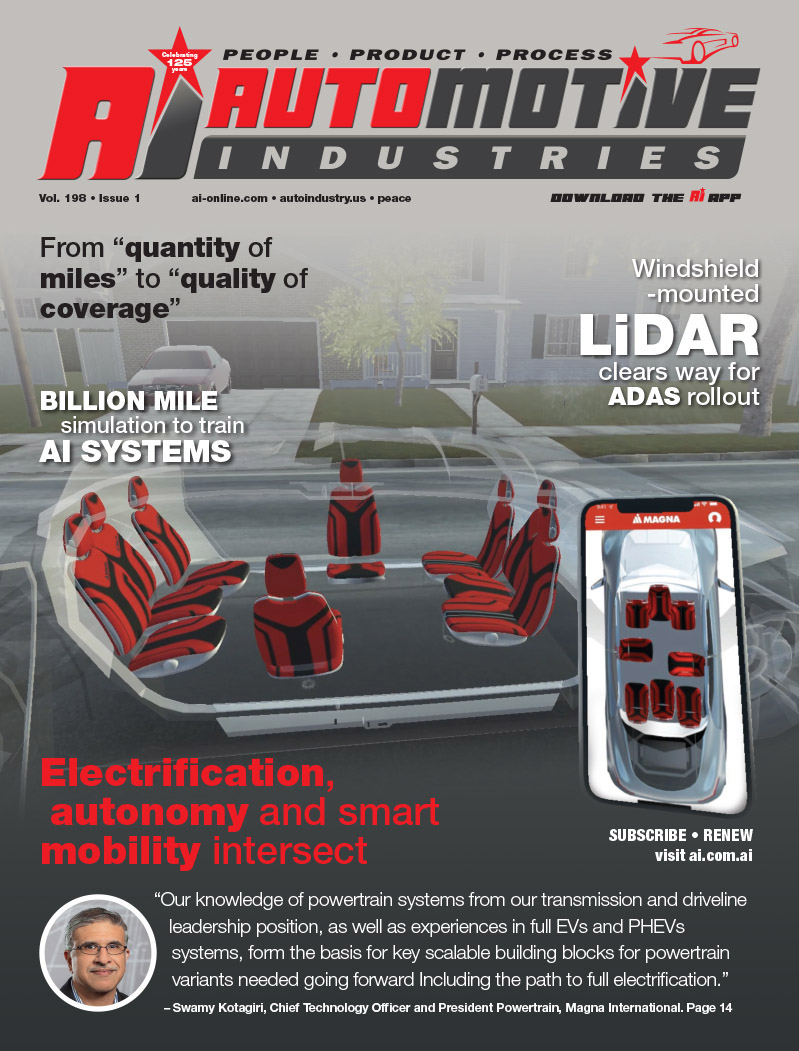
OEMs like Mercedes are building up a wealth of experience in operating electric vehicles in the field. On the road is the second generation BE Smart, with the third generation coming out later this year. Mercedes also has a BE A-class on the road, an electric Vito van, an electric B-Class with fuel Cell and a City Bus with fuel cell.
Automotive Industries (AI) asked Dr Christian Mohrdieck, Director Fuel Cell & Battery Drive Development, Daimler, to tell our readers more about his company’s electric vehicle strategy and partners.
Mohrdieck: Battery technology is one of our zero emission technologies that is very well suited to small and compact cars like the A- and B-class and Smart. We have a large number of regular suppliers. For example the S-class hybrid battery was done together with Continental and JCI. Our most important partner is Li-Tec Battery GmbH – a Joint Venture of Evonik Industries AG and Daimler AG. In China we work on a battery electric vehicle together with BYD. We also have a partnership with Tesla, in which we have a stake and which provided the battery and the on-board charger for the second generation Smart electric drive and the electric A-class.
AI: What would be the difference between Daimler EVs and the competitors?
Mohrdieck: It is pretty much the same as with the regular cars. Our cars will have all the Mercedes-Benz features our customers expect, like very high quality, very high safety standards and comfort level, and driving pleasure which you get from all our internal combustion cars. We always strive for the best or nothing approach.
AI: Where do you see the biggest potential in the medium and long run?
Mohrdieck: Hybrid and powertrain development takes time. I always remind people that the hybrid story started in 1997, and today we have some 4-5 million cars with hybrid drivetrains on
the road. This shows that you need time. If you want to introduce a new technology, you need at least five years for development, in order to match with the referring product market launch. Over the short term the vast majority of drive trains will be internal combustion engines. Over next five years I see more and more hybrids. And, step by step, an increasing number of zero emission vehicles. In the 2020 time frame, zero emission technologies like fuel cells and battery electric vehicles will still represent a single digit percentage of the market population.
AI: Where do you see the biggest problem in creating a successful EV infrastructure?
Mohrdieck: The biggest issue is cost. Utility companies can easily solve the technical issues. Electricity is relatively cheap, and in order to recover the investment of a charging infrastructure you need to sell a lot of electricity. It takes a long time to recover the investment for a charging station by selling electricity, so the problem is the business case for a public EV infrastructure.
AI: Do you have the same emphasis on F-cell as much as the electric car?
Mohrdieck: Yes. If I look at the number of people working on batteries and fuel cells in my department they are about the same. The equal spending reflects our strategy that there is not one unique technology that can solve all the issues. How is this also linked to our product scope? Mercedes-Benz Cars has a very broad product portfolio ranging from Smart, to sedans like E-class, S-class, and up to heavy duty trucks. We need a variety of powertrains to meet all customer requirements and all regulations worldwide.
AI: How do costs compare between electric and F-cell technology?
Mohrdieck: This is a question of time. Today, battery technology is more affordable than fuel cell technology, but the cost reduction potential of the fuel cell technology is much higher. Battery cost is very tightly linked to material cost, which in turn cannot be reduced by the automotive industry or by manufacturing technology. The prospectus published by MIT shows that, in the long run, the comparable performance of fuel cell technology cost is lower than battery technology.
AI: And again the need for hydrogen fuel infrastructure?
Mohrdieck: We are ready for commercialization in 2014. But as in the other cases this will take some time. Hydrogen infrastructure is of course a big challenge. But the big advantage over the electrical infrastructure is that you need much fewer stations and the refueling time is only 2-3 minutes and then you are ready for another 400-500 Km. And there is a business case. Nevertheless, we have to build the infrastructure. We announced last year that we are going to build 20 stations together with Linde AG in Germany. The H2-Mobility partnership in Germany between OEMs, energy companies and the government will see more stations built in the near future.
AI: What do the suppliers bring in terms of fuel cell and battery?
Mohrdieck: Our intention is to involve the suppliers as much as we can. Especially on the fuel cell side, a variety of suppliers is needed. For example, I don’t think Daimler will ever do fuel cell membranes since we are not experts on that. But there are other very knowledgeable companies like Gore, DuPont, BASF and 3M with which we could work together. We also need pumps, compressors and other devices on the fuel cells. From our perspective, it is very important to have a competitive supplier scheme. We need more than one supplier per component in order to create competition in the market, as we do with the other automotive components.
This is true for both fuel cell and battery. For batteries we need a lot of sub-components like electrodes, housing, cooling system, and electronics. We need suppliers and are happy to work with anybody who can provide the expertise.
More Stories
DuPont materials science advances next generation of EV batteries at The Battery Show
How a Truck Driver Can Avoid Mistakes That Lead to Truck Accidents
Car Crash Types Explained: From Rear-End to Head-On Collisions