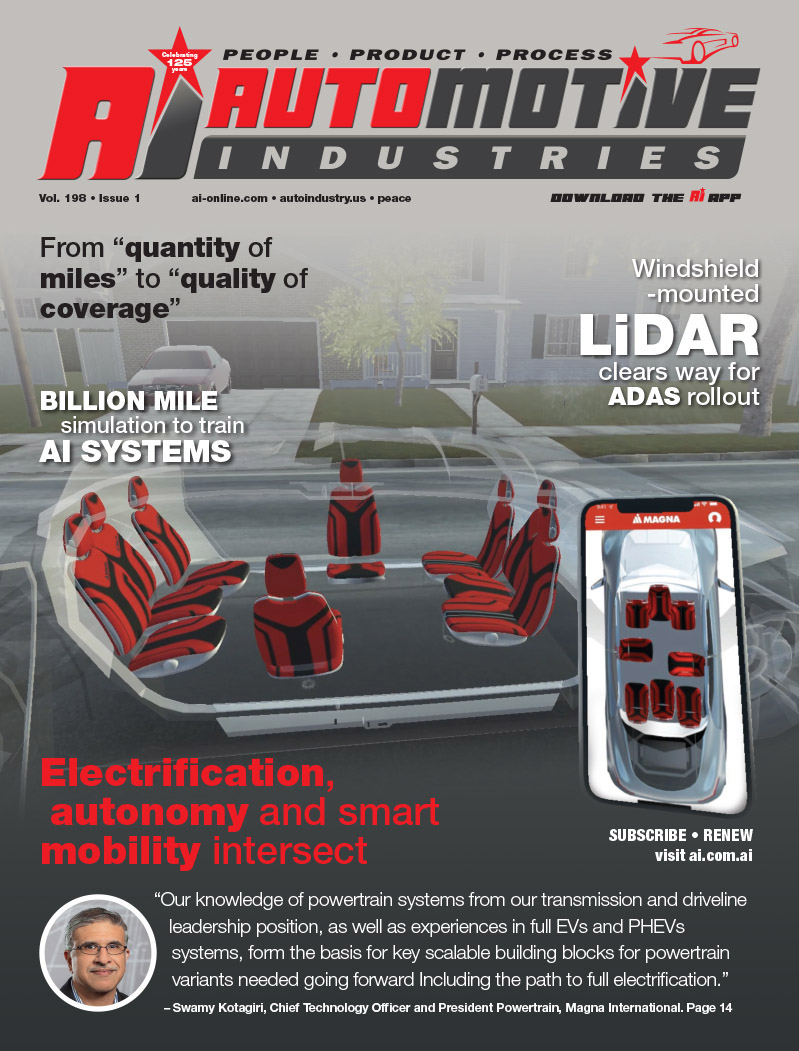
“In Asia, technology like ours and that of other vendors is widely accepted as the norm for developing new programs, and manufacturing with more than 80% of components being produced using CAD/CAM solutions. In contrast, in North America and Europe, more than 80% of components for interiors are still produced using technology that has been available for several decades. People are reluctant to change tried and true processes even though there is a possibility for significant savings,” says Thomas McKay, Lectra’s North American marketing director. He shares his thinking with the readers of Automotive Industries:
Automotive Industries (AI): You are, presumably, not developing integrated software and cutting technology just because you can there must be a need.
McKay Even if worldwide car production were not increasing dramatically, there are a lot of changes dictated mostly by consumers. Speeding up development time, comfort needs, new safety rules, and cost cutting are elements that have to be taken into account. In addition, mass customization of interiors (or at least several different options for a particular model) is also becoming a new trend. People are more sensitive to interior design and luxury than they were in the past. That’s why more and more cars are equipped with leather interiors (seats, door panels, consoles, etc …). We also see more of a mix with other new industrial fabrics.
There is a sort of fashion effect we could compare to the apparel industry. The result is that interior options are increasing dramatically, and the classical car mass production is moving to a new culture able to make all kinds of series (big, medium, small), which match these new needs.
There are basically three main requirements in the automotive industry,and Lectra has solutions for all three:
1) speeding up the design process,
2) flexibility to produce many variations, and
3) controlling the overall cost of a program.
Our solutions provide manufacturers with tools to master all of these needs. For instance, our Design Concept 3D software provides a virtual prototyping solution that drastically shortens the total design cycle, while also providing customers with flat patterns that calculate sophisticated strain analysis regarding the fit of a seat cover and take into account the material properties.
The software also provides the ability to visualize the virtual prototype and drape fabrics which is a powerful tool to marketers. Additionally, Lectra has developed a complete range of production tools including industrialization of patterns, nesting to achieve the highest utilization of materials and the generation of detailed work specifications to secure the global cutting process. These tools, incorporated with our complete range of cutting solutions developed specifically for the automotive market, ensure that we satisfy our customers needs for flexibility, productivity, and accuracy.
(AI): How does Lectra work with the OEMs? would they benefit from using your technology earlier in the design cycle?
McKay Our solutions help some customers shorten their design cycle by as much as 30% by allowing them to work concurrently on programs rather than sequentially, as they have in the past. Customers can now develop interior components such as seat covers directly from virtual 3D models as opposed to waiting for the actual foam to be developed. This dramatically improves the speed of design and efficiency in development, which represents a lot of “direct savings” (reduced costs) and “indirect savings” (faster time to market). In addition, as the component is initially created in a digital format, it is much easier for the OEM�s to communicate product specifications to their subcontractors as needed.
(AI): Is more responsibility falling on the Tier 1 suppliers to meet the artistic design specifications of the OEM?
McKay This trend to have Tier 1 suppliers develop artistic designs as well as manufacture components seems to be OEM specific. Some OEMs are willing to subcontract this work, while others are clearly still in control of the design process. Lectra is working closely with some car makers, such as Toyota, but also with Tier 1 suppliers like Johnson Controls. We work on long term projects with OEMs and Tier 1 suppliers (on a partnership and confidential basis) in order to define the best automotive design, industrialization, and manufacturing solutions. This is an excellent way to understand their needs better and help them achieve their objectives.
(AI): What opportunities are there in the after-market? Could an OEM, for example, boost its income and that of its dealer chain through a range of optional extras designed and manufactured using Lectras technology.
McKay If you consider Scion, it is clear that some OEMs have clearly understood that they can substantially boost their income and that of their dealer network by offering customers the ability to personalize their vehicles to a certain extent. This methodology in the design of cars will certainly allow the development of additional aftermarket options that consumers can choose in the future. The success of the Apple iPod and the multitude of available aftermarket options have clearly shown that consumers want to personalize their property, and the automotive industry will also benefit from this consumer trend if they can achieve it while controlling costs. Our solutions are ideally suited to allow OEMs, Tier 1 suppliers, and aftermarket companies to develop these alternatives quickly and cost effectively
More Stories
Best Wheel Size for Off-Road Adventures: What People Get Wrong
Trusted Auto Collision Repair That Restores Both Performance and Peace of Mind
What You Need to Know About Tire Pressure in Winter vs Summer