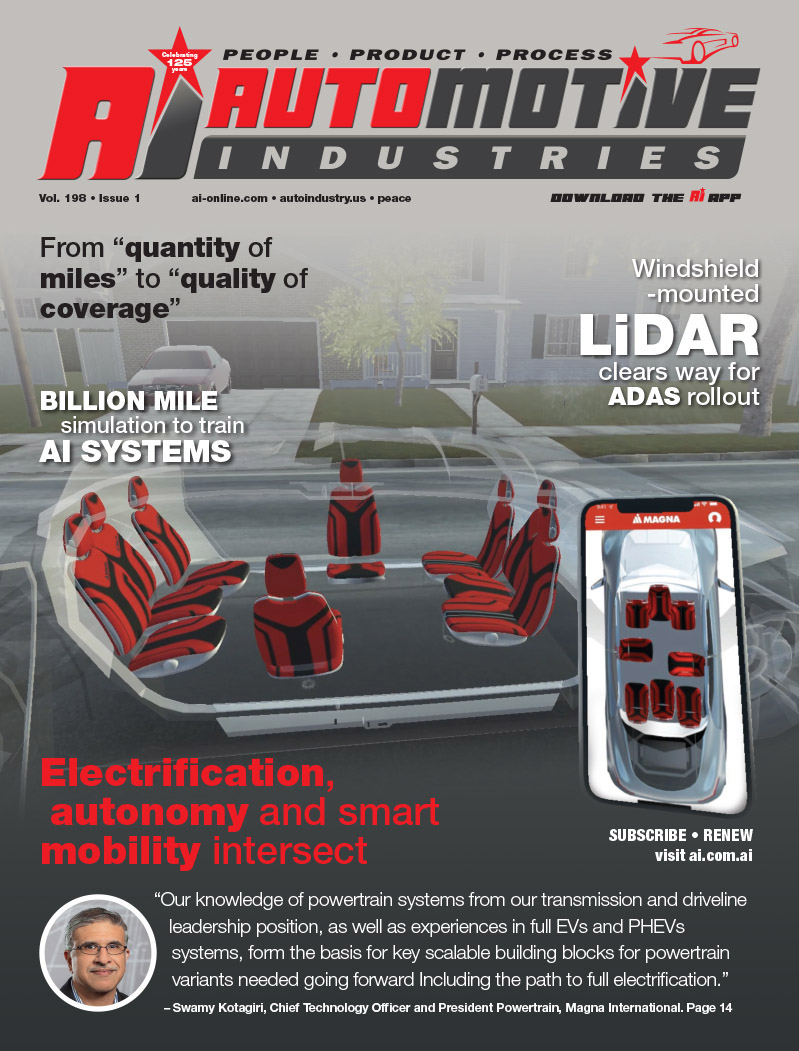
There are more environmental advantages to using aluminium in auto manufacture than the weight savings if suppliers look at the entire supply chain, which includes supplying molten material to the downstream users and the recycling of the metal at the end of the vehicle?s life. Steve Demetriou of Aleris talks to Automotive Purchasing News about some of the latest developments.
Automotive Purchasing News (APN): What is Aleris doing to help OEMs and component suppliers make lighter, safer, environmentally friendly and affordable vehicles?
Steve Demetriou: First of all, it is important to keep in mind that OEMs and their suppliers recognize that aluminium and other high strength, low weight, materials used in vehicle manufacturing can dramatically affect the safety and environmental performance of their vehicle fleet. In 2000 aluminium passed plastic in terms of content per vehicle to become the third most used material in automobiles and remains the fastest growing material used in automobiles today. The OEMs and their Tier 1 suppliers are increasingly choosing aluminium to improve fuel economy, reduce emissions and enhance vehicle performance ? all the while meeting or exceeding safety standards.
