and perhaps no component is taking center stage more rapidly than the instrument panel (IP). No more is the IP simply a place to stuff the radio: today’s instrument panels often control the interior design theme for the vehicle.
“It’s like the industry has had this lakefront property it’s been letting lie, and now we’re ready to build on it,” says Bob Kinney, executive director of engineering, design and interior integration for Intier. “There’s a good bit of valuable real estate on the instrument panel.”
Without a doubt, the biggest change occurring in instrument panels is the integration of sophisticated electronics. The impact of highly integrated IP electronics has led to increased functionality in smaller spaces, which in turn, frees up valuable space on the instrument panel that can be used for up-front storage. For example, Kinney says, new ways of integrating electronics and interior trim offer controls embedded in the trim; the trim can be opened to offer additional storage space — space that used to be needed for electronics. Future IP storage areas will be dedicated to specific things such as purses, cell phones and trash management. Integrating duct work for HVAC systems has also saved IP space.
It may not sound so glamorous, but Lear’s Kenneth W. Shaner, vice president, instrument panel cockpits and door systems, confirms that “up-front storage space on the IP is going to be big. We’re working to reduce the number of controls on the IP to clear more space for storage as well as relocating some of the controls into less critical areas.”
Yet, the truly big story is in the electronics themselves, which are bringing a new level of vehicle personalization into a market increasingly dominated by consumers who want their vehicle to reflect who they are.
“OEMs and suppliers are working very hard to ‘wow’ the consumer,” says Albert Faraj, product planning and strategy manager for interiors at Visteon, “and IP personalization plays a huge role in allowing the driver to say, ‘This is me. This is what I like.’”
Electronics: Aesthetics and Function
“The most striking trend in IP electronics is the new levels of vehicle personalization and customization that can be achieved,” says Intier’s Kinney. “The IPs of tomorrow will dial in to individual consumer tastes in both features and aesthetics.”
From the aesthetics side, Kinney says many of the IPs on the road today look “designed by committee.” In the past, the manufacturing process prohibited how IPs could be designed, because many components such as the radio and trim were ordered separately. Now, the pieces and parts are integrated, and with low-profile switches, higher quality plastics and flat, ribbon-like wiring systems, the various IP parts can be sewn together seamlessly with the trim. “Today, we can use the theme of the Class A surface to marry with the electronics,” says Kinney. “It all becomes a harmonious part of the IP picture frame.”
![]() |
Lear’s Touch Switch technology uses an electronic field sensor that detects when a person’s finger disturbs the electric fields close to the control’s surface. |
A good example of the latest in technology-enabled design is Lear’s integrated center stack with Touch Switch technology. These touch controls use an electric field sensor that detects when a person’s finger (or conductive object) disturbs the electric fields close to the surface of the control. Touch controls are prevalent in high-end consumer products such as big-screen TVs, high-end kitchen appliances and exercise equipment. The touch technology offered by Lear offers styling flexibility; improved interior design harmony; vehicle weight savings; complexity reduction; and controls that are easier for the consumer to clean.
Jim Geschke, vice president of electronics integration for Johnson Controls Inc. (JCI), says, aesthetically, the center stack is where most of the design changes are taking place. “In luxury vehicles, there is a significant migration toward integrated center stacks,” he says, “with navigation, radio, HVAC, etc., all located in one universal package.” Geschke believes that design trend will soon be migrating to mainstream vehicles as well.
There’s also an emerging design preference for the “floating” center stack coming off the console. Yet, the integration of electronics into the IP brings more of a focus on function and performance than concern about meeting geographical specs, says Visteon’s Faraj. “We’re looking at the intelligence of packaging certain electronics together,” he says. “What function and performance does each one bring? We want to be first to market with a great new technology, but innovation is not enough — it must be a useful innovation.”
Lear’s Shaner says one of his company’s most important roles is helping OEM customers understand the range of IP electronics and select what each vehicle really needs. “We’re finding that lately, OEMs are willing to make a trade for other things in the vehicle to add enhancements to the IP,” he says. “They’re looking for whatever technologies can drive their best-in-class rating. Still, we ask our OEM customers, ‘If it doesn’t integrate well, is it worth it?’ We often find ourselves helping OEM customers determine what to take out, not only what to put in.”
