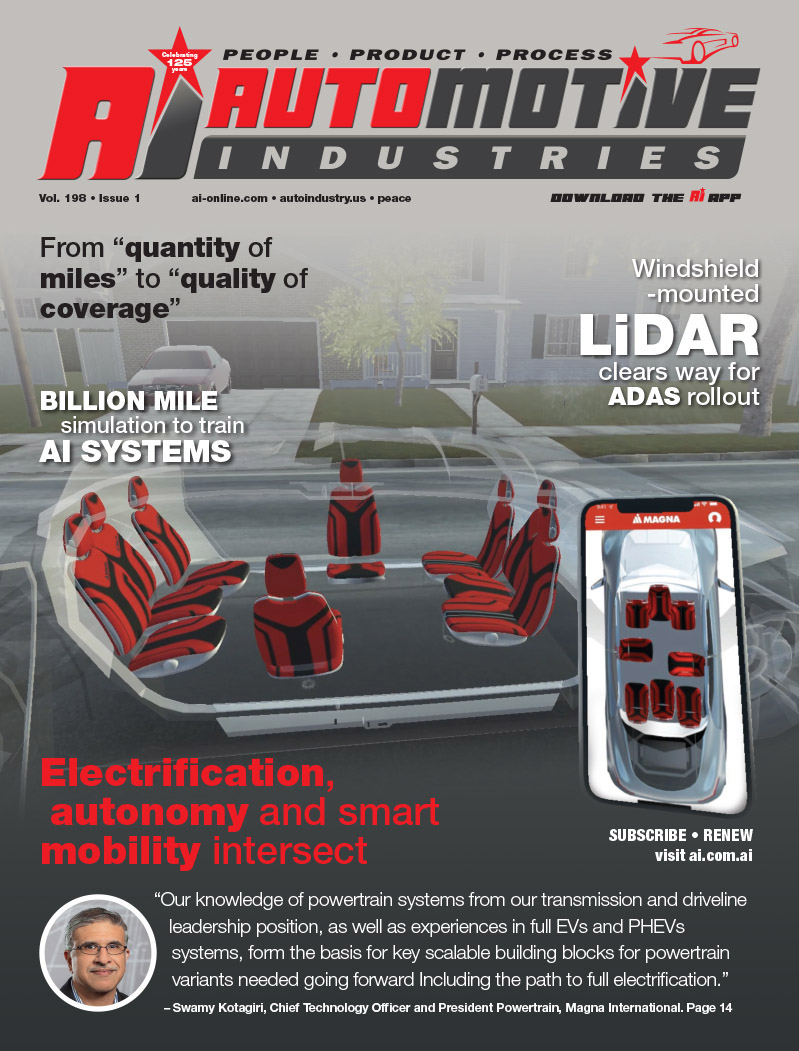
After years of focusing on reducing the weight of chassis frames, weight reductions are expected to come from above the ‘waistline’ components that improve driving behaviour and driving stability. In particular, glass panes are expected to be replaced by polycarbonate panes allowing a significant weight reduction, Dr Knuth Schmidt, chief operating officer of Dynamit Nobel Kunsstoff GmbH tells Nick Palmen of Automotive Industries.
Additional applications such as pedestrian safety systems are regarded as key success factors for future growth.
Dynamit Nobel Kunststoff GmbH is a leading European manufacturer of thermoplastic and thermosetting exterior plastics mainly for the automotive industry.
The company consists of two Strategic Business Units (SBUs) ‘Thermoplastics’ and ‘Thermosets’. DNK is the holding company of the two SBUs and the main operating legal entity of the SBU Thermoplastics. The operating activities of Thermoplastics are conducted through DNK, headquartered in Weiߥnburg, Bavaria. DNK has subsidiaries located in Spain, France and Argentina.
Thermoplastics can be found in vehicle body exterior parts, dashboards for commercial vehicles, front-end carriers (hybrid technology, combining steel and plastic parts) and safety devices such as airbag housings. Thermoplastics also designs and develops the tooling required for the injection moulding manufacturing process.
The production process of thermoplastic parts for exterior and interior applications comprises three main steps: injection moulding, painting and assembly. The processing of all thermoplastics in RRIM (Reinforced Reaction Injection Moulding) technology allow a wide product range to be offered. The most diverse fabrication processes in injection moulding machines with a clamping force of up to 54.000 kN allow a high flexibility and diversity.
