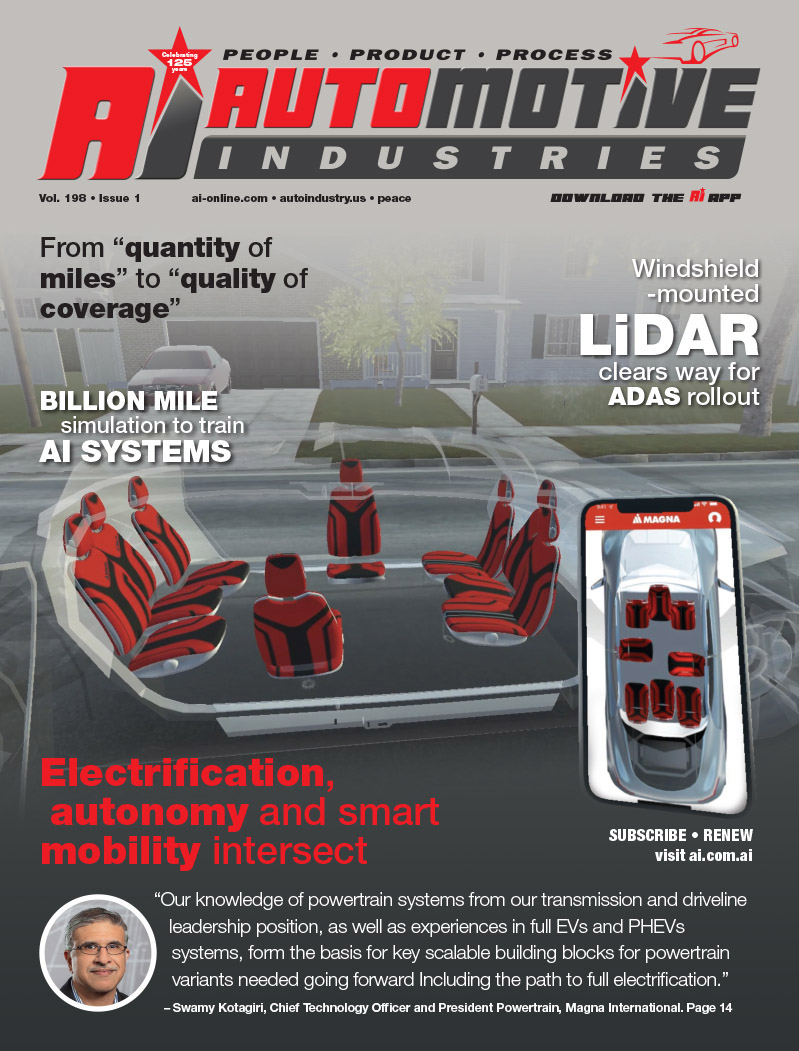
Hardly any other industry demands as high a level of cleanliness of components as the automotive industry does. Meanwhile cost pressure is increasing. Thus the challenge for the automotive sector and its suppliers, now more than ever, is to make maximum use of optimisation potential for the cleaning of parts, as a step in the production process.
The demand for higher performance, while simultaneously reducing weight, fuel consumption and the emission of pollutants, can only be fulfilled with components which match the most rigorous requirements and the most exacting tolerances. This is linked up to a higher degree of sensitivity of components to impurities. Any dirt not removed can lead to expensive rejects, laborious follow-up work, restrictions in functionality which damage a company’s image, right through to vehicle failure in service. To fulfil the challenging requirements of component cleanliness with maximum economic effectiveness, the optimum coordination of cleaning strategies is essential.
