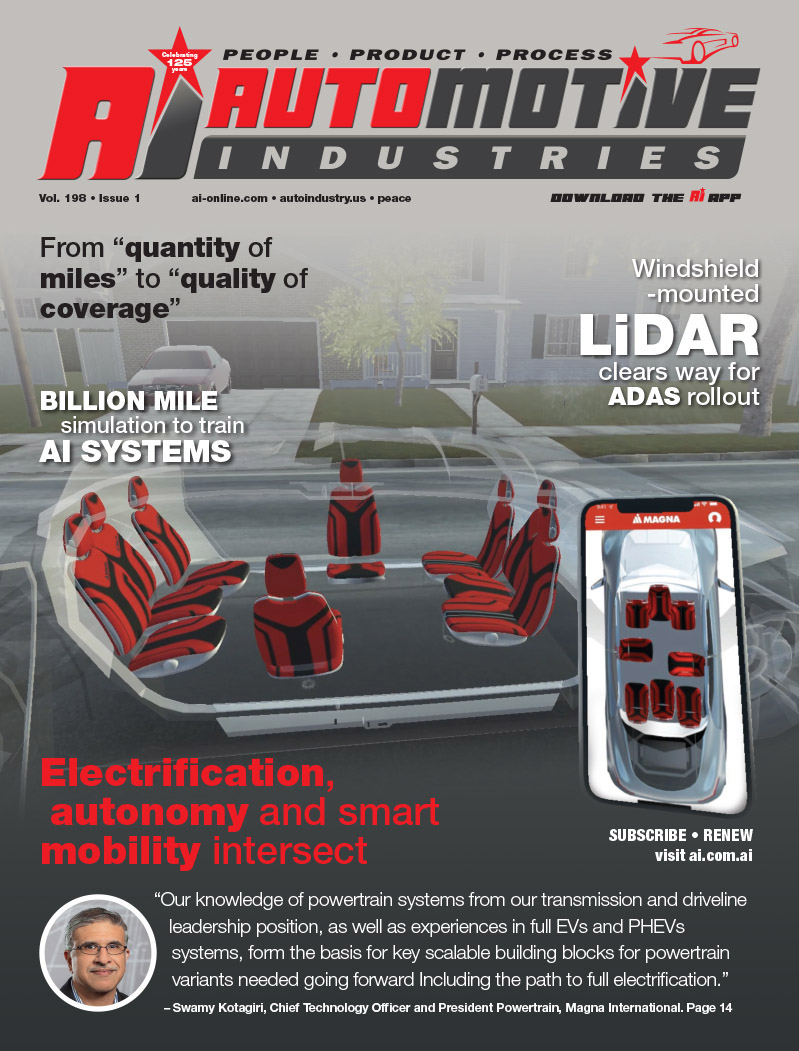
People have been trying to manufacture solid tires since the 1920’s, but the technology has only recently been perfected. “Amerityre believes that it has managed to surmount the problems faced by others, such as heaviness, lack of shock absorbency, tendency to wear out quickly and excessive absorption of moisture,†says Steinke.
“We set out to solve these problems. Our products are variable densities and consist of specially formulated polyurethanes creating a closed-cell foam construction which effectively reproduces the ride quality of a pneumatic tire. The closed-cell foam construction which forms one of the key components of our technology contains millions of closed-cells containing compressed air. Therefore our products are best identified as Flatfree in that they have no inner tube, do not require inflation and will never go flat even if they are punctured. Moreover the closed-cell infrastructure allows the tire to maintain its stability,†states Steinke. In 1996, the company first developed polyurethanes for foam tire applications. Amerityre closed-cell polyurethane foam technology is used to make Flatfree tires for bicycles, wheelchairs, lawn and garden, riding lawnmowers, golf cars and mopeds.
According to Craig Hooks, Sales and Marketing Manager, “independent tests validate the performance of the foam tires versus standard rubber tires in these categories. These tests include shock absorbency, weathering effects and durability. Amerityre’s tire outlast a standard rubber tire by more than two to one in most applications. This is great news because the market place for these foam tires represents more than 25% of the total tire market in the world.â€
The company started in 2003, when Steinke decided to develop an elastomer polymer compound to compete against rubber material to do auto and truck tires. In one year Richard Steinke, CEO and Manual Chacon, Head of Chemical development, invented a polymer for highway use. It was first tested as a retread on auto tires see if the polymer could withstand emergency stopping without flat spotting and also tested for wet/dry traction. According to Chacon, “the polymer made it through all the tests and so at the end of 2003 a tire mold was made in order to manufacture a complete tire out of urethane.â€
The research and development effort to produce a polyurethane auto tire with plies beads and belts culminated in April 2004 when Amerityre announced that FMVSS 109 testing had been successfully completed on the Amerityre’s “Arcus†polyurethane tire. “It is the first polyurethane tire to ever pass this test,†says Steinke.
“Not only did Amerityre’s urethane tire pass the test but the tires ran 114°F through the high speed test and 109°F through the endurance test with ambient temperature being 100°F for both tests. Also, the urethane tire had over 40% lower rolling resistance which equates to approximately 8% greater fuel efficiency. But, the key to success of the urethane tire will be the environmental issue. When discarded or burned, rubber tires are environmental hazards. Rubber products also start to break down as soon as they made. Amerityre does not use dry fillers or plasticizers because the chemistry of urethanes does not require a fusing of the polymer to cure. The natural chemical bond of polyols and isocyantes and the required additives such as catalysts, colorants, surfactants, and others are all reactive chemicals. These become the finished polymers,†says Chacon.
