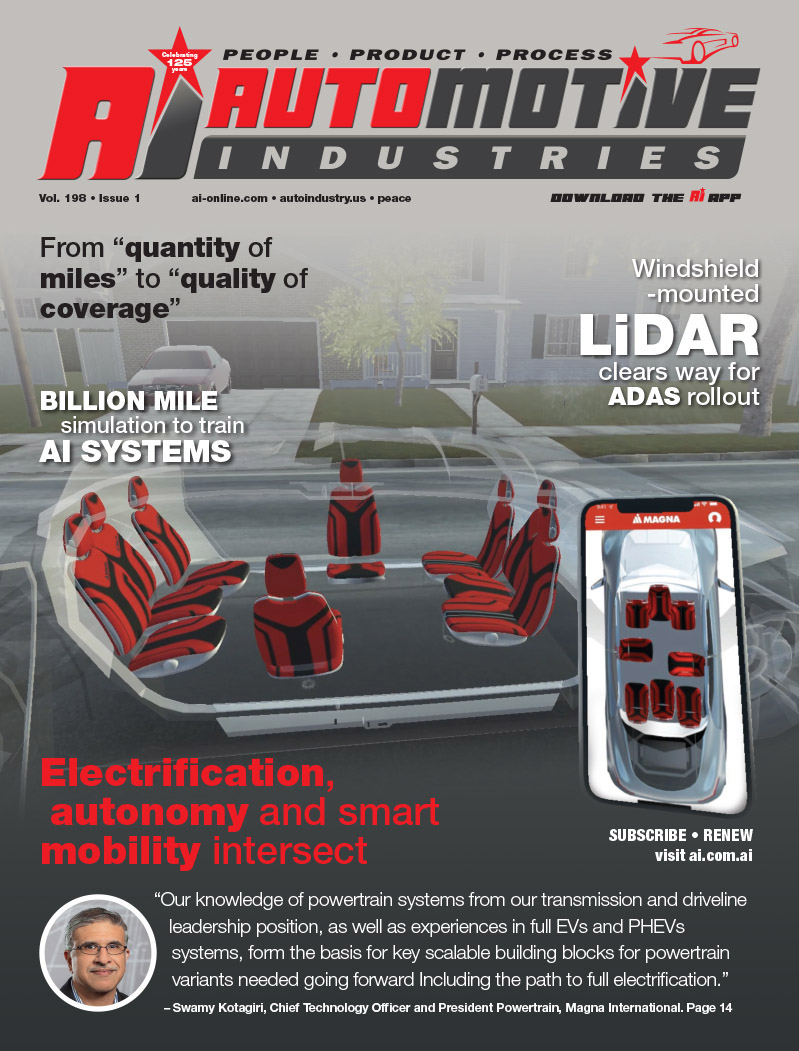
Hi-tech industries, such as automotive and aviation, are keen to produce more components in titanium because of its attractive combination of properties. It has an excellent strength-to-weight ratio, being twice as strong as stainless steel but about half the density, and is four times more corrosion resistant than stainless steel without any need for any special coating treatment.
In the fourth and final article for Automotive Purchasing News, QinetiQ’s Dr Stephen Mason examines how the company has developed a revolutionary new manufacturing process for titanium alloy powders, and how this will enable the automotive industry to manufacture lighter vehicle components more cost-effectively.
Titanium is potentially cheaper than stainless steel, since it is one of the most plentiful elements in the Earth’s crust. The machinability of titanium is similar to stainless steel, and in most cases, its processing can be done with standard equipment. Titanium is also environmentally friendly, hypoallergenic and has a good public image, as it is regarded as a ‘hi-tech’ metal. It has a comparatively low stiffness-to-weight ratio, and this means that it can be used in the automotive industry for vehicle springs. It is also used in the manufacture of sporting goods such as golf clubs, and in jewellery because it is capable of being anodised in vivid colours.
There is consequently a large potential market for titanium, provided that it can be produced cost-effectively. QinetiQ, by industrialising a new electrolytic powder production process, is poised to capture a significant share of the emerging titanium powder market.
Historically Expensive
The automotive industry has always been interested in using titanium, from engine parts such as valves and con-rods, through to springs and cosmetic parts such as radiator grills and trim, but in general has had to reject it as being prohibitively expensive. The reason that titanium is expensive is due to its reactivity at high temperatures, making it costly to extract from the ore, to cast into ingot form and also to process into useable form such as bar, plate or rod.