Introducing Greater Flexibility Into The Cleaning Of Individual Parts
Within the automotive industry and its suppliers, a large number of versions of equipment for engines and transmissions, as well as ever-shortening product life cycles, necessitate a high degree of flexibility. This means that production equipment and machines must be able to be re-equipped and adapted in order, for instance, to suit engines with less cubic capacity. The production of cylinder heads, crankcases and gearbox housings, for instance, entails the use of processing centres which can be re-programmed easily, thus enabling different versions of a workpiece to be produced. Frequently the parts, made in large production runs, are still cleaned in transfer units specifically arranged for a given component. Modern automatic cleaning solutions, using robots and integrated into the production line, offer a flexibility in the cleaning of parts which is appropriate to production needs. Integrated into the wet cell, the robot serves as the handling and processing system of the cleaning unit, precisely positioning the workpieces to guide them to the various treatments, such as spray cleaning, injection flood washing, high pressure burring and drying. Control is via a standard CNC system; the programming is via a user-friendly teach panel. This way, the unit’s operating personnel are in a position to program necessary adaptations to new or changed parts, rapidly and without problems.
CAPTION – The use of CO2 snow jet cleaning in the cleaning of plastic parts, such as fenders, mirror housings, offers economic and ecological benefits, compared to traditional wet cleaning systems. With a modular-based jet array, even complex geometries are reachable.
Image Courtesy of acp
These cleaning units, usually offered as standard modules, are compactly constructed; the media processing is integrated. Their space-saving mode of construction means that they take up much less production area than transfer units, while most of them also offer energy savings.
More Effective Batch Processes
Whether it is bulk material or products made in sets, wet chemical cleaning, using solvents or water-based cleaning agents in a batch process, is the procedure of choice for countless parts built into vehicles. The advantage of this type of cleaning is a high throughput in a relatively short time and, accordingly, a low proportion of the total manufacturing costs of a given workpiece. Frequently the cleaning process is carried out in central units. However there is no guarantee that the necessary degree of cleanliness is attained for all workpieces, in the case of simultaneously cleaning parts with different geometries, cleanliness requirements and/or levels of soiling (e.g. cooling lubricant and polish dust), as well as workpieces consisting of different materials. Thus for an optimum cleaning result, it is in most cases an advantage to carry out the cleaning process decentrally, in separate units, coordinated according to the spectrum of parts, the degree and type of soiling, as well as cleanliness requirements. In most cases this also leads to a significant reduction in the resources expended on logistics and handling, because the cleaning units can be placed close to the production of the respective part.
A cleaning receptacle in which the parts are well rinsed around by the cleaning medium from all sides is conducive to the process in all cases. This high level of accessibility also provides rewards in terms of the required drying time and lower level of carry-over of media, providing the opportunity of shorter cycle times or a higher throughput and longer bath usage times respectively.
Bath supervision and media processing
Bath supervision and media processing also make a substantial contribution to process-safe, economically efficient cleaning in the automotive sector. There is a variety of systems available for the continuous monitoring of the cleaning baths; these calculate the cleaning capacity presently available, in the process which is currently in progress; they either provide a consumption-dependent follow-up dosage automatically or they signal the need for a change of bath. New developments and product improvements in terms of filtration and processing systems open up opportunities for constantly higher separation rates and thus extended bath usage times.
Monitoring and documenting technical cleanliness
A continually growing quantity of components for the automotive sector requires the fulfilment of precisely defined stipulations regarding residual dirt. Due to the introduction of the ISO-DIS 16232 norm, Volumes 1 to 10, (VDA 19) ”Road vehicles
– Cleanliness of components of fluid circuits“, comprehensive standards were defined with regard to the approach and methods adopted for monitoring the cleanliness of particles. The objective of the directives is to be able to evaluate and compare the technical cleanliness of a component, by means of clear, unambiguously-described paths and procedures for obtaining and analysing particles.
For most of the relevant components, the proof of a particle’s properties cannot be provided directly on the product surface, simply due to their geometry. This necessitates a cleaning measure in which the particles are transferred into a fluid medium. The particles can be extracted from the component by means of spraying them away in a targeted manner, cleaning them off using ultrasound, rinsing them off and shaking the component. A second step is to count, measure and characterise the particles obtained. This involves the use of various procedures with varying degrees of usefulness in drawing conclusions: the gravimetric method enables conclusions to be drawn about the monitored components’ level of cleanliness, without giving information about the particles’ potential to cause damage. Manual analysis gives the opportunity to determine the sizes and distributions of particles (or, respectively, the largest particle) cleaned off the component – and thus to see whether the product conforms to certain specifications (e.g. no particle > 15 micrometers).
