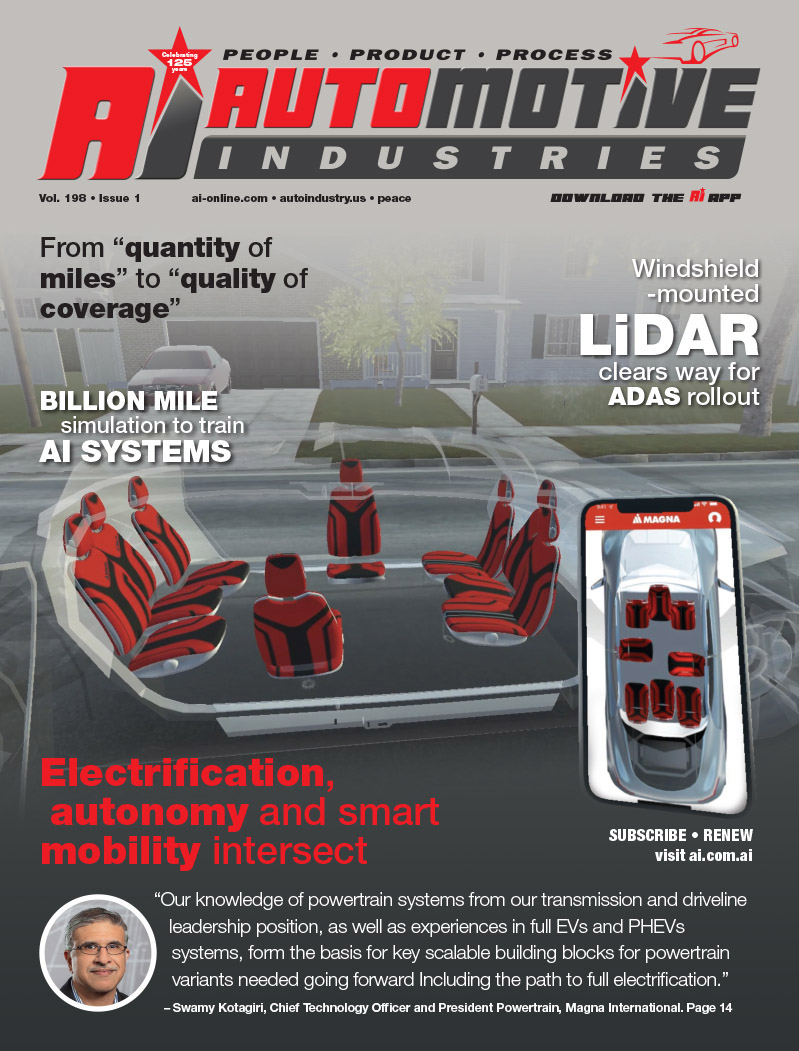
Automotive lighting designers are almost unanimous in their key expectations for the resins they specify for use in forward lighting applications — headlamp bezels and reflectors, fog- lamp reflectors, and park-and-turn reflectors. They demand materials that exhibit excellent surface appearance, high temperature resistance, excellent impact properties, and high flow rates.
Responding to the needs of this global market, Solvay Advanced Polymers, L.L.C. has introduced two new grades of amorphous materials that have been developed specifically for automotive lighting applications. RADEL(R) LTG- 3000 polyethersulfone (PES) and UDEL(R) LTG-2000 polysulfone (PSU) materials are designed to outperform conventional polyetherimide (PEI) resins and high- heat polycarbonate/PEI blends in these key performance criteria. Both new products are capable of direct metallization, which can eliminate secondary production operations and reduce the system cost of a lighting component.
RADEL(R) LTG-3000 PES – optimized for automotive lighting
In any reflector in a directional lighting application, the quality of the surface is paramount. These new grades have been formulated to optimize both surface quality and functional requirements such as thermal resistance, impact, and flow. These products have shown to be excellent materials for these critical and demanding lighting applications.
Performance and processing advantages
Designed for use at temperatures up to 205 degrees C, RADEL LTG-3000 PES delivers higher temperature resistance, greater impact resistance, and higher melt-flow rates than grades of PEI traditionally used in lighting applications. This new lighting grade of polyethersulfone also demonstrates a 50% improvement in impact resistance over conventional PEI products, with a 33% increase in flow.
“This increase in flow allows engineers to reduce wallstock by at least 25% while maintaining toughness,” says Matt Howlett, Global Market Manager for lighting materials at Solvay Advanced Polymers. “This represents a real possibility for substantial cost savings while maintaining part integrity. The first time you put the LTG materials in a tool, you’ll appreciate the difference — pressures will drop, material will flow better, and you’ll fill out the part with less molded-in stress.”
UDEL(R) LTG-2000 polysulfone replaces high-temperature PC and PC/PEI blends
UDEL LTG-2000 polysulfone is designed to provide an excellent surface appearance at temperatures up to 175 degrees C. Materials traditionally specified for this temperature range have been high-temperature polycarbonate (PC) and PC/PEI blends. Compared with these materials, UDEL LTG-2000 PSU exhibits greater temperature resistance than most commercially available high- temperature polycarbonates and PC/PEI blends.
The new lighting-grade polysulfone also has significantly higher flow rates than these competitors. “It’s a very high-flow product,” Howlett points out, “even higher than the new RADEL material. In addition to its surface appearance and thermal properties, this product offers excellent impact resistance, so it’s more durable than other medium-heat materials used in this segment. Many of the more traditional high-temperature polycarbonate products are plagued by poor flow. UDEL LTG-2000 polysulfone has high heat and high flow. The best of both worlds.”
UDEL LTG-2000 polysulfone is also designed to be directly metallized for use in applications such as reflectors and bezels for headlamps, fog lamps, and park-and-turn lamps.
Long-term commitment to this market
Focusing material expertise and manufacturing technology directly onto the needs of the lighting market are tangible evidence of the commitment Solvay Advanced Polymers has made to the automotive lighting market. Longer term, the company has invested $50 million in expanding its Marietta, Ohio, plant. This will greatly increase the company’s capacity to produce sulfone-based resins. The expansion keeps pace with increased demand in the global lighting marketplace, and it indicates the company’s intention to supply these materials on a global basis.
More Stories
Dürr and GROB concept battery factory uses 50% less production space
DuPont materials science advances next generation of EV batteries at The Battery Show
Cybord warns of dangers of the stability illusion