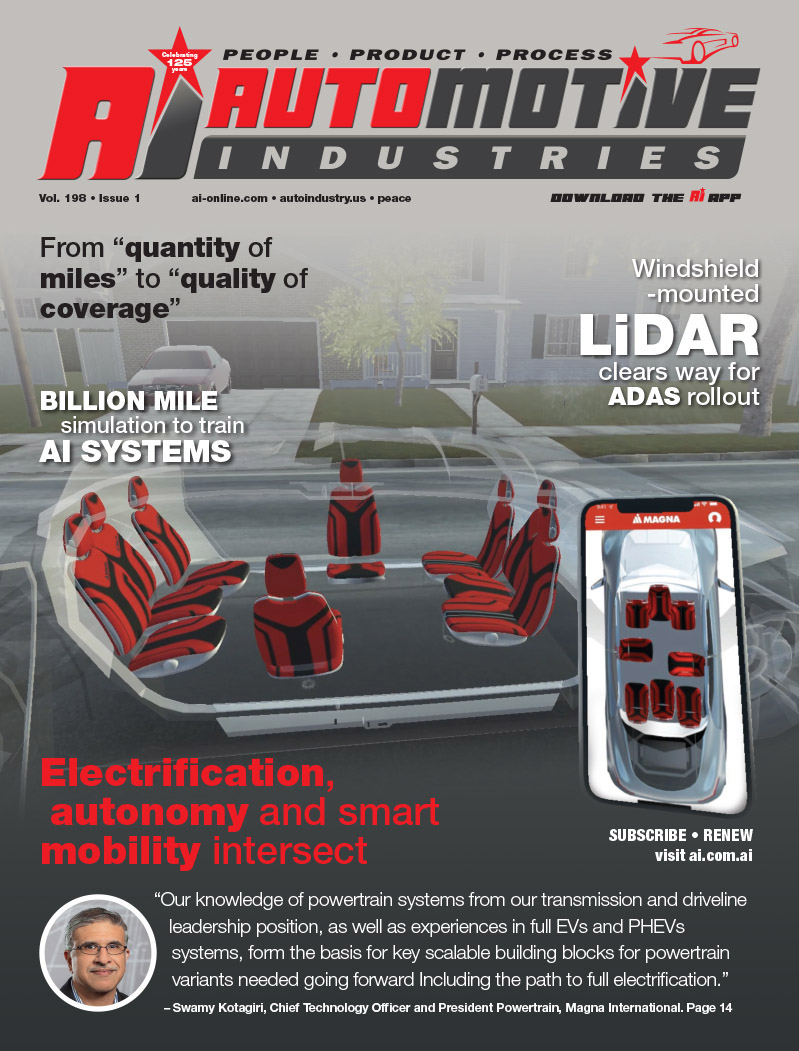
16:1 compression ratio combined with misfire free ultra lean gasoline operation developed by Transonic Combustion, Camarillo, California, has been demonstrated in a 2.2L 2900 lb car at 65 MPG highway (unadjusted FTP). Transonic’s system replaces the cost and complexity of exhaust emissions aftertreatment with unique pretreatment of fuel and unthrottled operation to put Otto (gasoline engine) efficiency in apparent leadership cost competitive position relative to both diesels and current gasoline hybrid systems.
Transonic technology, as explained by the firm’s business development manager, Mike Rocke, is based on use of super critical, high temperature, catalytically activated gasoline, injected at high pressure directly into engine combustion chambers. Rocke explains that super critical gasoline (treated in unique injectors) burns cleanly when directly injected resulting in minimum cylinder wall contact and at very high speed. Injection occurs at the optimum time when the piston is almost exactly at the ideal top dead center position. Complete combustion is achieved at very lean conditions without combustion delay and misfire. Super critical gasoline ignites instantly without an ignition source other than normal engine compression heat, says Rocke.
Asked about energy use for fuel heating, Rocke says this is provided by waste exhaust heat at engine operation above 4 bar BMEP. 300 watts of electric heating energy is needed at idle diminishing to zero as engine power increases to the 4 bar BMEP
Level.
In response to questions about engine NOx control, Rocke says this is achieved at high EGR rates which normally would cause characteristic misfire problems but is not an issue with the Transonic technology. Fast misfire free combustion applies to both lean and EGR mixtures.
Rocke further explains that the firm’s new fuel injection system operates at higher pressure compared with current gasoline direct injection but at lower pressure compared with typical high pressure diesel systems. Injection system cost is in proportion to its operating pressure level while the cost of the core engine is in proportion to robustness needed for higher operating pressures. Compared with current production direct injected gasoline engines, Transonic system engines may appear on the one hand to be somewhat more costly, but with minimal if any emissions control cost and lower cost injection (vs. diesel systems), Transonic engines have good cost-effectiveness.
.
Transonic is running engine fuel efficiency tests at a consulting engineering organization the results of which will be available in April, says Rocke.
Rocke also said he could not reveal the names of firms Transonic is working with., however, AUTOMOTIVE INDUSTRIES, has learned that Cummins Engine Company is evaluating the system. And further, that 3 auto makers are evaluating the system; one each in Japan, Germany and the U.S. and that all 3 are focused on application to 4 cylinder engines. Cummins interest suggests that robust automotive diesel cores may
indicate use of Transonic technology to replace expensive diesel exhaust emissions controls and special fluid needs.
.
Considering the Worldwide search for economic supplies of new drop-in fuel and better engine fuel efficiency, technologies such as the Transonic system take on increased meaning. With light duty vehicle engines in transition from 8 to 6 to 4 cylinders, who is to say that 2 cylinder vehicles perhaps with lean system Transonic fuel management technology may not be a next wave for mass market World cars. Current data suggests that such cars may have very high fuel efficiency.
More Stories
DuPont materials science advances next generation of EV batteries at The Battery Show
How Modern Power Management Enhances Connected Fleet Tech
Automotive Industries interviews Bahar Sadeghi, Technical Director, Car Connectivity Consortium (CCC)