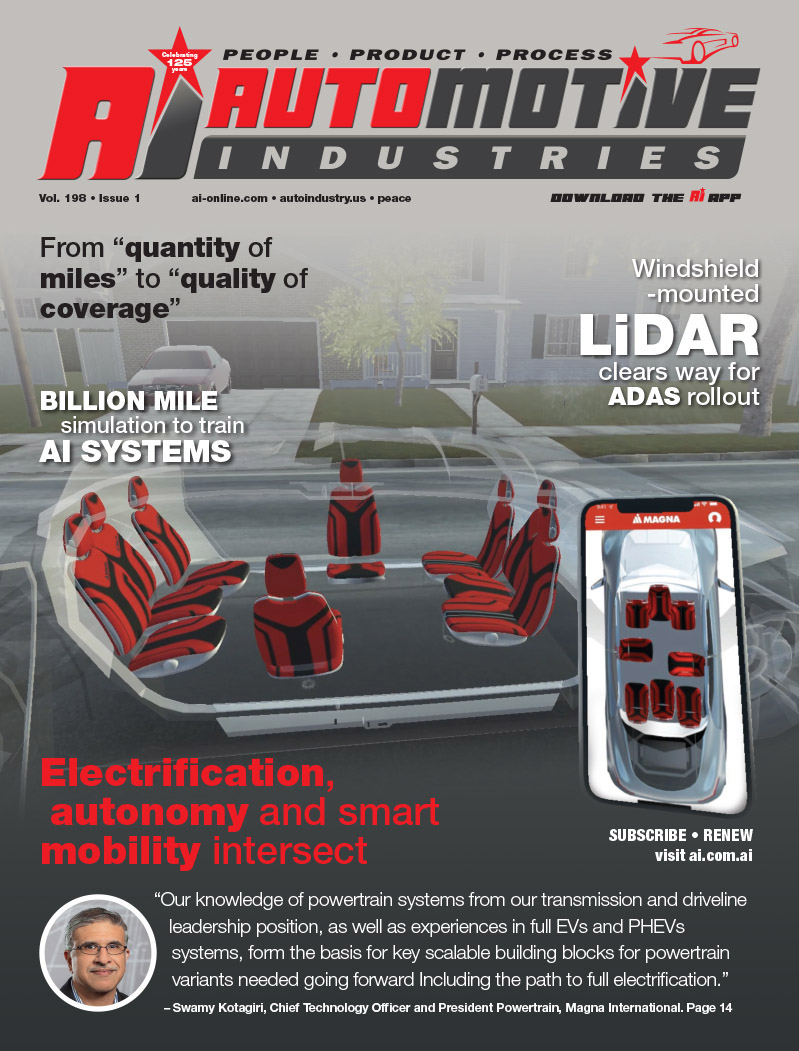
INTERVIEW – EFD Induction is Europe’s largest—and the world’s second largest—supplier of industrial induction heating solutions. The company was established in 1996 through the merger of Germany’s FDF with Norway’s ELVA. The former was a well-established induction hardening specialist. The latter, an agile newcomer that had pioneered the use of solid state technology to devise smaller, lighter, more flexible and more efficient induction systems.
The company’s heritage is important to CEO Eivin Jørgensen. “Absolutely,” says Jørgensen from EFD Induction’s corporate HQ in Norway. “Our focus from the very start has been crystal clear: harness this amazing technology called induction to create value for our customers. Of course, it’s easier said than done, but it’s this focus that drives us forward.”
The focus seems to have paid off. EFD Induction now has manufacturing facilities, subsidiaries and service offices worldwide. In the past year alone it opened its third center in China, as well as subsidiaries in Japan and Poland. Jorgensen explains the reason for the expansion: “Our customers are located all over the globe, which means we have to be too. For example, in the automotive industry we have customers in the Americas, throughout Europe, in India, and in China.”