Painting is a key competence and value-added process, says Schmidt. Due to the OEMs – demand for the highest quality ‘Class A’ products, both the quality of the surface coating of manufactured plastic parts and the colour matching are critical in the production process, he says.
AI: What are the trends in the use of thermoplastics and in particular new materials & processes in terms of lower part weight and increasing overall functionality?
Schmidt: The automotive industry accounts for approximately 7% of European plastic consumption by weight. In Europe the average plastics content per passenger car was approximately 100 kg in 1990 and is expected to rise to 150kg by 2006.
The trends in the use of thermoplastics and the key drivers of the growth of plastics in automotive applications are among other things:
– Reduction of weight and fuel consumption based on the rising usage of hybrid solutions (which increase comfort at low cost) in addition to substitution of other materials and the development of lightweight applications
– Integration ability since plastics are easily combined and integrated with other materials (inserts). Further on modularisation will help to reduce the number of components and suppliers, and contribute to further optimise car assembly cycle times
– Increased safety: weight reductions that have taken place in cars below the centre of gravity (e.g. suspension and transmission components) and the trend for taller vehicles, such as vans and Special Purpose Vehicles have moved the average centre of gravity higher, which has resulted in reduced ride and handling stability.
– New applications in alternative materials such as sun roofs, transparent all-plastic roofs and glazing will be important as they will lower the centre of gravity
AI: Where do you see the biggest growth potential for the company?
Schmidt: DNK is positioned ideally to benefit from the rising share of plastics in automotive applications as a result of the continuous substitution of other materials (e.g., steel, aluminium and glass). This effect is driven by the growing importance of weight savings and increasing complexity of parts within the car design, as well as from increasing upstream capture due to increasing outsourcing by the OEMs.
AI: costs and a competitive product with higher quality. How do you cope with these tasks?
Schmidt: Thermoplastics has established a sophisticated IT-based quality management system that ensures high output quality and constantly monitors production performance. Performance and product quality measurements include ‘RPPM’ (rejected parts per million – parts rejected by customers), ‘IPPM’ (internal parts per million – internal rejects and rectifications) and ‘PPM’ (parts per million – the ratio of rejected vs. total supplied parts per million). Proximity to OEMs is another essential factor in the automotive supplier industry. In addition to -Just-in-Time- (JIT) delivery, JIS delivery is becoming increasingly important to meet today’s production philosophy of the automotive OEMs. In order to ensure the stability of the process, Thermoplastics operates a highly complex, IT-supported system of material and information flows, inventory and asset management, customer relationship management systems and performance measurements.
Further on DNK has implemented an integrated cost management system that covers both the sales side and the production side. Therefore different methods are applied e.g. to optimise the efficiency of our production systems or for the analysis of products already in series production. All methods are centralised in a separate function that copes with the customer-driven cost reduction programs. The purchasing department bundles the quantities of the whole SBA to enable better conditions and better prices. An active risk management system minimizes insolvency problems with suppliers. Further the continuous contact during quality meetings, audits, value analysis projects and project meetings ensures a high quality level and competitive prices.
AI: DNK has long-standing customer relationship with all major German OEMs. What are the benefits that your cost management process brings to the customer?
Schmidt: Allocating the knowledge of our cost improvement efforts and implementing it in the development of future programs enables us to offer best-in-class design-to-cost to our customers. Combined with our innovation management system we are able to integrate new ideas and well established methods together in a new product. Being a technological leader among the OEM’s suppliers, our customers can rely on our expertise and efficiency and focus on their core competencies. Responsibility for development also results in a professional cost management and cost structure. Therefore we continuously try to improve our methods.
AI: Congratulations on your Volkswagen Group Award 2005! What were the main factors contributing to this excellent achievement?
Schmidt: Our company, more precisely our plant in St. Andreu Barca (Barcelona/Spain), got the Group Award in the category product quality. DNK could convince by its excellent quality capabilities for the production process as well as by the quality performance with regard to series-production supply.
More Stories
Dürr and GROB concept battery factory uses 50% less production space
DuPont materials science advances next generation of EV batteries at The Battery Show
How Modern Power Management Enhances Connected Fleet Tech