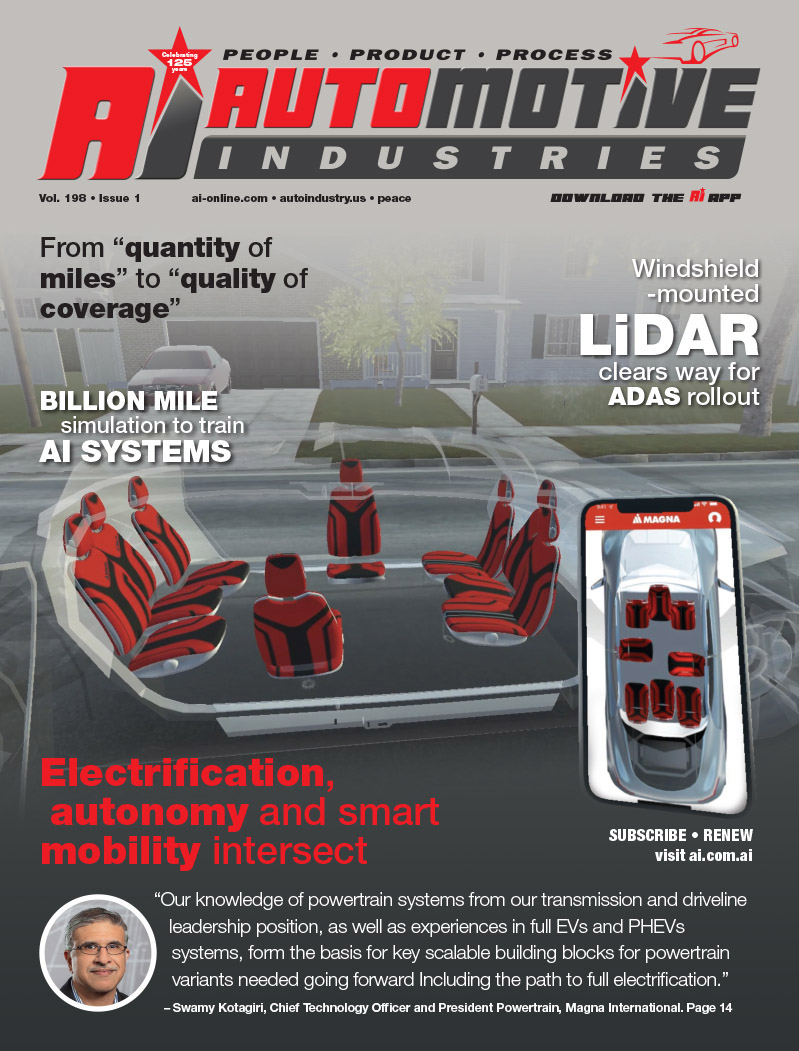
The Danish firm Haldor Topsoe has been manufacturing catalysts since the 1940’s. Its product range spans from catalysts to proprietary equipment, process design, engineering and service. Today it is on the cutting edge of some of the most exciting innovations in the transportation industry. In December 2009, Topsoe showcased its Topsoe Integrated Gasoline Synthesis or TIGAS at The Gas Technology Institute in Illinois where wood is converted into transportation fuel. With the TIGAS process, Topsoe is working on converting biomass including household waste, into fuel in the future. Topsoe received a USD 25 million grant from the US Department of Energy for the TIGAS project.
Haldor Topsoe has been at the forefront of the worldwide race to find alternatives to fossil fuel in transportation. Last year, the company started construction of a new bio fuel plant in Piteaa, Sweden that will be the world’s first to produce dimethyl ether – DME – from biomass. The plant is constructed as part of the EU project BioDME, coordinated by Swedish Volvo. In cooperation with Swedish Chemrec, Topsoe is designing and building the DME plant, which will produce DME from black liquor – a by-product of paper production which is normally burnt.
Topsoe is also part of a European Union initiative called the EuroBioRef (European multilevel integrated biorefinery design for sustainable biomass processing). This project, which has 15 partners, aims to uncover the entire process in the transformation of biomass from field to fuel and from plants to plastic. The project will create a virtual biorefinery researching all processes – from choosing the right crops to production of sustainable products from biomass. The project received Euro 23 million from the EU’s Seventh Framework Program. Topsoe’s contribution to the project is its expertise in downstream gasification technology and catalytic processes will contribute significantly to uncovering the transformation of biomass e.g. to acrylates.
Another project Topsoe is involved in includes turning bioethanol into diesel. Topsoe and the Danish Technological Institute received 1 million Euro from the Danish Energy Agency for this project. Diesel engines cannot run on bioethanol, because the cetane number is too low resulting in an inability to start the motor. The project goal is to uncover how bioethanol can be converted into diethyl ether using a catalytic process. The diethyl ether may subsequently be applied as diesel fuel.
“We expect to draw on our experience from diesel catalysis as well as industrial production of dimethyl ether,” says Pär Gabrielsson, Project Manager in Topsoe’s Research and Development.