Non-Pneumatic Tires
In 2005, Amerityre developed auto tires had no air in them. “What was significant here was the test that had to be passed was identical to the air tire test requirements. At loads from 1,000 pounds to 2,000 pounds, Amerityre succeeded in passing tests required under FMVSS 129. To Amerityre’s knowledge no tire including a rubber tire has ever accomplished this feat. Passing these tests clearly shows the strengths of our polymers,†says Steinke.
Retreads
Several tire companies have asked Amerityre to do retreads for tractor/trailers and the large mining tires. The large mining tires are difficult to retread with rubber.
Amerityre is currently retreading truck tires for testing with four different tire companies.
Amerityre has also licensed Qingdao Qizhou Rubber Company in China to do truck retreads for the three largest size tires commonly used in mining operations. Qingdao is expecting to retread 10,000 tires a year. “The pouring machine is the largest pouring machine ever built. It can pour over 2,500 pounds of urethane in a minute,†says Steinke.
Tire Fill-Foam and Elastomer
Amerityre has developed tire fill for both light duty and heavy duty applications called “AmeriFillâ€. The foam fill is a light duty polyurethane closed-cell material which can be used in bicycle, wheelchair, and lawn and garden tires. This material is less than 1/2 the weight of our heavy duty fill. Elastothane or heavy duty fill is for industrial applications such a skid steer tires, mining tires, etc. Both tire fills are 100% environmentally safe in manufacturing and disposal, according to Steinke.
Technology available
Amerityre’s business strategy is to license the technology for manufacturing tires, sell the equipment package and then sell the chemical systems for the tire products. “We do not intend to be a tire manufacturer. That it not our strength. We are formulators, who understand the processing of urethanes. We intend to stay in that position. We will build a service department to support out clients and our technologies,†says Steinke.
“In the last several months, we have had many inquires from tire companies, urethane product manufactures, and entrepreneurs companies without urethane experience. But because of the simplicity of our manufacturing techniques, and the low capital equipment costings(one-tenth the cost of rubber), we feel the future will be very lucrative for Amerityre,†says Steinke.
Automotive Industries (AI) asked Steinke to talk about the potential for closed-cell polyurethane foam.
Steinke: Closed-Cell polyurethane foam tires have the potential of 25% of the whole tire market which means 500 million tires a year. This includes mopeds and motor scooters.
AI: Do you believe that the use of polyurethane in car tires or even a fully polyurethane tire will become a reality soon?
Steinke: Yes I do. It will be a total polyurethane tire. Tire companies are adding more synthetic rubber in their mix compounds today. The urethanes comes from the same basic chemical mixes. Therefore, the urethane tire will become a reality soon. Outside of the proper chemistry, manufacturing and equipment processing has been the problem. This has been addressed and the problems have been solved.
AI: What are some of the reasons the technology has not been absorbed by automotive tire companies?
Steinke: The manufacturing techniques were not discovered until recently. It took several years to invent the equipment package to handle the liquid phase technology. It had to be invented, built, fine tuned, and then file patents on the processing before one could show the tire companies. This has now been done. In the last two years we have filed over 20 patents covering equipment, processing, and tire designs.
AI: Your advisory board chairman Lee Iacocca is upbeat about the potential of PU tires – how has his endorsement helped?
Steinke: Mr. Lee Iacocca endorsement has helped because of his charisma and his integrity to the automotive industry. I do not put words into his mouth. He speaks what he believes.
AI: Who is likely to replace you as CEO of Amerityre?
Steinke: Dr. Gary N. Benninger will replace me as CEO on September 1, 2007. Dr. Benninger has worked with me the last two years and he is well qualified to take my place. He has years of experience in the manufacturing of polyurethane products. He is also well focused on implementing the company’s marketing program.
AI: What role do you plan on playing in the company after you step down on October 1st?
Steinke: I resign as CEO on September 1, 2007. I step down as Chairman of the Board on October 1, 2007. At that time I take on the duties as consultant to Amerityre on technology. I will spend my time fine tuning tire manufacturing techniques.
AI: What do you think the tire of the future will be like?
Steinke: Definitely the tire of the future will be polyurethane. It will be less costly to manufacture in capital equipment, energy, floor space, speed of production, and labor. But the monumental issue will be “Environmental.†Rubber is hazardous. Amerityre’s urethane chemistries are not hazardous, in fact they are inert.
AI: What makes you most proud when you look back on your stint as founder and CEO of Amerityre?
Steinke: What makes me most proud is that two people who truly believed and “never gave up†accomplished what many companies failed to do. I give a lot of credit to Manuel Chacon who trusted me and spent over 20 years on this technology. The last 10 years we perfected the polyurethane foam and the auto/truck tire elastomeric technology. Not bad for two people who lacked the technical education in science. Everything we learned and accomplished we did ourselves. Any man could do what we did if they are willing to pay the price of hard work and perseverance.
More Stories
Sonatus – The industry is shifting gears to software
Cybord warns of dangers of the stability illusion
How Modern Power Management Enhances Connected Fleet Tech