In addition, automated microscopy with image processing creates the opportunity for conclusions on the damage potential of individual particles. The raster electron microscope provides information on the size and distribution of the particles found, as well as the chemical elements they contain. This enables deductions to be made about the origin and the damage potential of the particles. A further alternative is fluid particle counters, working on the basis of so-called extinction particle counters. With these automated systems, the particles are cleaned off the component being checked, in an ultrasound bath; after this, fluid samples are assessed according to a defined program setting. The cleaning industry offers special checking systems in various sizes and versions for each of these procedures.
CAPTION – Standard cleaning units, with a robot completely integrated into the system; provide in the event of product changes or new components, the opportunity for rapid process adaptation, with low input of resources, thanks to reprogramming. Image Courtesy of
Cleaning the functional area in the production and assembly process
The selective cleaning of certain areas on the components, such as sealing areas, joining areas and adhesion areas, as well as laser weld areas, can lead to a huge saving in time and costs. This is because in these cases it is usually necessary to invest a great deal of time and cost to bring the whole component up to the degree of cleanliness needed for the functional area, using the classic water-based or solvent-based solution. Here cleaning is carried out on a production-integrated basis, using CO2 snow jet, laser or plasma procedures.
Thanks to the limited-area cleaning effect and the compact jets, the CO2 snow jet procedure is also suitable for integration into assembly units. Here screw insertion, caulking processes or contact with uptake from the workpiece can similarly give rise to functionally-critical particle dirt; up to now, little attention has been given to this issue.
Using alternative cleaning procedures to save costs
CO2 snow jet cleaning also offers advantages over traditional wet processes in terms of the cleaning of plastic assemblies, such as bumpers, mirror housings, prior to varnishing or coating. The cleaning process is dry, using environmentally-neutral, liquid carbon dioxide, accelerated by compressed air and jet-sprayed onto the component to be cleaned. This is also a targeted means of reaching areas which are difficult to access. Whether in the form of particles or film, any dirt present is removed (in what is a sparing manner in material terms) by using mechanical, thermal and chemical properties. On average, the investment costs for such a cleaning system are up to 50 percent below those for a conventional wet chemical system. The operating costs are up to 30 percent lower on average. This is due, not least, to there being no energy-intensive drying: the cleaning process is dry. The cleaning equipment can also be integrated directly into the varnishing booth, thus saving space.
The same also applies to plasma cleaning, for instance: a method offering a broad spectrum of application, thanks to the use of various reaction gases. This cleaning technology primarily comes into play in cases where later processes demand a very high level of degreasing. An additional effect of this procedure is a good preparation – for instance, simultaneous activation – of the surface for subsequent processes, including improvement of adhesion properties of adhesives and coatings. The plasma procedure is also suitable for applying coatings, e.g. corrosion-protection coatings.
Frequently a cleaning strategy that is coordinated to match requirements offers the opportunity to exploit optimisation potential within the entire production chain, thus structuring production more efficiently. Yet this can only be effected using knowledge of the way the various cleaning technologies perform and the best possible way of using them.
parts2clean 2009
What potential is offered for optimisation of time and costs by parts-cleaning in the automotive industry? Which processes can be used for the cleaning of different components in a process-safe, economically efficient manner? Answers to these questions, and lots of others concerning cleaning of parts in the automotive industry, are provided by parts2clean. The leading international trade fair for cleaning within the production process takes place from 20-22 October 2009, on the new trade fair site at Stuttgart Airport in Germany. The exhibition portfolio encompasses equipment units, procedures and process media for degreasing, cleaning, burring and pre-treating components, wire-mesh crates and workpiece carriers, handling and process automation, clean room technology, quality assurance, test methods and analytical procedures, cleaning media processing and disposal, contract cleaning, research and trade literature. In 2009 there will also be an international congress, for the first time, with the maxim ”Worldwide requirements, technologies and markets”. www.parts2clean.com
More Stories
Sonatus – The industry is shifting gears to software
Cybord warns of dangers of the stability illusion
HERE building trust in ADAS systems