Many OEMs are designing in lower weight solutions to improve the performance, safety, fuel efficiency, and environmental friendliness of their vehicles. The Jaguar XJ, Audi A8, BMW 5 series are constructed with very significant amounts of aluminium. They are also best in class with regards to safety, performance, and fuel economy.
On a global basis OEMs have recognized that aluminium castings are highly competitive on a cost per pound of weight saved basis. In addition, they have come to realize that using aluminium to cut a vehicle?s weight by 10% can boost its fuel economy by 5-8% or 2.5 miles per gallon. That means a savings of up to 700 gallons of gas over the lifetime of the vehicle. Obviously a vehicle that uses aluminium to reduce weight uses less fuel and using less fuel also produces fewer greenhouse gas emissions. Over the average life of a vehicle, every pound of aluminium that replaces two pounds of steel can reduce carbon dioxide (CO2) emissions by 20 pounds. With respect to Aleris specifically, we have invested significant resources to help OEMs and their suppliers to improve the performance, safety, fuel efficiency and environmental friendliness of vehicles.
Supplying molten metal
Aleris has dramatically increased it capability to deliver molten metal to our customers which lowers their energy costs, lowers their dross generation, minimizes their capital requirements (i.e furnace relines) and increases their productivity. We have also established a number of long term partnerships with many OEMs to help them use more aluminium in their vehicles. As an example, Aleris is currently supplying molten A356 to General Motors? Saginaw Metal Casting Operations for their L6 lost foam castings for the 6 cylinder blocks and heads used in Trailblazers, Envoys and Rainiers. GM recently asked Aleris to expand Aleris? Saginaw facility in support of their need for alloy 319 molten for the Generation IV V-8 engine block that will be used in full size SUVs such as the Yukon, Silverado, Sierra and Escalade.
In Europe, Aleris has established similar long-term partnerships. Within five months, Aleris received planning environmental, building and operating permission for a new plant in Deizisau, Germany. As far as we know this is a record for Germany as usually permitting processes for industrial Greenfield operations take between one to three years. The plant will service the Mercedes Benz foundry of DaimlerChrysler in Mettingen, which is only 10 miles away. The plant will provide liquid metal just-in-time for casting of cylinder heads and engine blocks and recycle run-around-scrap generated in Mettingen. The initial capacity will be 60,000 tpy. Permission was already granted for the maximum capacity after an upgrading step of 120,000 tpy total.
APN: Where else could aluminium be used?
Demetriou: Aluminium casting shipments in the U.S are forecasted by Modern Casting to grow 6.4% on a year over year basis in 2005 and 18% between 2004 and 2008. This rate of growth is in large measure due to the penetration that aluminium is having at the expense of nodular iron castings. However, aluminium?s growth in automotive applications is not restricted to cast products. Aluminium is broadly applied to hoods, deck lids, bumper systems, heat shields, suspension components and a myriad of other applications.
One of the trends that we have seen in the U.S. is that consumers want larger, safer vehicles. One of the many challenges in vehicle design is to create a stronger and larger passenger compartment that maintains integrity in a collision, prevents intrusion of external objects, and contains occupants within the vehicle. Aluminium plays a part in the overall solution because it offers unique properties that allow manufacturers to keep (or even expand) the size/crush zone of vehicles while loosing the weight. Clearly, aluminium offers the vehicle designer the positive benefits of high strength and low weight that can reduce the aggressiveness of heavier SUVs. Studies have clearly shown that vehicle size appears to be very significant with regard to safety and that appropriately sized, lower weight vehicles constructed with advanced materials can yield efficient, environmentally friendly transportation.
You must also keep in mind that, according to the World Resources Institute, Americans still use 10 times more gasoline per capita than the world average. While the energy crisis of the ?70s helped to reduce oil consumption sharply, partly due to improved automobile fuel efficiency and increased conservation, over the last two decades, consumption has risen steadily and is now higher than it was at the peak of the crisis. The transportation sector has been responsible for all of the increase, rising 36% from 1980 to 2001, while annual oil consumption in all other sectors declined 19% in the same period.
