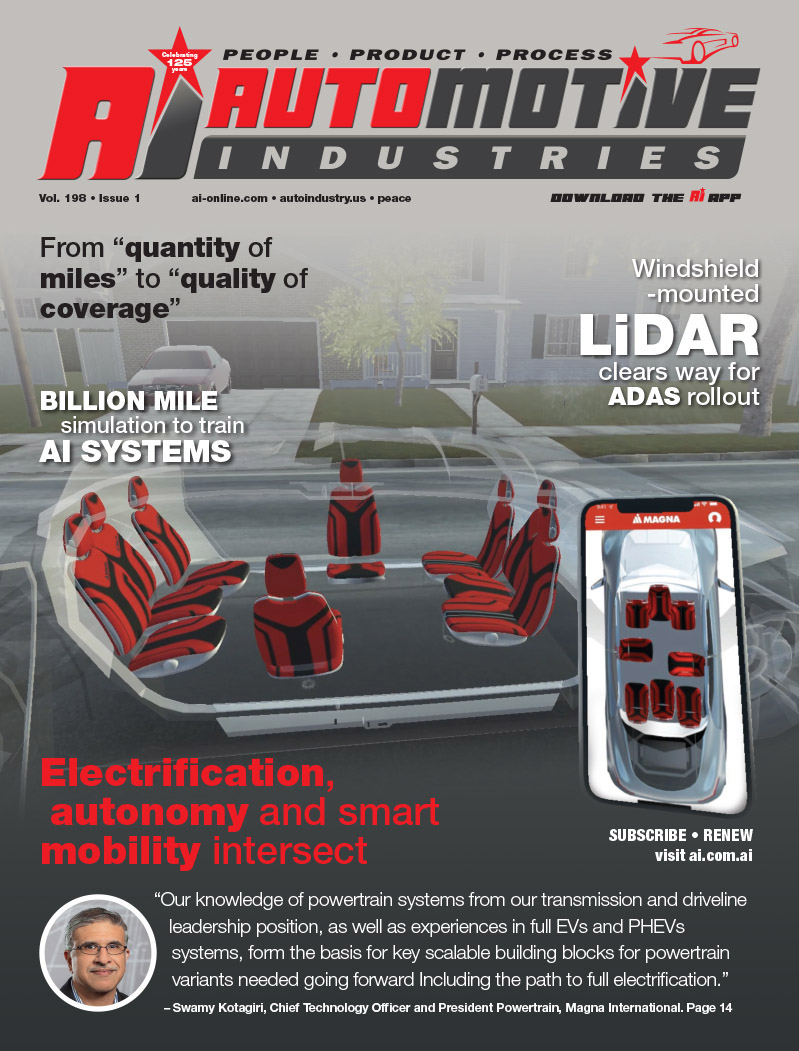
“Lead, follow or get out of the way.” Lee Iaccoca’s words as head of Chrysler Corporation never proved truer in machining and manufacturing than they do today. In order to be efficient, effective, and competitive, leading organizations must be innovative.
Experience in machining is both valuable and necessary. Experience, though, is best used as an evaluator of the new and not merely an insistence on the tried and true. New technologies in machining occur almost daily – through-the-tool coolant, high pressure coolant, and high speed machining techniques are all innovations that are quickly becoming mainstream.
So what’s next? Who will take the risk?
You? You’d better.
Case in Point:
Once just a military and space systems material, titanium usage is now expanding considerably. It’s showing up in everything from golf clubs and automobiles to cell phones and hip replacements. Still, machining titanium continues to be an issue for many organizations. The material properties of titanium dictate that plastic flow necessary for chip formation in machining is not initiated until significantly elevated temperatures are reached. Conventional tools HSS, Carbide, and Coated Carbide all suffer under temperature loads that high. Forces are high, tool life is low, tool wear is fast, and processing times are both long and costly.
One aerospace supplier had a titanium part that was particularly troublesome Process times were long (over twenty hours per part) and material costs were high because the organization used excess material to dissipate heat and reduce warping generated during processing.
