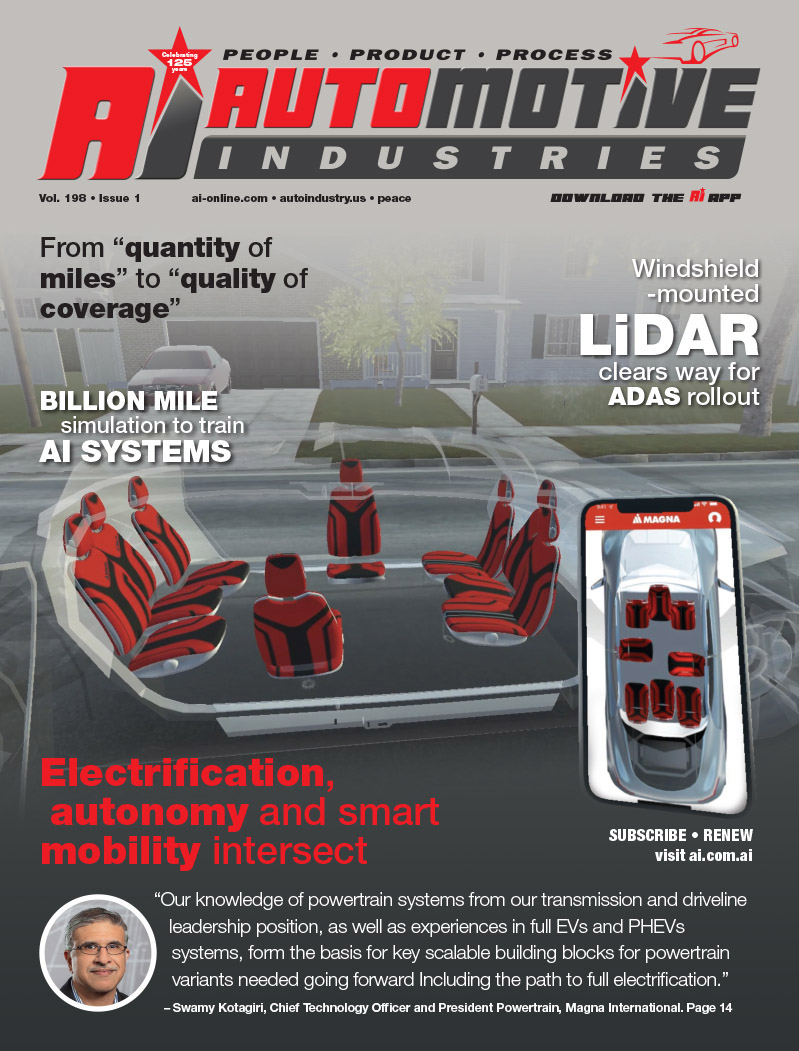
Globalisation of the automotive industry and the increasing focus on the quality of the vehicle as delivered to the final customer have created the need for a new kind of service – one which combines Vehicle Inspections with Automotive Risk Management services. C.A.R. (Control Automotive Risk) Consulting Group, Managing Director Timo Pasila talks to Automotive Purchasing News.
Automotive Purchasing News (APN): In a cost-down environment, why do we need to add another logistics cost by appointing a vehicle inspection and risk management company?
Pasila: We often see that the automotive logistics industry is being held liable to other-than-transport related damages to the vehicle. Consequently, the logistics chain is being placed in the uncomfortable position of having to settle claims with their client or the final receiver, which relate to (minor and major) imperfections of the finished vehicles. This reality combined with the fact that multiple OEMs do not yet have a well-defined liability standard, clearly calls for the need to have proper risk management in order to create an awareness and acceptance within the OEMs about the actual quality standard of their vehicles, as well as the need for the automotive logistics industry to properly use all vehicle inspection data available to defend their case towards the OEMs.
If we take a look at all the vehicle inspection data available, we note that (roughly) just 10-20% is actually related to transport, whereas the other 80-90% is related to manufacturing deficiencies. With this in mind, we are astonished to note that the automotive logistics industry is mainly focused on the transport-related damages (e.g. in order to improve their quality of transport), while the other 80-90% are merely used to reject any eventual claim from the final receiver.
In our view, much more should be done with this valuable information. We strongly feel that the automotive logistics industry needs to move from the traditional approach of the use of the vehicle inspection data (primarily, just to reject claims) towards a more proactive approach and share the vehicle inspection findings with the OEMs, not only in order to assist them to improve the quality of the vehicles, but also to create the awareness and acceptance that the logistics industry cannot be held liable for the quality deficiencies of the vehicles.
APN: You have made the claim that Risk Management can actually improve the quality of vehicles. How?
Pasila: Through proper use of the available inspection data “Automotive Risk Management” and strong communication between the logistics industry and the OEMs, the quality of vehicles will actually be improved. This process will also bring significant costs savings as well as service improvement to the automotive logistics industry. At the moment, we feel that too many people in the industry (both the OEMs as well as the logistics industry) are playing, what we call the “ostrich-game,” by “putting their head under the sand” in order to avoid unpleasant claim vs. quality negotiations, instead to proactively tackling the problem (which both parties acknowledge that exists) head-on.
