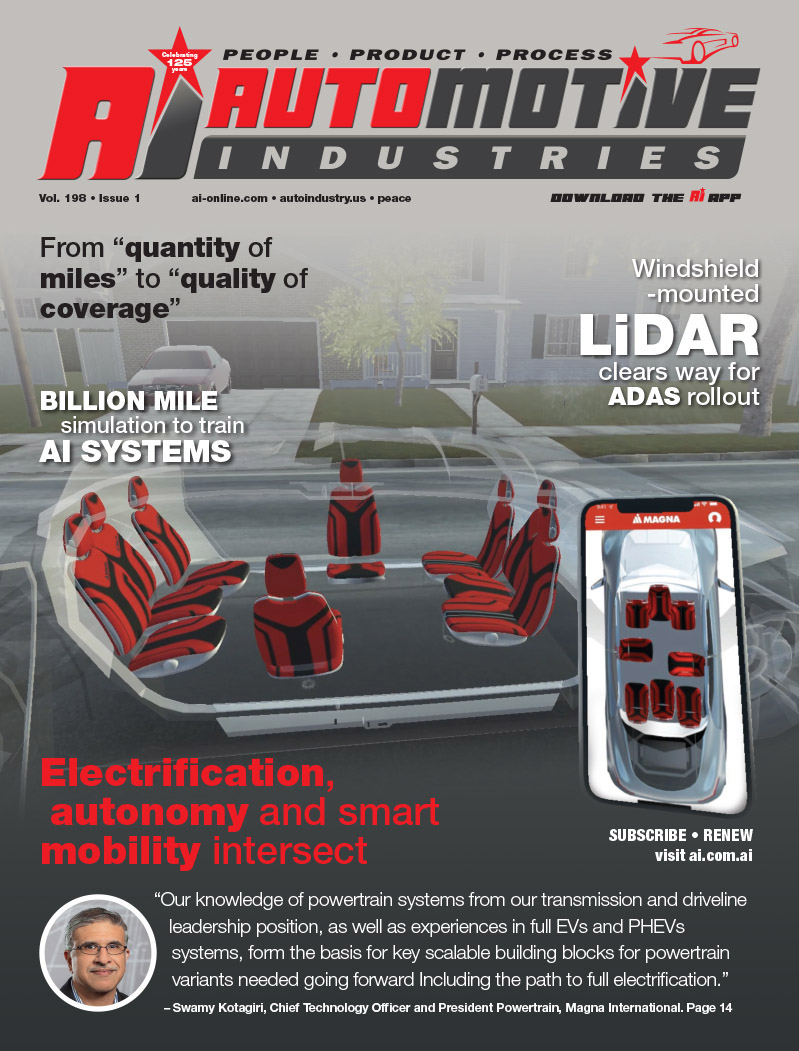
Motorsport wiring specialist BERU f1systems has developed a cost effective solution to allow 30 AWG lightweight wiring systems to be used in harsh environments. Developed in conjunction with Souriau, the new process doesn’t require special terminals or costly crimp tools, resulting in a wiring loom that is twelve percent lighter without the expensive component and tooling of competitor offerings.
“Working closely with an F1 team, we looked at how we could use 30 gauge wire to reduce weight whilst also considering the ever increasing cost restrictions that the teams have to comply with,” says principal engineer Gary Norman. “Other technologies are available but they require a tool that costs around £900, a specific 30 AWG wire that is four times the cost of our solution and they also need special terminals. These terminals also limit the range of connectors available resulting in weight or package compromises.”
BERU f1systems’ culture of improving all aspects of vehicle performance meant they were able to demonstrate that effective gains in loom reduction could benefit other areas of the car, without compromising reliability. “The twelve percent weight saving achieved will allow engineers to distribute weight more effectively, increasing vehicle performance or enhancing tyre wear,” claims Norman. “Testing demonstrated that our solution could withstand the SAE–39029 pull off tests, providing confidence. The team will use our solution on some of the harshest vibration applications on an F1 car.”
The firm has identified a set of components and assembly parameters and sequencing that allows the technicians to use standardised parts and assembly tools. This simplifies servicing and spare part stocking during the product’s life. Considering “whole life cost” is another area where an experienced integrator with design and manufacturing expertise such as BERU f1systems is providing additional value over simple component providers or distributors. “Many of the guys here have worked for race teams so they understand the importance of offering solutions that are simple to maintain and repair when you are far from the workshops,” says Norman.
The first applications are for F1 sensor wires, used for temperature and pressure senders around the chassis and powertrain. Sensor units are low power so can readily use the smaller gauge wires, however, BERU f1systems believes solving the cost of adopting 30 AWG could see the technology migrate to other areas of the car or onto lower formulae. “Having a solution that is both robust and cost effective will see the technology used where light weight and minimum size are the driving factors,” claims Norman.
About BERU f1systems
BERU f1systems offers advanced design and manufacturing facilities for vehicle wiring harness systems, tyre pressure monitoring, stress measurement and composites. Supplied to world championship winning cars in every major formula including Formula 1, components from BERU f1systems are now available in military, road car, aerospace and nautical applications.
More Stories
DuPont materials science advances next generation of EV batteries at The Battery Show
Cybord warns of dangers of the stability illusion
Avery Dennison PSA tapes support rapid evolution of EV batteries