The existing extraction method for titanium is known as the Kroll process and has remained fundamentally unchanged since it was introduced over 50 years ago. It takes titanium ore as its raw material and relies on a reaction between titanium tetrachloride and magnesium to form titanium ‘sponge’. Alloy ingots are then produced by a process known as vacuum arc (re)melting (VAR) in which the sponge is remelted up to three times and the alloying elements added as metals or master alloys. These remelts are required to ensure alloy uniformity and purity. The resulting ingots are further processed into bar, plate or rod, which typically costs around £15-60 per kilogram, up to 30 times the equivalent cost of steel. If these are then machined into components, often 90% of the original material is cut away – a very wasteful process.
The automotive industry has led the adoption of powder metallurgy manufacturing methods to produce complex engineered components cost effectively, without the need for extensive machining. Steel or iron has traditionally been used because it has historically been cheaper to obtain in powder form than titanium. High quality titanium powders often cost in the region of £60-120 per kilogram compared to stainless steel powder costing less than £10 per kilogram.
QinetiQ’s Process
“In our process we can go straight to producing titanium alloy powders from a widely available and inexpensive metal oxide,” explains QinetiQ’s Dr Stephen Mason. “This has the potential to reduce the market price for powdered titanium significantly. Component manufacturers will now be able to look seriously at titanium powder metallurgy as a viable commercial production process.”
The original FFC Cambridge Process [also known as ElectroDeoxidation (EDO)] on which the QinetiQ process is based, was invented by Cambridge University and is now being developed and scaled up by QinetiQ. EDO converts titanium dioxide directly into titanium metal by a reverse electrolysis process.
The titanium dioxide powder that forms the raw material (feedstock) for the QinetiQ process is a chemical widely used for a number of applications. Millions of tonnes per year of high purity titanium dioxide powder are produced as a whitening agent for the paint production industry at a cost of approximately one US$ per pound of powder. It is also widely used in the paper and food industries. The feedstock is therefore readily available at a low cost through economies of scale.
Alloys can be created in a single step using the EDO process by mixing the titanium dioxide powder with oxides of the alloying additions. During the de-oxidation process the elements, minus the oxygen, combine to form a metallurgical alloy. This creates an alloy of better uniformity and more safely than the traditional VAR method used following extraction of titanium by the Kroll process.
QinetiQ has developed patented modifications to the EDO process to permit production of cost effective, high purity titanium alloy powders. This powder is suitable for use in the powder metallurgy manufacturing technologies currently used by the automotive industry, enabling titanium to be more widely used.
Benefits to automotive industry
“It is still early days but we have high hopes for this technology,” concludes Dr Stephen Mason. “Titanium has so far maintained its exclusive status as it has been difficult to manufacture cost-effectively. With our new process we should be able to provide competitively priced, high quality titanium alloy powders – growing demand and fulfilling supply. We envisage titanium becoming a relatively common material over the next few decades.”
The EDO process results in a better quality of product than the Kroll method of extraction, and through careful control of the process, QinetiQ can produce in one step either sponge (for melting or direct compaction into ingots), or powder or near-net-shape products in either pure titanium or alloys. This process can be applied to a wide range of titanium alloys attractive to the automotive industry, including titanium aluminides suitable for engine parts and titanium-nickel shape memory alloys that can be used in actuators, as well as the standard grade alloys. By mixing other metal oxides with the titanium dioxide during the initial process, a range of alloy powders, each with specific characteristics tailored to a particular need, can easily, and cost-effectively be produced.
The strength and performance of the product is not compromised by the EDO process, which relies on cheap, readily available feedstock and electrolyte, and is relatively environmentally friendly. The powder production process is currently a batch process with a more rapid cycle time compared to that taken to manufacture titanium powders using the current processes, and it is envisaged that optimisation of the process during industrial scale-up will result in the process becoming even quicker, and more affordable. There is also a potential for continuous production that was not possible with the existing method.
Consequently, the cost and time taken to produce titanium alloy powders suitable for use in the powder metallurgy processes pioneered by the automotive industry are set to fall significantly. Such technologies result in wastage of a maximum of 10% of the powder they use and are a much more cost-effective and competitive way of producing complex engineered titanium components than traditional machining.
Initial production at QinetiQ’s pilot plant is expected to start later this year, with commercial quality powders becoming available by early 2005. Once fully commissioned, QinetiQ will be able to supply a wide range of titanium alloy powders at tonnage levels per year. The existing plant can be easily scaled with the addition of further units to meet anticipated market demand for affordable titanium alloy powders.
In parallel with the new titanium powder production capability, QinetiQ is also developing the special technologies needed to convert titanium alloy powder into finished parts. QinetiQ is working with a number of companies from various market sectors to demonstrate the technical and commercial feasibility of manufacturing components from titanium powders.
The automotive industry should therefore be in a position to exploit the advantages of titanium and titanium alloys over other metals at long last.
More Stories
Your Guide to Filing a Car Accident Claim
Steps to Take Immediately After a Car Accident
What Makes SUV Cars More Prone to Accidents?