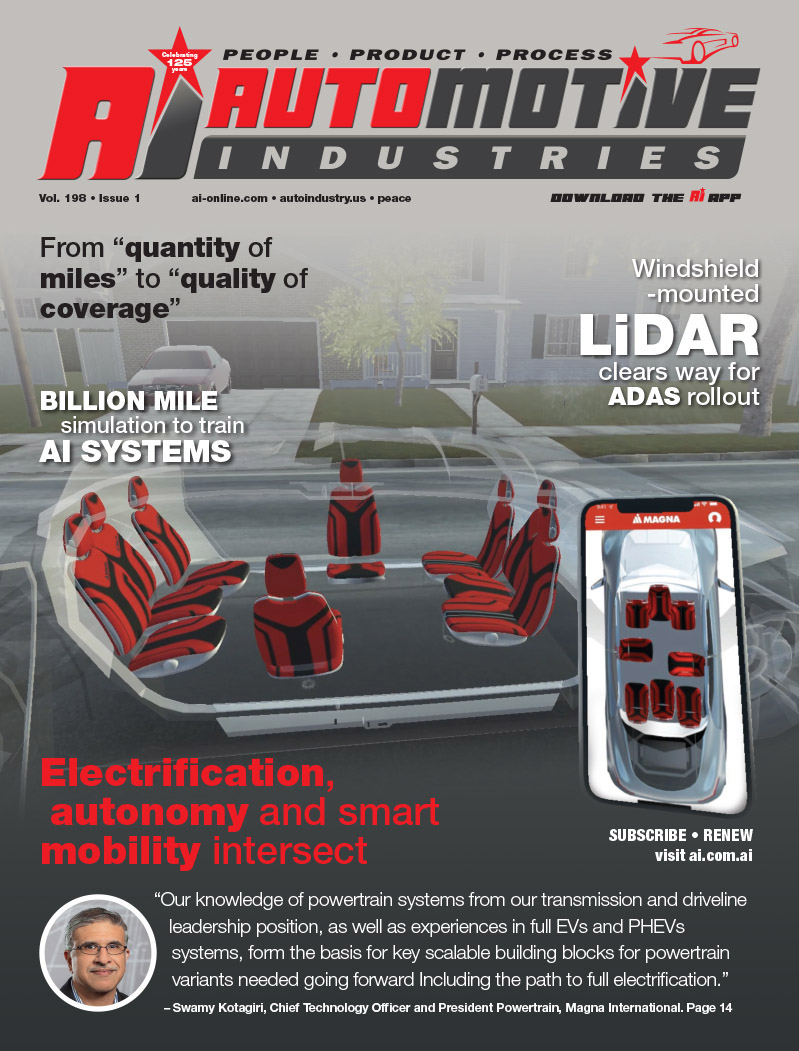
Behr America has developed an improved exhaust gas recirculation (EGR) cooler that adheres to the latest United States emissions standards for heavy trucks.
An EGR cooler is a device used on diesel engines that works in conjunction with the EGR system. The EGR cooler works by cooling the exhaust gases that go back into the engine through the intake manifold. The EGR system is used to reduce nitrous oxide (NOx) emissions. The EGR system lowers the amount of oxygen in the cylinder and the combustion temperature, thus reducing NOx.
“The EGR coolers being developed by Behr are designed to achieve double the recirculation rate and a much higher pressure level in comparison with the systems currently in use,” said Frank Mueller, Behr America president and CEO.
Due to 2004 U. S. emissions standards, vehicle manufacturers were required to reduce the level of NOx emissions by 38 percent. The tightening of emissions standards that began in 2007 has the goal to reduce NOx and particulate emissions by more than 90 percent by 2010. During this transition, 50 percent of vehicle engines sold must comply with the new regulations and all of them must be in compliance from 2010 and on.
Behr’s EGR cooler was redesigned to double the recirculation rate of cooled exhaust. The cooler will now have an increased power density, pressure strength and resistance to vibrations. For example, a 12-liter engine needs 120 kilowatts (kW) extracted from the exhaust gas in order to meet 2007 standards. This means that the Behr EGR cooler must have improved power density, robustness and durability.
Behr has developed a new management system – called the “House of Reliability (HoR)” – that keeps track of the reliability of the new EGR cooler. The HoR is based on seven elements: mission profile, failure management and weak-point analysis, virtual breakdown, component analysis, test strategy, field observation and validation.
More Stories
DuPont materials science advances next generation of EV batteries at The Battery Show
How Modern Power Management Enhances Connected Fleet Tech
Automotive Industries interviews Bahar Sadeghi, Technical Director, Car Connectivity Consortium (CCC)