How Automotive Risk Management really works is probably best described by General Electric’s former Chairman Jack Welch: “Most of the information a manager will need to run a business will reside on a computer screen in a ‘digital cockpit’. It will contain every piece of real-time data, with automatic alerts spotlighting the trends requiring immediate attention. While information will be available as never before, it will always be human judgement that will make the organisation go (forward).”
APN: You highlighted two parts “digital cockpit” and “human judgement”. Why?
Pasila: Transparent management information is fundamental for decision makers to know where to intervene. Quality managers in the logistics industry need to know at all time where their vehicles are, in what condition and what could be the financial consequence (eventual claims). They also need to be able to identify where in their logistics chain are the major risks of loss and damage, in order to implement the necessary damage prevention measures.
They can pilot this process through our “24 C.A.R.A.T.” system, which is a business intelligence tool through which our clients are able to analyse their the quality performances in any way they like (e.g. damage type, damage cause, damage location, liable party, best driver, most claiming dealer, best vessel, worst stevedores, etc…) The C.A.R. Consulting Group collects all available vehicle inspection data into a central database, while through the “24 C.A.R.A.T.” system, we show the data in a “digital cockpit” in order to create a “helicopter view” for the automotive logistics industry. On the basis of these data, we work closely together with the quality managers (“human judgement”) of the automotive (logistics) industry in order to analyse and identify the problem areas, and decide on where to intervene in order to reduce the risks of loss and damage and consequently save costs and improve service. The underlying idea is to avoid damage in the first place, rather than finding someone to pay for it.
APN: Should your service be “independent”?
Pasila: In our business it is fundamental to be completely independent, and not have any ties to 1) OEMs, 2) transport companies or 3) PDI centres – it would be a natural conflict of interest! In this respect, we also need to consider at the outset that there exists a large “grey area” in the damage classification, due to unclear liability quality standards and inspection guidelines of the multiple OEMs, for which it is sometimes difficult to correctly classify whether origin of the damage comes from the manufacturing process, or actually relates to the transportation of the vehicle.
Any ties with OEMs would directly have an averse impact on the independence; the transport companies would not feel properly protected, as they would suspect that the vehicle inspection and/or risk management company would side with the OEMs in order to facilitate subtle, however unjust claims settlement with its carriers. It is a true fact that OEMs often consider their product as perfect, especially when the vehicle passed their internal final quality control at the manufacturing plant. However, unfortunately the quality standard does not always correspond to the requirements of the highly demanding markets. In case the vehicle inspection company would be linked to an OEM, it could be coerced not to record these deficiencies (or anomalies) at the manufacturing plant, while subsequently the automotive logistics industry will repeatedly be held responsible at the end of the day for quality related deficiencies.
If we look at the origin of vehicle inspection companies, we see that they are traditionally appointed by transport companies, in order to report all damages and anomalies prior to the moment the vehicles enter into their care and custody, and consequently to protect them versus damage claims they should not be held liable for. Coming back to that “grey area” in damage classification, in case vehicle inspection companies would be linked to transport companies, they could easily be influenced to reject any damage (classify as other-than-transport-related) in case there is the minimum of doubt about the actual liability.
Perhaps the most obvious link which must be avoided by our industry to maintain our independent status is any co-operation with PDI facilities (or body-shops). It is a fact that the PDI process is an essential part of the automotive logistics chain, however (and we have seen countless examples of this event) due to the lack of clear liability and inspection standard, and moreover considering the “grey area” in damage classification, through any tie with a PDI centre, vehicle inspection companies could easily be influenced to justify the repair of any damage (classify as transport-related) in case there is the minimum of doubt about the actual liability. Also in this case, the automotive logistics industry will repeatedly be held responsible at the end of the day for quality related deficiencies.
In this respect, complete independence and integrity is fundamental for our line of work; we need to function as a third party independent “judge” in order to accurately project the real situation to OEMs and the automotive logistics industry and clearly distinguish between transport-related and warranty-related damages and anomalies.
APN: Where is C.A.R. represented?
Pasila: We have a global presence. We provide our services on all continents, in all countries, at all plants, ports, vehicle hubs and distribution centres and dealerships; basically at every location new vehicles are produced, transported, delivered and repaired. In fact, it is very important to have a global presence, as it is the only way vehicle inspection standards and guidelines are applied equally at both the point of departure and the point or arrival. As a global company, we will be able to minimise the problems encountered with unclear liability standards, different inspection levels and damage classification/interpretation at different locations worldwide.
Quality
Every vehicle manufacturer (OEM) around the world has ongoing internal quality improvement programmes. However, what happens with the quality of their vehicles as they leave the factory gates, en route to the final customer, is predominantly controlled by numerous logistics providers (either linked to the OEM’s or independent) and automotive transport companies. Whereas the OEMs are proud of the vehicles they produce, the quality does not always satisfy the high expectations of the final customers. Often, the automotive logistics providers and the transport companies find themselves in the middle (as uncomfortable third party) between the powerful OEMs and the final receivers of the vehicles (either dealerships, PDIs or sometimes even the final customer).
More Stories
Your Guide to Filing a Car Accident Claim
Steps to Take Immediately After a Car Accident
What Makes SUV Cars More Prone to Accidents?