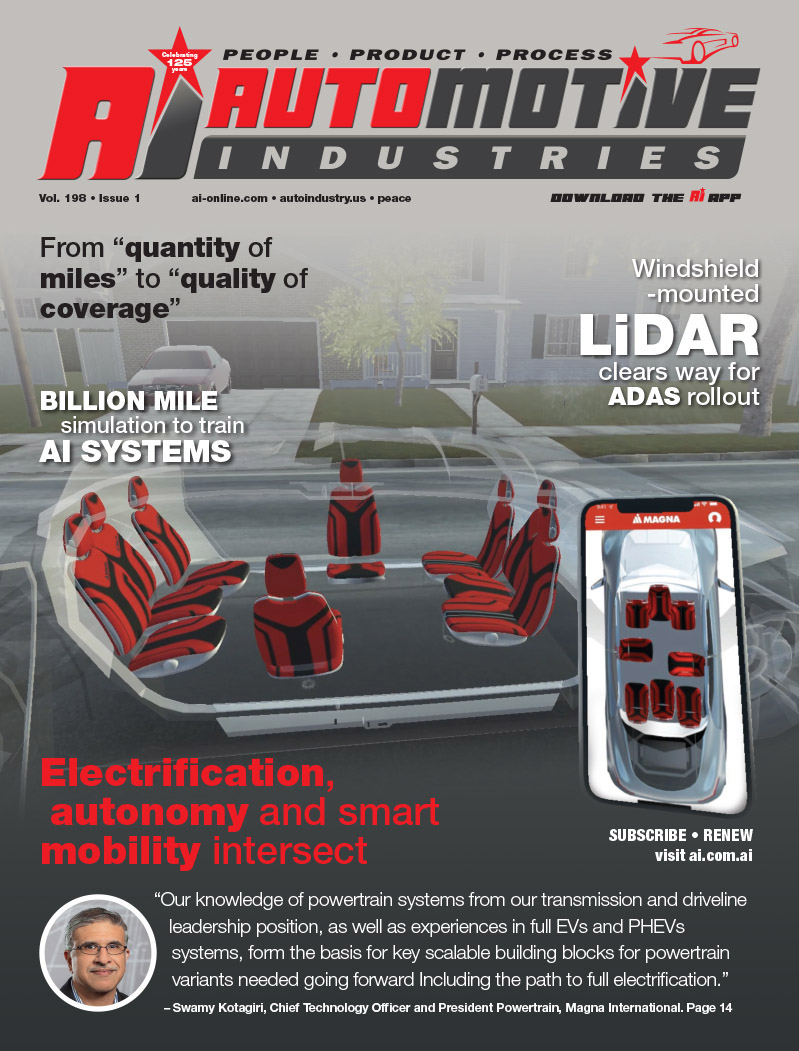
Increased consumption of wollastonite is being driven by the motor industry. According to Nordkalk, one of the pioneers in the mining and use of the material, the consumption of wollastonite in the plastics compounding has increased significantly within the last ten years. At present, the mineral is expected to see growth rates of approximately 5 to 10 percent each year within this industry.
Marketing Manager Hannu Venäläinen of Nordkalk discusses the uses of the mineral.
Automotive Industries (AI): What are the potential uses of wollastonite?
Venäläinen: The most common end use for wollastonite is found in plastics for the automotive, electrical and whiteware industries. The typical end use is Nylon 6 & 6,6 compounds, but wollastonite is also used in polypropylene, epoxies, polyurethane (RRIM) and polycarbonate etc. Some grades can also be used in special elastomers.
AI: What advantages does it offer to manufacturers over more conventional materials?
Venäläinen: Compared to common mineral fillers (e.g. talc, calcium carbonate, kaolin etc.), the main advantages are found in scratch and mar resistance, dimensional stability, stiffness, shrinkage and impact resistance of the filled compound. Compared to chopped glass or glass fibre the main advantage is the lower cost of the filler. In addition, advantages in the processability, the surface appearance and paintability of the compounds are found. Wollastonite also reduces the wear on the processing equipment compared to chopped glass.
AI: What are the reserves of the material?
Venäläinen: With the current production level, the exploitation of the deposit in Lappeenranta (wollastonite and limestone) is expected to continue at least for another 100 years.
AI: Is it suitable for recycling?
Venäläinen: As wollastonite is a natural mineral, compounds containing wollastonite can be recycled. Wollastonite has a status of being a harmless mineral. When considering thermoplastic, the compounds can be used and moulded again. The needle shape structure of the particles may however experience minor damage. This, together with the partial destruction of the polymer matrix, may lead to minor losses in the technical properties of the recycled compound.
AI: What technological back-up is there for the material?
Venäläinen: Nordkalk tends to work very closely with the customers, providing them all the support needed to achieve the wanted properties that are possible for their applications. We also keep the customers informed about the new developments and new possibilities. A large part of our export sales for the plastics industry are handled through distributors who are experts in the applications that they are serving with our products. So one could say that local support is available for our customers both home and abroad.
Nordkalk also co-operates closely together with the universities and institutions linked to the plastics industry within our R&D activities.
AI: What logistical structures are in place to get the raw material to potential users?
Venäläinen: During the last 30 years Nordkalk has built an effective logistic network with our transportation partners. Nordkalk offers a full range of packaging options from 20 kg paper bags to 1200 kg big bags. Material is of course also available in bulk, but the wollastonite used in plastics is mainly packed material.
AI: How do its costs compare with conventional plastics and metals?
Venäläinen: Generally, the filler is cheaper than the polymers that it is used in. For example in Nylon compounds the difference of the prices between filler and the resin are quite high, but when we come down to more commodity grades, the difference is lower. But it is also an issue for selecting the most cost/performance favourable grade for each application. At the moment Nordkalk is developing new high aspect ratio grades, which are designed mainly for PP compounds.
More Stories
Your Guide to Filing a Car Accident Claim
Steps to Take Immediately After a Car Accident
What Makes SUV Cars More Prone to Accidents?