On the features side, electronic functionality is increasing at a dizzying pace. “IPs of the future will offer intuitive personalization way beyond what we see today in basic ‘vehicle memory’ systems,” says Rich Hager, cockpit applications engineering manager for Intier Automotive. “For example, in operating the vehicle’s electronic systems, a driver will begin to use the same keystroke pattern over and over. The IP computer will pick up on this and will start to introduce the first keystroke in the driver’s pattern as soon as the driver begins interacting with the system.”
“The whole IP will begin to function like a computer,” agrees Lear’s Shaner, “allowing vehicle owners to plug in personal data sticks into the center stack. Each data stick will contain programming for the individual’s preference in satellite radio, GPS, seat position and firmness level, vehicle temperature and more. Kids will have their own data sticks and everything will be voice operated.” Shaner says these technologies will be in vehicles sometime between the next round of new programs and 2009.
Navigation systems are another area in IP functionality expected to see continued growth. “In-vehicle navigation systems haven’t caught on as big here in North America as they have overseas,” says Geschke. “In Japan, they are an absolute necessity, in Europe they are increasingly popular, but North America has a good base road system, so navigation systems aren’t as necessary.”
Geschke says JCI’s answer to that trend in North America is a sort of “bridge technology between your basic compass and a navigation system.” Called Point™ Location Based Trip Information, the system utilizes GPS technology and a digital map linked to point-of-interest data to provide pertinent trip information regarding food, gas and lodging options in the area in which a vehicle is traveling. Also provided is relevant address and cross-street information. Geschke says it’s much simpler to use and much less expensive than a full-blown navigational system.
Yet, while suppliers have numerous new technologies that could be integrated into a vehicle, they point out that more attention should be paid to the fact that consumers are still determined to bring their own electronics into their cars and trucks. Thanks to integrated on-board entertainment systems, desperate parents are no longer plugging a TV into their vehicle’s cigarette lighter and strapping the monitor between the driver and front passenger seats with bungee cords. Still, what the fact that most people talk on their cell phones when driving? about a consumer’s PDA, Blackberry or iPod?
An automotive application of hands-free voice technology was actually introduced by Visteon back in 1998 with Jaguar. The earliest systems allowed the driver to control climate and radio presets by voice. As voice technology improved over the years, Visteon saw it as more of a safety technology than anything else. By 2003, three BMWs were launched in Europe with Visteon’s MACH® VoiceLink system, which interfaces with Bluetooth wireless technology and allows anyone with a cell phone containing Bluetooth to use it hands-free in their car. Visteon’s first installation of MACH VoiceLink in North America is in the 2004 BMW 3- and 5-series and the X7. Visteon also has a contract to mass produce the MACH VoiceLink technology in a Nissan vehicle in 2006.
![]() |
Hands-free voice technology systems like JCI’s BlueConnect allow anyone with a cell phone containing Bluetooth wireless technology to use their phone handsfree through the vehicle’s speakers. |
“But, we’re fooling ourselves if we think that people are going to stop talking on their cell phones in the car,” he continues. “A good, voice-activated phone system allows drivers to keep two hands on the wheel and eyes on the road at all times.” With that in mind, Geschke thinks handsfree voice systems should be viewed as a necessary feature, not a luxury.
“As long as your phone has Bluetooth and it’s turned on, as soon as you enter your vehicle, the vehicle is interacting with your phone,” he explains. “Bringing Bluetooth wireless capability into the vehicle opens up endless opportunities to customize a consumer’s driving experience by integrating his personal electronics with the electronic system of his vehicle. For example, some BMWs now offer an access port for iPods in the form of a mechanical connection from inside the glove box. With Bluetooth technology integrated with the vehicle’s electronics, a vehicle could also offer wireless iPod access.
“Consumers are going to continue to bring their personal electronics into their vehicles,” Geschke says, “so, we might as well do whatever we can to integrate them in a safe manner.”
