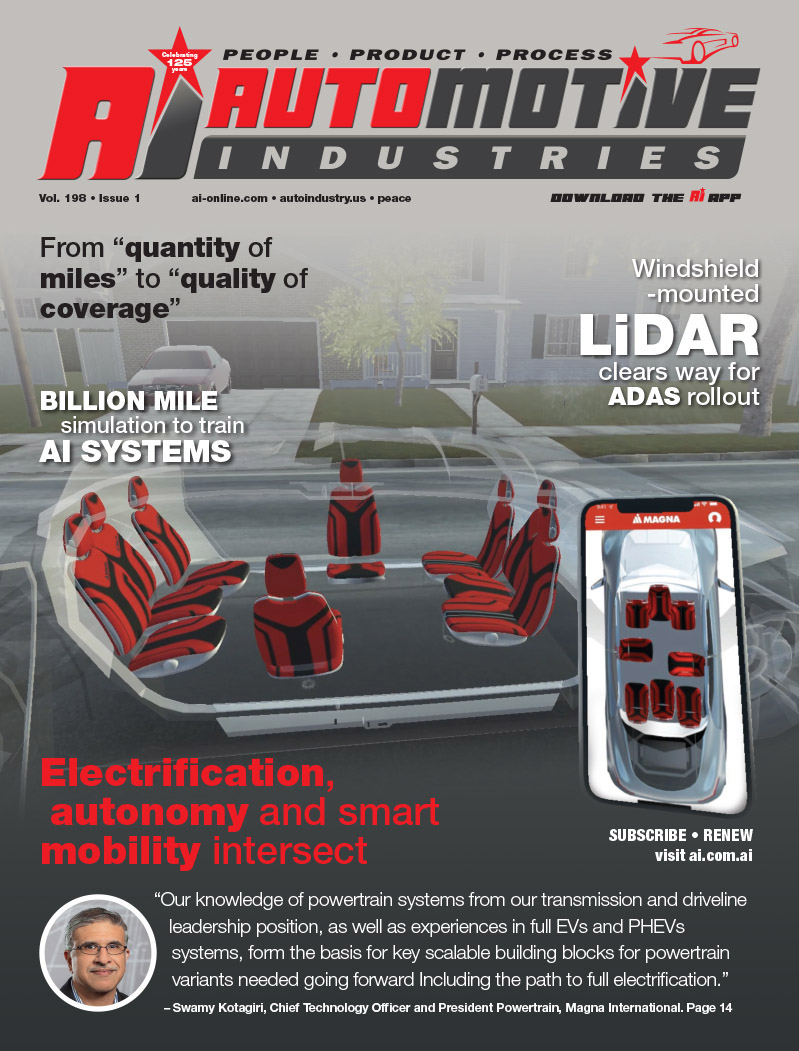
Designers and manufacturers of catalytic and ceramic honeycombs and plates are being challenged by the adoption of selective catalytic reduction (SCR) technology in vehicles after its success in stationary applications.
“The real challenge for vehicles was the development of a new geometry. An extreme increase in cell density was needed to accommodate a reasonable catalyst volume in the limited space of a vehicle. Pioneering work was done in manufacturing the new tools with ten thousands of high precision cells instead of a few hundred for stationary operations. All this R&D had to be accompanied by adjusting the necessary processing parameters of the catalytic mass,” according to Porzellanfabrik Frauenthal, which is part of the Austrian Frauenthal Holding group.
Porzellenfabrik’s SCR diesel catalyst, developed for commercial vehicles, successfully entered into series production in 2005. Diesel catalysts yield a nitric oxide reduction of up to 90% in the exhaust gases of today’s diesel engines. The various forms of usage range from low-temperature reduction of nitric oxides up to full load operation in motor vehicles. This SCR-system requires a mix of an additional reducing agent.
An example is a 32.5% urea solution marketed under the trade name “AdBlue”.
For really tough conditions such as very hot regeneration temperatures behind particle traps, the company has developed a stabilized new catalyst type. “Additionally, we fully investigate the limits of our traditional series catalysts as they are well proven in all conditions. The advantage of SCR-systems for automotive applications lies in the considerable reduction of fuel consumption up to 7%, as it is possible to efficiently optimize diesel engines,” says the company.
SCR-catalysts are homogeneous extruded honeycombs containing titanium, tungsten and vanadium. They are the leading technology for nitrogen oxide reduction in stationary applications particularly in Japan and US and, according to the company, the market is still growing. “There is a lot of public discussions about the possible loss of vanadium in the environment if catalysts are installed into mufflers of vehicles. We take our responsibility seriously, and have comprehensive projects running at well known and specialized external organizations. Toxicological behavior of the catalyst as a whole, as well as biologic influence of the separate ingredients, has been investigated. The results clearly showed that our homogeneous, vanadium containing catalysts did not damage aquatic organisms or cause cancer in approved test series,” says the company.
