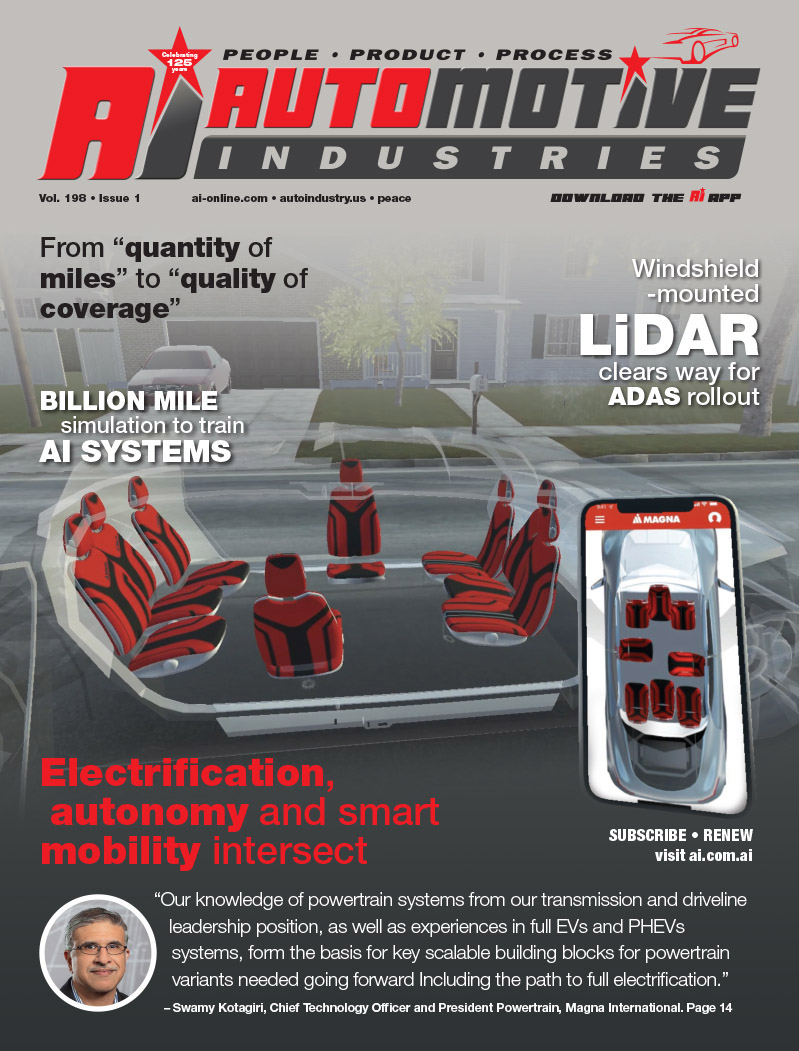
Plastic composites and other materials are starting to replace conventional bearings and bushes in a number of automotive applications in which consistent high performance and low wear are required.
Automotive Industries (AI) asked Kai Metzler, sales manager for Oiles Germany, what products had been developed for specifically for automotive applications.
Metzler: In 2009, we introduced our plastic sliding bearing (PSB) for automotive strut systems, which was designed specially for EU market. Unlike conventional ball bearings, these bearings are made completely from patented Oiles Plastic material. Movement is on a sliding base rather than steel balls. Another product is our multi-layer bushes for belt tensioners and decoupling pulleys introduced in 2008. For the past two to three years, Oiles has also been offering graphite-based bushes for use in applications such as butterfly valves in exhaust systems.
AI: What are the advantages of plastic and graphite bushes?
Metzler: The advantages in comparison with standard ball bearings include extremely low wear (0.07 ) mm over a normal standard OEM test of 1.6 million cycles. It is also possible to increase the length of the strut spring because of a reduction in construction height. Other advantages include zero corrosion due to the use of pure plastics, a reduction in news even over prolonged use, a mass saving of up to 50%, and potential savings of up to 20% on the cost of an Oiles PSB compared to a standard roller bearing.
AI: What is different about your multilayer bushes?
Metzler: Oiles designed a high-performance multilayer bush especially for use with decoupling pulleys and belt tensioners. The bush is built up from different functional and material layers that give it a clear advantage over other products. In today’s high-performance engines, the stresses and vibration rates on pulleys and belt tensioners are extremely high, as are the minimum specifications set the OEMs. The Oiles multilayer bushes are 100% compliant with the physical requirements of the motor and the specifications set by the OEM. The bushes have been proven to offer long life, low wear, high performance, as well as noise reduction.
AI: What about graphite bushes?
Metzler: Generally, in the case of applications such as butterfly valve bushes, customers want a bearing that runs silently, while at the same time offering high performance over its lifetime. In the case of steel or ceramic bushes, there is often a problem that they emit noise by rattling. Oiles’ graphite bushes combine damping performance with the high wear resistance in one product, based on our specially developed graphite material.
AI: What projects have you been awarded in the last 12 months based on these products?
Metzler: Over the past year, we have been awarded a number of projects by European Union – based OEMs for both vans and luxury cars. In addition, Oiles is continuously awarded new projects by Japanese manufacturers with plants in the European Union. Oiles’ multilayer bearings are also being used in several new high-volume models which are in the start-up phase. EU OEMs have placed high-volume orders for a number of applications using the graphite bushes as well.
AI: How do you achieve low friction, high load resistance, and long life with your products for steering applications?
Metzler: Oiles is continuously developing and testing new materials to meet the needs of the market and our customers. Development is done by ourselves in anticipation of market needs, as well as on request from our customers in the EU and rest of the world. Oiles works closely with our customers and universities to develop new materials ahead of market demand. Some of these applications are ready for production, but are not yet in series production. It is part of our commitment to being a reliable partner for sliding bearing solutions.
AI: In what other areas do you offer alternative design solutions?
Metzler: Oiles EU is working in a number of different areas. One of the bigger Oiles EU divisions is our industrial section, which supplies bushing materials based on steel, brass or graphite bases for use in all kinds of PSB applications, such as injection machines, diggers, cranes, turbines, and marine diesel motors. Based on our experience in the use of low-friction plastic materials, we are able to offer alternative solutions to those currently made out of metal or metal/plastic combinations. Costs may be saved through the integration of different functionalities into a single material, while remaining within the specifications.
AI: Where do you see the biggest potential for growth?
Metzler: We will continue to work closely with our customers to improve design and performance while reducing costs.
AI: How do you tell potential customers about your products?
Metzler: Oiles is continually making presentations and providing products for testing. We will also work with customers to improve their existing design, or to be involved at the start of a new design cycle.
More Stories
Dürr and GROB concept battery factory uses 50% less production space
DuPont materials science advances next generation of EV batteries at The Battery Show
How Modern Power Management Enhances Connected Fleet Tech