EFD Induction solutions have been chosen by auto makers as diverse as BMW, Audi, Bentley, Ferrari, Ford, Volkswagen, Volvo, KIA, GM, Mitsubishi, Renault, Peugeot and Citroën. And by suppliers such as Bosch, GKN Drivetech, Delphi Automotive Systems, Visteon, Valeo, SKF and Raufoss. “But,” says Jørgensen, “what’s really important is what we do for these demanding customers, and that ranges from spot bonding to shaft and gear hardening, and from curing brake disc coatings to protective atmosphere brazing. In fact, whenever an automotive customer wants fast, efficient, reliable and controllable heat, the odds are we can devise a solution.”
We recently caught up with Jørgensen and asked him a few questions about his company’s, and induction heating’s, role in the automotive industry.
AI: Let’s discuss the economic downturn in the industry, as it’s something on everyone’s mind right now. How is EFD Induction responding?
Jørgensen: It’s at challenging times like this that customers really prioritize cost-control and productivity—especially if they can be achieved while simultaneously improving quality. And this is very much to our advantage. For example, we recently installed a brazing solution for a major diesel motor manufacturer in Finland. Now, lots of our competitors can deliver brazing equipment. But what we were able to do was build an automated in-line solution that removed an entire production step. The solution also uses copper alloy, rather than ten times more expensive silver alloy. This is an example of what I mentioned earlier—about our focus on creating value. And delivering even more value to our customers is how we’re responding to the crisis.
AI: EFD Induction often describes itself as the innovative induction heating company. Can you give us an example of this innovation benefitting the automotive industry?
Jørgensen: I could give you lots! But one that’s particularly relevant for the automotive industry is our ‘Package Hardening’ innovation for hardening closely spaced camshaft lobes. The method uses three different induction coils to simultaneously heat the inlet, outlet and injector lobes. Each coil is independent, with its own power supply. This means that the heating process can be adjusted to suit each lobe. Then there’s our patented Multi Frequency breakthrough that involves ‘blending’ two different frequencies into a single coil, or inductor. This helps ensure optimum heating results, particularly when hardening complex geometries such as gears. But I’d like to stress that EFD Induction combines innovation with the stability and resources one would expect from the world’s second-largest induction heating company. And this security—the knowledge that we have exceptionally well qualified staff from a range of disciplines, R&D labs, logistics systems, maintenance and training programs and a worldwide presence—is crucial for our automotive customers.
AI: Many of our readers probably associate induction heating primarily with hardening and brazing, at least in the automotive industry. How has EFD Induction created value for automotive customers outside these application areas?
Jørgensen: Well, to start with, there’s spot bonding—something that was actually invented by EFD Induction. Spot bonding is a fast, efficient way to join door and hood panels by heating only selected segments. Moreover, by ensuring precise energy inputs for each panel, our spot bonding systems minimize elongation. And with the launch of our patented U-Coil solution, we removed the need for clamps to maintain panel shapes and positions. Customers who’ve adopted these solutions report big savings due to less downtime and re-working. I should also mention the work we did with DACRAL, the protection coating specialists. That project involved drying and curing spray-applied Geomet® 360 brake disc coating. The list could go on…
AI: How do you see the relationship between induction heating and the automotive industry developing over the next decade?
Jørgensen: I’m no fortune teller, but I think it’s obvious that automotive customers will become even more insistent on innovation. Nobody these days can afford to do business with complacent suppliers. I think—and hope!—that automotive customers will seek out partners who are truly proactive, partners who never stop trying to rip out costs and improve quality. After all, auto makers will intensify their efforts to make lighter, cleaner and more fuel-efficient vehicles. Therefore, companies such as EFD Induction that can contribute to these efforts are well positioned for the future. For instance, EFD Induction has led the way in using induction together with lightweight materials such as aluminum, carbon fibers and composites. So we have a proven track record in overcoming tricky technical challenges—and coming up with practical solutions that can be integrated into automated production processes. The same process is at work with the new generation of hybrid, electric and bio-fuel engines. Auto makers are keen to work with partners who can optimize the mass production of these engines, and induction definitely has a key role to play. So whatever happens in the future, our task at EFD Induction remains essentially the same: to put the smarter heat to smarter use!
More Stories
Cybord warns of dangers of the stability illusion
Automotive Industries interviews Bahar Sadeghi, Technical Director, Car Connectivity Consortium (CCC)
Hexagon’s MAESTRO reinvents CMM systems through digitization