“Of course, the automotive market of these products is strongly dependent on the political landscape. Wherever the legal situation is requiring tougher emission limitation, more vanadium-containing catalysts will be needed. This is the case particularly in those markets where only high sulfur containing fuel is available. Our type of catalyst is completely resistant to sulfur compounds. For this reason, we see a market boom in the emerging markets within the next a few years”, says newly-appointed managing director Chaohong Zhu.
Automotive Industries (AI) asked Zhu what plans the company had to popularize SCR technology.
Zhu: As a company used to working with OEMs, as well as canners, we regularly inform our existing and potential clients about results we’ve achieved and what we are planning to do in the next steps. A lot of fruitful contacts also came through “word-of-mouth-recommendations”. In parallel with this, we intend to actively participate in relevant government projects during their preparation phase, and in other related professional organizations.
AI: What are some of the new products launched by your company recently and what impact have they had on the market?
Zhu: Developing temperature stabilized catalysts recipes combined with bigger diameters, high cell densities and thin walls are the most challenging projects we have been working on. Meanwhile, we are well on our way to produce diameters of up to 13” in 400cpsi – fully homogenous extruded – not too far in the future.
AI: Where is the fastest growth for SCR catalyst technology?
Zhu: In our opinion, the fastest growth will come from emerging markets like Brazil, Russia, China and India. With the upcoming emission regulations (similar to Euro V in Europe) big markets for SCR will be creates. The question for us now is not whether, but when? The timing for the big market demand depends mainly on the regulatory situation in the related markets.
AI: How does your company adapt technologies to different regions?
Zhu: As a flexible company we are used to follow our customers´ requirements. This gives them the freedom to choose solid, robust and cost effective technical solutions. It is precisely for this reason that continue investing in resourcing for our Research and Development Team and in our production capacity.
AI: Please tell us a little about Porzellanfabrik Frauenthal’s plans for further expansion across the world?
Zhu: Whenever the necessary volume for the smallest self-sustaining production unit has been established, we are prepared to follow our clients to the relative market. We are, of course, flexible enough to work with which local system suppliers in regions in which the OEMs are active. This is particularly important in the emerging markets.
AI: What are some of the current issues facing SCR catalyst technology, and how is
Porzellanfabrik Frauenthal dealing with these issues?
Zhu: One of the most challenging issues is the short timelines for development programs – especially if those are linked with customized new catalyst formulations. But, we are flexible enough for any reasonable adaptation and modification. Our goal is customer satisfaction. Our reaction time is fast!
AI: What are some of the new technologies/products in the pipeline from your company?
Zhu: Besides dimensional development, we are developing new catalyst recipes capable of delivering good performance in sophisticated EURO VI/US 2010 exhaust after-treatment systems in regards to NOx performance – no matter if the performance is required at low or high exhaust gas temperatures. At the end of the day our customers must have the choice out of several solutions to find the optimum for their individual application – and this is what we are targeting and striving for.
The making of Porzellenfabrik
Porzellanfabrik Frauenthal was founded in 1921 and is a specialist in honey-comb ceramics. Initially, the company manufactured high voltage insulators made of hard porcelain.
It was sold to the Swedish EUROC group, and in 1985 started manufacturing SCR catalysts. In 1990, a management-buy-out took place. Through strategic expansion and acquisition the new brand name CERAM was established. The CERAM group is now the world’s second largest manufacturer of porcelain insulators. In 2001, the insulator division was sold to American investor group The Riverside Company and Porzellanfabrik Frauenthal was taken over by Frauenthal Holding. Since then, catalysts and non-catalytic honeycombs have become the company’s main business. The Austrian group Frauenthal Holding is a group of industrial companies with 13 production sites in Europe, and sales and representative offices in the United States, China and South Korea. The Frauenthal Group, headed by Frauenthal Holding AG, which has three divisions – industrial Honeycombs, comprising Porzellanfabrik Frauenthal, which produces ceramic honeycombs that are used as SCR catalyzers for flue gas purification at thermal power stations, waste incinerators and other large combustion plants, as well as heat exchangers and foundry filters.
The Automotive Components Division, consists of truck component suppliers, which manufacture leaf springs, suspension arms, stabilizers, braking system air reservoirs, U-Bolts and diesel catalysts for automotive manufacturers in Europe. Finally, there is the Wholesale Plumbing Supplies, made up of the SHT Haustechnik Group, which distributes a number of third-party brands in Austria, as well as its own Prisma and SaniMeister brands.
More Stories
Dürr and GROB concept battery factory uses 50% less production space
DuPont materials science advances next generation of EV batteries at The Battery Show
Cybord warns of dangers of the stability illusion