Money-Saving Materials
When it comes to efficiencies in IP production, innovative materials and processes are often the starting point. “The main trend in IP materials is the same as in all parts — cost reduction,” says Dr. Charlie Reid, business manager of Solvay’s Interiors Business Unit. “Basically, there are two kinds of IP materials — hard IPs used in high-volume vehicles and soft IPs used more in high-end vehicles. Either way, cost reduction is on everyone’s mind.”
“It varies by region, but in Europe we’re seeing a focus on high-end materials that offer softer IPs and can help OEMs achieve brand differentiation,” says Visteon’s Faraj. “In North America, OEMs are looking for improved appearance with a focus on high-value rather than highend. Europe is more tactile, North America is more visual.”
Reid says thermoplastic polyolefins are making great progress in replacing traditional PC/ABS material in hard IPs. “By the time the new programs come out in 2005 and 2006, we’ll be looking at a market that is 50 percent PC/ABS and 50 percent TPO,” he predicts. It would be even greater, he says, but some OEM part designers are comfortable with their old PC/ABS material and have resisted making the change.
One of the latest developments bringing efficiencies in soft IP materials is the introduction of aromatic isocyanate-based polyurethane spray skins such as BASF’s Elastoskin. “Polyurethane sprays in and of themselves are not new,” says Todd Green, BASF market development manager, polyurethanes. “They were introduced several years ago as a way to produce a soft IP skin with excellent physical properties, gloss control and high grain definition.” Green says the new aromatic polyurethane skins are more efficient because they are in-mold coated (IMC), not post-painted.
“These new skins provide high UV resistance and grain definition with a soft luxurious feel over a wide temperature range,” he says. “There is no need for plasticizer like in thermoplastics, cycle time is faster than typical slush processes, mold temperature is low so tools don’t wear and the IMC process provides the most efficient means of achieving multi-color parts.”
Green says there’s often a false perception about the in-mold coated polyurethane skin. “Many people think that any time you add a coating to a component, it adds cost, complication and a greater potential for peeling and scratching. But, that’s a false perception with the aromatic polyurethane skins, because the wet-on-wet chemistry process allows the coating and the polyurethane to bond directly. This is not a typical postpainting process most commonly used for plastics.”
Still, much of the old stigma about painting remains, accounting in part for the rise in popularity of molded-incolor technology. “Everyone wants to eliminate the traditional painting process,” says Lear’s Shaner. “Molded-incolor is gaining popularity, as the trend toward soft, durable low-gloss IPs emerges.” Shaner believes soft-touch materials will take over IP designs of the future, adding that these materials also act as sound-deadeners.
“Lear has invested quite a bit in injection molding, because we feel it addresses the craftsmanship issue,” he says. “Injection molding is best for sharp grain definition, integrity and gloss control. It also offers flexibility and design freedoms because it helps eliminate molding lines and helps us achieve very close tolerances to cut down on interior buzz and squeak.”
Another factor that could influence IP material selection is the increasing attention to recyclability. “Within the next five years, we’ll see mono-material instrument panels,” predicts Solvay’s Reid. “This means that at the end of the vehicle’s life, the IP can be ripped out and tossed in the shredder for recycling. Tomorrow’s IPs must offer the ability for all the plastics to be reclaimed together without the costly need to separate one material from another.”
Lear’s Shaner agrees with Reid. “IPs are being hit for cost control as much as any other part in the vehicle, and any material or process that can bring new efficiencies to the table and still meet specs will have a promising future in the industry.”
All-TPO Instrument Panel is a First for GM North America ![]() Traditionally, GM instrument panels have been built using painted PC/ABS parts or vinyl skin-and-foam construction. The unpainted TPO panel is a lower-cost alternative, because it is molded with a grained Class A finish, eliminating the cost of secondary finishing operations. The instrument panel in the Chevrolet Colorado and GMC Canyon compact pickup trucks is the first all-TPO design by Intier Automotive and the first such application by General Motors in a North American vehicle. |
Tomorrow’s IPs at a Glance
|
More Stories
Your Guide to Filing a Car Accident Claim
Steps to Take Immediately After a Car Accident
What Makes SUV Cars More Prone to Accidents?