When you analyze where the oil is going in the transportation sector in the U.S., it is clear to see that the sales of sports utility vehicles, pick-up trucks and minivans have risen, while their average fuel economy has decreased. If you examine cars, trucks, airplanes, buses, railroads etc, fuel consumption grew 20% from 1980 to 2001 and large trucks accounted for two-thirds of the increase, so this is an obvious target market for further aluminium penetration.
APN: What can be done to improve the recovery of aluminium scrap and what if any are the benefits to the OEMs (is there any way this will reduce the cost of raw materials?)
Demetriou: There are a variety of ways that scrap recovery can be improved for the OEM. These include, but not necessarily limited to, better scrap segregation, lubeless machining, state of the art recycling processes and advanced scrap inspection technology. Aleris has launched initiatives in a number of these areas, so as to differentiate ourselves from the rest of the competition.
As an example, Aleris has made significant progress in furnace data acquisition with the objective of providing the furnace operator with cognitive assistance to reduce process variation and improve recoveries. We have launched Six Sigma energy teams to lower natural gas usage. We are also working on a proprietary method to measure moisture in scrap on-line. Since moisture is a critical cost variable in many scrap types (i.e. UBCs) this technology will help insure that metallic value is properly measured at time of scrap receipt. Aleris is evaluating what may become breakthrough technology in scrap melting. These initiatives are essential drivers of economic value to our customers because they can lower operating costs, increase capacity and free-up working capital.
APN: What support do you offer to OEMs in terms of design and life-cycle planning?
Demetriou: Aleris has demonstrated the ability to support automotive OEMs in a full range of capabilities and high value services that range from scrap management to turnkey plant construction (i.e. GM Saginaw, DCX Germany). As the technological leader in aluminium recycling, Aleris has proven its ability to lower operating costs, increase capacity and free up working capital for its OEM customers. Our intent is to continue to leverage these core competencies to grow our share of the automotive market.
APN: How is consolidation of the aluminium industry going to affect purchasers in the automobile industry?
Demetriou: Consolidation can provide operating cost reductions through the closing down of obsolete capacity, economies of scale and the elimination of duplicate administrative costs. Further, it allows the reallocation of production to the most efficient facilities, and it allows the location of new capacity where energy costs are relatively low and where they can serve new markets.
With respect to aluminium industry consolidation, it is worthwhile to examine the ?root causes? of the trend. Clearly, there has been a lack of individual aluminium company and industry profitability. Specifically, there is excess secondary alloy capacity in the U.S. and Europe. Unfortunately, many producers in this segment have opted to continue to run facilities at the high end of the cost curve while chasing volume for volume sake.
Concurrently, major customers have consolidated and want suppliers of equal stature. On the scrap side, consolidation is rampant. From a primary perspective the number of producers is down by more than 50% with the top five now controlling over 60% of world capacity.
What some aluminium producers have learned is that consolidation can streamline their cost structure. It has enabled them to leverage best-in-class core competencies through the transfer of best practices. It improves the company?s competitive position through scale and scope. If done properly, it can yield stronger management, greater access to capital markets and the ability to pursue growth opportunities.
As the aluminium consolidation trend continues, customers will ultimately have suppliers who are more robust. Their vendors will have world-class technology and the cost structure that will enable them to compete in a global commodity.
APN: Where is Aleris positioned in terms of this trend?
Demetriou: Initially, Aleris will earn the right to grow. Our intention is to rapidly de-leverage our balance sheet while keeping a close eye on potential acquisitions. Rest assured that the combination of IMCO and Commonwealth is not the end of the road. Within three to five years, this company will be dramatically different from what it is today. Stay tuned!
More Stories
Your Guide to Filing a Car Accident Claim
Steps to Take Immediately After a Car Accident
What Makes SUV Cars More Prone to Accidents?