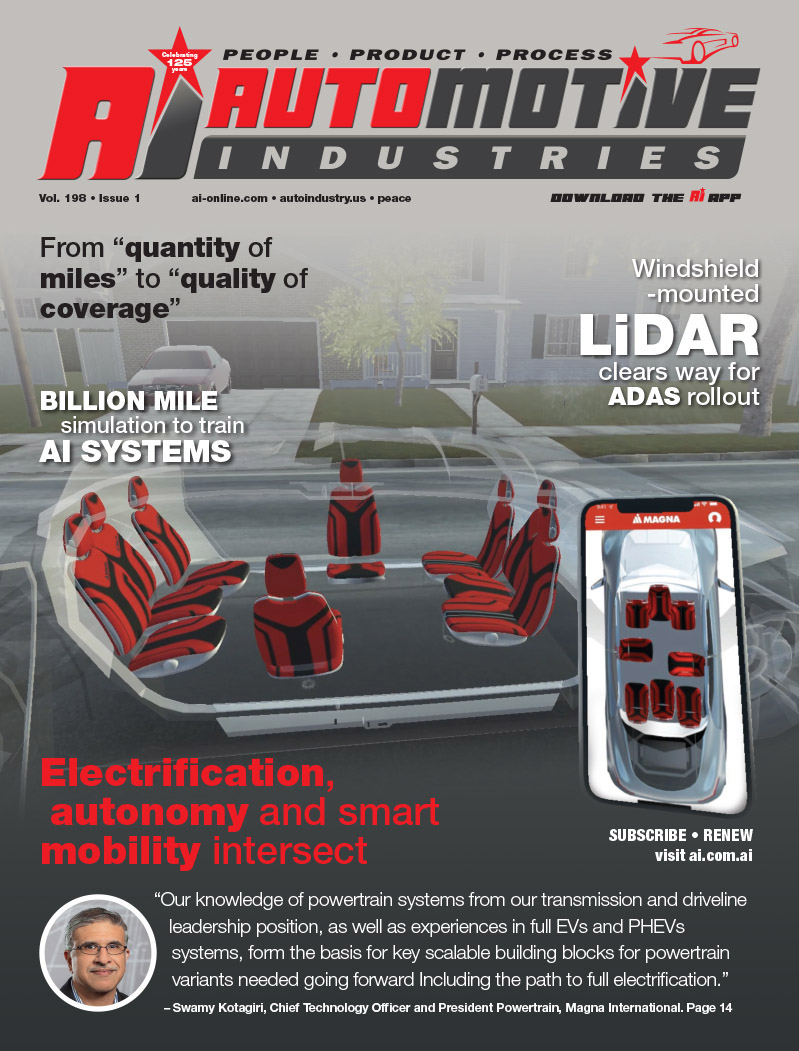
South Africa’s once troubled political and economic history has seen the development of a “can do” business culture.
During a period of international sanctions during the 1980’s and 1990’s component suppliers had to learn how to keep costs to a minimum and to improvise with what they had while still delivering quality products to the country’s auto industry. That tradition remains, although the manufacturing equipment has been modernised. “We are still innovative with raw materials,” says Jake van der Kolk, managing director of Gauteng-based Fine Blanking.
The company, which for 30 years was the only one of its type in South Africa, specialises in the production of precision conventional and fine blanked quality metal pressings, together with component machining for the automotive, electrical and various associated industries, supported by in-house tool design and engineering facilities. According to van der Kolk, it pioneered and adapted the fine-blanking processes to South African conditions and raw materials. Strong commercial and technical relationships with the local steel mills have contributed to its ability to deliver.
Fine Blanking has more than 40 industrial customers within South Africa of which have established first tier automotive operations in South Africa and is gaining recognition in the USA and in the EU.
Fine Blanking has a well-established logistics network, providing on-time delivery to customers in Gauteng, Cape Town, Port Elizabeth, and Durban, which are the main industrial areas in South Africa. Cape Town and Port Elizabeth are over 1,100 kilometres from the Fine Blanking plant in Gauteng. The primary target market is the growing automotive industry representing over six per cent of South Africa’s gross domestic product (GDP). This figure is projected to increase in future, fuelled by a growing domestic market, continued surge in vehicle and components exports and large automotive manufacturers investing in South Africa. The automotive industry represents the third largest sector in the SA, after mining and agriculture, and accounts for approximately 29 per cent of South Africa’s manufacturing output. Fine Blanking’s secondary target market is spread across the mining, electrical, armaments and the security industry for which specialised metal pressings are needed. “Each segment of the market wants to procure quality products at reasonable prices. Fine Blanking is in the position to offer just that to our clientele, and we understand that our products must assist our clients to better add value to their own end customers,” he says.
A dramatic strengthening of the local currency, the rand, saw Fine Blanking losing some export contracts over the past two years. However, “contracts lost to the EU in 2003/2004 due to the strong Rand are now being re-awarded to Fine Blanking due to quality and shorter supply chains,” says van der Kolk. Fine Blanking is able to compete in the European and US markets because of its flexibility and its approach of working with clients to find solutions to material and manufacturing challenges. “One of our strengths is that we are used to producing lower volumes cost-effectively. Our tooling costs are much less than those elsewhere, which helps us to be competitive,” he says.
Technical skills developed during the sanctions period have since been honed, and are helping South African-based assembly operations to reduce costs. “It is not always viable to import components. That is where we work with the OEM to see what equivalent materials are available, or to find other ways of doing the job,” he says. In-house quality controls ensure that the work produced by Fine Blanking meets international quality standards.
Fine Blanking’s equipment includes nine fine-blanking presses, eight eccentric presses, two CNC machining centres, two CNC turning centres, six auto lathes, three de-burring linishers, a robot welder station, a fully equipped tool room and a host of secondary operation and transport equipment. It has the capacity to double its output in order to meet new orders.
Greater stability in the country’s political, social, economic and labour sectors is also helping to position South African-based manufacturers as preferred suppliers. “Strong commitments to exporting and sustained expansion of the South African economy are key elements in the metalworking industry’s newfound stability.” Export successes and the world’s fastest-growing domestic market have added stability to the local automotive sector. “The automotive industry is changing, which is important. It is far less cyclical than it was in the past. Automakers are undertaking more frequent and less extensive design changes and becoming more global, tailoring their products to individual markets. This has led to ongoing investment programmes rather than concentrated purchasing cycles. The increasing globalisation of the automotive sector is encouraging a similar trend among metalworking companies. South African companies are increasing their worldwide presence, often through joint ventures, cooperative agreements, and strategic alliances.”
Within this context, “Fine Blanking’s strength and profitability stems from its rigid adherence to manufacturing products that can be supported through taking systematic advantage of the knowledge obtained and achieving continuous improvement of fine blanking tools and processes. Maintaining a technical team through a high level of competent individuals with many years of experience in fine blanking who form and maintain relationships with our customers. The Company’s basic philosophy is to profitably meet the needs of discriminating customers by providing a quality product, meticulous personal service, and total customer satisfaction,” he says.
More Stories
What You Need to Know About Tire Pressure in Winter vs Summer
Essential Features to Look for in ADAS Calibration Systems
Your Guide to Filing a Car Accident Claim