The Key to Success:
Our expert research at the supplier’s facility and verified through tool-life testing in the Dr. M. Eugene Merchant machining TechSolve Labs in Cincinnati proved that tooling choices played a major role in the development of a best practice for machining titanium. The research and testing also discovered coolant application techniques and the use of five-axis machining to slightly tilt the cutting tool (approximately one degree off vertical) into the material provided the optimum process.
The tooling used was a 10 flute coated (TiAlON) Solid Carbide End Mill. The number of flutes was critical to success because they reduced the chip load per tooth and provided an overall increase in feed per revolution at the same time. This simultaneously reduced forces and increased metal removal rate, while generating less heat. High pressure coolant forced metal working fluid into the cut zone – additionally cooling the process. The one degree of tilt on the tool allowed the coolant easier access and disengaged the cutting edge from the cut, which further enabled the cooling process.
The combination of faster, low force cuts (the basic science behind High Speed Machining techniques) and better, more effective thermal management of the process provided a significantly more efficient machining process. Material requirements were reduced by one third because the requirement to guard against warp was reduced along with the extra material needed to “sneak up” on the finished geometry. Only two cuts were required, a rough cut and then a finish cut. This shaved the processing time down to one-half of the original process. It was no longer necessary to “sneak up” and the process parameters yielded much higher metal removal rates. Quality yield was also increased because the warp issues in the final part were not nearly as significant, leaving the geometry within tolerance.
The organization’s ultimate key to success was their willingness to change. There was risk involved. Innovation by its very nature involves risk. The experience of your people, though, can mitigate that risk through the optimal selection of possibilities. In order for them to do this, they must be exposed to what is new, great, and no pun intended, cutting-edge.
Leading with inventive tooling and processing will allow an organization to compete more profitably and effectively on a national and global scale. Either you lead with innovation in your machining processes or your competition will.
About Mike Gugger
Gugger’s experience has focused on the shop floor. Prior to returning to school for his engineering degree, Gugger gathered over ten years of machining experience. Assuming greater responsibility up to Group Leader in charge of set-ups, CNC program verification and training of shop floor personnel. After completing his undergraduate degree, Gugger combined his background and education and applied it to the field manufacturing engineering. His responsibilities have included CNC programming and software implementation; training of programmers and operators; tooling, fixturing and process development; capitol equipment justification, procurement and implementation; JIT and ISO9000; development of DNC and shop floor communications systems; and management
More recently, Gugger’s efforts have been directed toward product development, process development, teams/cellular manufacturing and Lean manufacturing. He has served as a manufacturing representative for product development, insuring that manufacturing issues were addressed in the design stages. His cellular implementation experience, including personnel issues, began in his first manufacturing engineering position and continued through his most recent position, prior to joining TechSolve.
Gugger’s capital equipment and process development projects totaled over a million dollars in the two years prior to joining TechSolve. Gugger is presently Manager of Special Projects with TechSolve. In addition to those responsibilities, he is in the field doing manufacturing assessments to assist companies with improving their operations. Gugger also is one of TechSolve’s primary trainers in machining and Lean seminars.
Gugger has also had over 25 published articles. Included in those are a monthly column contributed to Cutting Tool Engineering, feature articles and articles in peer reviewed journals. Gugger has also been an Adjunct Professor at the University of Dayton, instructing in CNC Machine Programming.
About TechSolve
TechSolve is a team of business experts and engineers who represent some of the best thinking in the world on how to make your organization more successful. Through a hands-on approach, TechSolve’s industry experts: implement lean and other productivity improvement and cost reduction projects at the enterprise and supply chain levels; support new product development and growth planning; and help program and product managers reduce the cost of high volume or low volume/high cost metallic engineered parts.
TechSolve has been around for more than 20 years, helping small to large companies around the globe identify and implement process changes that will make them more successful. We don’t just say what could be done. We don’t just train. We get in there and do it. Moreover, TechSolve doesn’t just claim results; it uses an independent third party surveyor to capture and validate its customers’ ROI. More information can be accessed at www.techsolve.org.
More Stories
What You Need to Know About Tire Pressure in Winter vs Summer
Essential Features to Look for in ADAS Calibration Systems
Your Guide to Filing a Car Accident Claim