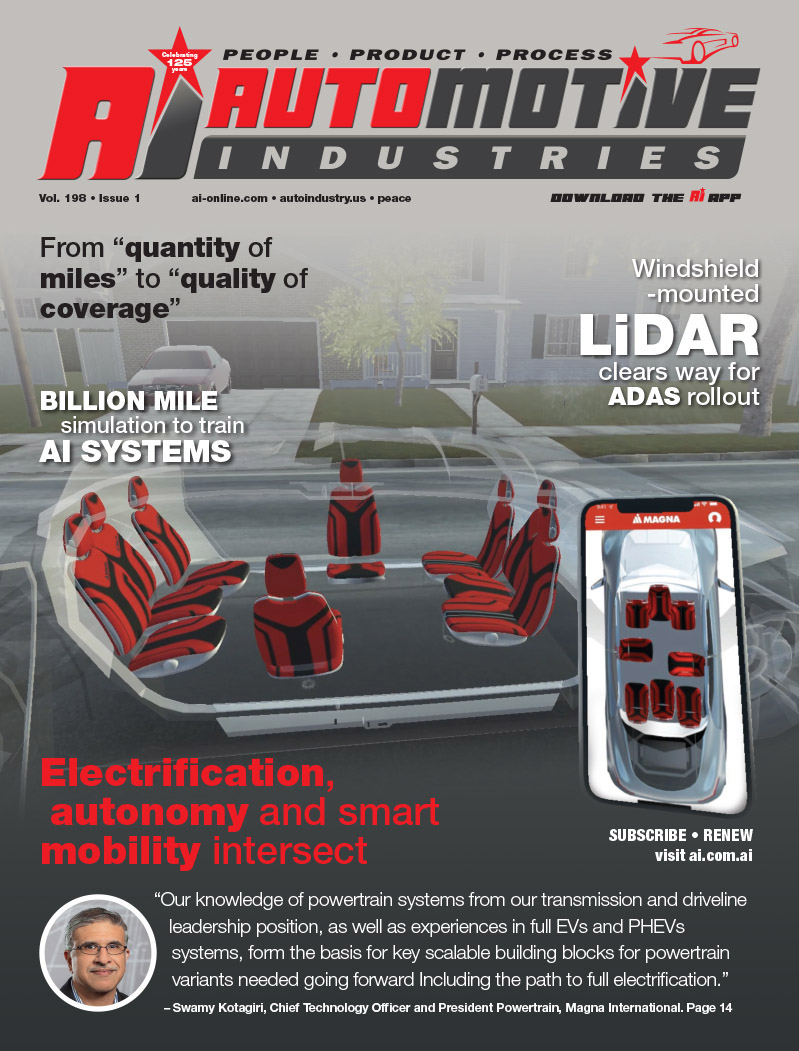
Renault’s Romanian Route
Renault’s Dacia plant gears up to build a quality, $5,000 car for Eastern Europe.
Louis Schweitzer, outgoing chairman of French carmaker Renault, has always been slightly nervous about the constantly escalating costs of ordinary family cars. Adding more and more features just pushed up costs with no real benefit for buyer or carmaker, he argued. One of his lasting legacies, apart from the successful alliance with Nissan, will be the Logan, the so-called €5,000 ($5,000) car now in production by Dacia, in Romania, which Renault bought in 1999.
![]() |
Logan is built on the Renault-Nissan B platform found under the Nissan Micra. It will also be used for the next Renault Clio. The Logan uses the front axle, door handles and steering wheel from the current Clio, and the heating system is the same as what will be used by Renault on other B segment cars. |
Now, with almost €500 million invested, it is turning out a car that is thoroughly modern in terms of fit and finish, but without the frills. And this is without going down the route to automation. Pitesti is still, by Western standards, a labor-intensive plant.
So how have the savings been made? Carryover of parts was one significant saving. Logan is built on the B platform of the Renault-Nissan Alliance, already in use on the Nissan Micra and it will also be used for the next Renault Clio. From current Clio, Logan uses front axle, door handles and steering wheel and the heating system is the same as what will be used by Renault on other B segment cars.
Design-to-cost was crucial if Renault was to meet its €5,000 target. The dashboard for Logan is a single moulding aimed at giving a robust feel rather than a fancy sculptured facia made up of different parts and colors. This produced savings on tooling and assembly operations.
The body sides produced another problem.
Traditional laser butt-welding of steels of different thickness to produce a monobloc component — which is heavy and manipulated by robots — was out of the question. There are no ultra-high tensile steels available in Eastern Europe, and installing laser butt-welding systems would have been prohibitively expensive.
The solution was to design Logan body sides using two pieces of steel, which are easier to handle, joined using traditional welding techniques and sealed with mastic.
Windshield and glass curves have been kept to a minimum to help keep machine tool costs low. Using a single window in the rear door avoids the cost of adding a quarter light. Sourcing from local suppliers was another critical factor, as was encouraging Renault’s existing suppliers to set up shop on a new supplier park within the Dacia factory complex (which is vast, covering some 9.5 million square feet). Not easy, since many suppliers were skeptical about the whole project. It worked, though, and 65 percent of parts bought in from suppliers are produced locally. In all, 26 of Renault’s frequent suppliers agreed to set up in Pitesti, seven of them inside the supplier park.
The entry-level Logan does not have power windows, central locking, fingertip radio controls on the steering wheel or sophisticated seating adjustments. These are all on the options list. It does have excellent brakes (you should see how the Romanians drive …) and first-class road holding.
Renault 1.4 and 1.6L petrol engines were available from launch and this year a 1.5L common rail diesel engine will be added. The sales target is 700,000 vehicles by 2010, all part of Schweitzer’s ambition for the Renault group to sell 4 million vehicles a year by then.
In addition to the Pitesti plant in Romania, Logan will also be made in Russia, Morocco, Colombia and Iran, with the same goals of cost-effective production close to its markets. In Russia, in partnership with the Moscow City Authorities, initial production capacity will be 60,000 vehicles a year. The Somaca plant in Morocco has a capacity of 30,000 units a year. Medellin, Colombia, will come on stream in 2006, with annual production capacity of 44,000 units.
The most recent major decision concerned production in Iran, with the announcement of the creation of a joint venture company, Renault Pars, in partnership with the Iranian automotive industry. Logan will be made in Iran from 2006, with production capacity of 300,000 units a year.
Whether the Dacia or Renault badge is used will depend on the characteristics of each market and on how long and in what circumstances Renault has been established there. In Central Europe, Turkey, northern Africa and the Middle East, Logan will be marketed under the Dacia brand. Entry-level vehicles in a country like Poland account for 30 percent of the automobile market.
On other markets where Renault has a relatively limited presence, Logan will help to win new customers for the brand. In Russia, for instance, Logan will have a Renault badge and will be competing in the segment of new vehicles sold at between 8,000 and 10,000 euros ($8,000-$10,000), which account for 90 percent of the market.
Logan is, by any measure, a brave move, but one that looks like it will prove the sceptics wrong. Motoring without frills could be what we all really want.
More Stories
Best Wheel Size for Off-Road Adventures: What People Get Wrong
Trusted Auto Collision Repair That Restores Both Performance and Peace of Mind
What You Need to Know About Tire Pressure in Winter vs Summer