Topsoe’s work with the transportation industry includes its automotive product portfolio which comprises a complete range of catalytic products for the automotive industry. The company offers integrated catalytic solutions including substrates, catalysts and sleeving, offering clients single point responsibility and collaboration for the complete catalytic solution.
These include vanadium and zeolite based selective catalytic reduction catalysts, ammonia slip catalysts, catalytic coating for wall flow diesel particulate filters and diesel oxidation catalysts
In late-2009, Haldor Topsoe introduced three new catalysts that used the company’s HEAT SCR technology. These new catalysts cut the amount of NOx from 12 g/kWh to the Euro VI requirement of 0.4-0.7 g NOx pr. kWh, a reduction of more than 95 per cent. The HEAT SCR system makes it possible to meet Euro VI requirements which come into effect by 2014. Topsoe is currently developing a second version of the HEAT SCR system capable of being retrofitted on existing diesel vehicles.
Automotive Industries spoke to Michael Dennis Knudsen, General Manager, Haldor Topsoe A/S.
AI: Tell us about some of the advances in catalyst solutions.
Automotive vehicle manufacturers are facing ever increasing requirements to reduce emissions. The US 2010 regulation implemented in the US this year and the Euro 6 legislation prepared for in Europe already place significant demands on the industry. We don’t think that it will stop here, and we believe that legislation beyond the above mentioned will focus on reduction of CO2 emissions and secondary emissions like NO2, N2O, etc. The industry, on their side, will demand reduction of PGM content in the catalysts and packaging of catalysts in the aftertreatment system. Integrating SCR functionality in the DPF is a challenging wish from many OEMs.
AI: What are Haldor Topsoe’s OEM capabilities and homogeneous SCR catalysts?
Haldor Topsøe is a relatively new player in the automotive industry as we first entered the industry on an industrial scale with the introduction of Euro 4 for heavy duty vehicles in Europe. As a catalyst company we have excellent facilities for development and characterization of catalysts. Further, we have built up facilities for validation of catalysts and systems enabling us to offer application engineering to our customers. In other catalyst business areas we generally back our catalyst products with technology. This also applies to this business, where we played a major role in developing the urea dosing technology when the SCR technology for automotive applications was introduced.
When we entered the vanadium based SCR market for heavy duty vehicles in Europe, we decided to base our catalyst technology on the SCR catalyst technology we already had for stationary applications. One of the advantages of our homogenous SCR catalyst is its high porosity. Besides making it very resistant to poisons and deactivation in general, it enables us to offer the catalyst at low cell density, still achieving similar conversion as competing catalysts with higher cell density, and thereby with lower pressure drop.
AI: What are some of the advances your company has made in diesel oxidation catalysts and catalytic coating?
The diesel oxidation catalyst is a relatively mature catalyst technology, where the task often is to find the right amount and mix of PGMs for a given application. For diesel particulate filters we have developed a catalytic coating which besides being platinum free also has the ability to reduce the NO2 emissions the noxious compound of NOx – a major concern to legislators in most major cities. Integrating SCR functionality in the DPF is also an area where we are achieving continued improvements.
AI: Tell us about Topsoe’s new diesel emission control system that use HEAT SCR.
The Topsøe HEAT SCR system is a potentially cost efficient system with less use of PGMs in the catalysts. It aims to adhere with Euro 6 legislation without the need for EGR. Besides enabling continued use of Euro 4 and 5 engine technology it will have the lowest CO2 footprint among the different systems suggested for Euro 6. A key component in that system is a very active and selective ammonia slip catalyst.
AI: What kind of work has Haldor Topsoe done in converting methanol to hydrogen?
Haldor Topsøe is a leading supplier of catalyst and technologies for production of hydrogen based on steam reforming of hydrocarbons. Our Methanol-to-ShiftTM Technology has been developed to meet increased demand for extra hydrogen from refineries and other users. It is based on a dual function catalyst, which enables simultaneous hydrogen production from both CO shift conversion and methanol cracking. The methanol feed stock is commercial grade methanol.
AI: What is the company’s vision for future fuels for the automotive industry? What do you say to recent reports that biomass-based fuels are as bad for the environment as fossil fuels – and will this change Haldor Topsoe’s focus in the hunt for alternative fuels?
Haldor Topsøe is very much devoted to R&D within the energy sector and environmental industry. We are therefore proud that our catalytic competencies enable us to play an active role in areas related to solving future energy supply challenges and improving the air quality in our environment. We are currently working on a wide range of technologies for production of alternative fuels, and we focus on technologies we believe in, also taking into account downsides with the technologies. Even though we follow and listen to the public debate, it will in general not change our focus in hunt for alternative fuels. The development of alternative fuels is very much an ongoing process, where continued improved energy efficiency in production process also matters.
More Stories
Dürr and GROB concept battery factory uses 50% less production space
DuPont materials science advances next generation of EV batteries at The Battery Show
How Modern Power Management Enhances Connected Fleet Tech