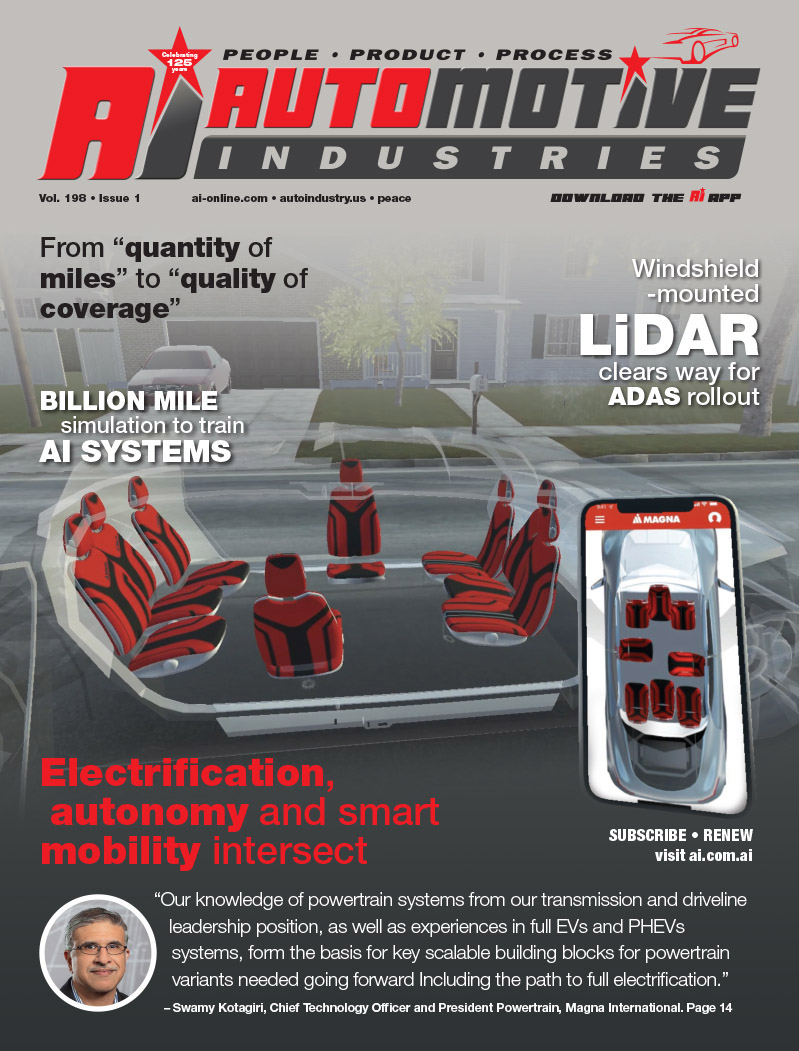
In the course of the “efficient dynamics” program in 2011, BMW introduced a downsizing in diesel engines with the adoption of the further-developed twin turbo charged 4 cylinder engine. With a power of 160 kW at a maximum torque of 450 Nm, the new 4-cylinder engine aims to be the top performer in its displacement class, and so can be used in platforms which previously relied on larger capacity engines.
In particular the use of an all-aluminum engine block enabled an ambitiously low target weight to be realized. The engine block contributes just 27.5 kg, including liners, bearing caps, and bolts, to the total weight of the engine.
The all-aluminum engine block is manufactured by Nemak Dillingen using the core package system (CPS). The use of precision sand cores in this system allows maximum design freedom, which is used in a variety of ways to achieve a higher level of integration. The coring of the side balance shaft housing, the pressure oil lines to the main bearings, balance shaft bearings and piston cooling lines, and also the coring of the various water passages and unpressurized oil cavities all contribute to minimizing weight. Not only that, the system also reduces the subsequent machining and assembly steps in the engine plant and the inherent precision engineering enhances the robustness of the components.
The high combustion pressure of the engine means the maximum stress on the engine block is in the area of the main bearing saddles and also the upper part of the cylinder bores. A drilled cooling line in the cylinder deck reduces temperatures to a level permissible in the long-term. An optimally-planned casting process and application of chills to the highly stressed zones – so-called “local engineering” – ensure the necessary high mechanical properties for these highly stressed zones of the casting.
Close cooperation between Nemak Dillingen and the development department at BMW Motoren GmbH throughout the whole design phase of the engine ensured the performance of the engine block met the aims set with regards to weight and cost. Thus at a very early stage of development, the design of components and processing requirements in the engine factory were optimized in accordance with the casting process.
In the course of development of an engine as a whole, an assessment is made of the safety factors preventing failure of individual components at critical positions. See Figure 1. These factors are calculated from the mechanical loading and thermal loading, in operation, and the assumed mechanical properties.
Furthermore, when developing this engine block, in the calculation of the fatigue strength, impact factors resulting from the engine block production process were also taken into account. So for example, the mechanical properties are particularly influenced by the local microstructure development, and this in turn can vary locally due to the casting process within the cylinder block. Predictions are made concerning the actual spread of mechanical properties based on the simulated solidification conditions so as to take account of the distribution of mechanical properties.
In addition the local residual stresses in components which arise from the processes of manufacturing, finishing, and installation are computed. So inferences could be made about how the actual local mechanical properties would cope with the forces which arise during the operation of the engine.
In addition, potential weak points arising from the core package production process were integrated into the data model for operational simulation. These include small irregularities on the core surfaces arising from the process of manufacturing the core due to the tool joint lines, injection nozzles, and ejector pins. These are depicted in the model as “notches” in the component. When under stress, these notches can induce locally increased stresses. These were previously not considered in operational simulations, and thus calculations of local safety were over estimated. Therefore, in the development of the engine block BMW N47D, the core joint surfaces and other surface irregularities were geometrically incorporated into the model by an artificial notching, and so taken into account in the simulations of fatigue strength in operation.
By considering the impacts of the manufacturing process on component properties, the predictive quality of the simulation with regards to fatigue strength of the engine is significantly increased, and thus provides additional resemblance to actual engine tests. Furthermore, this method allowed zones to be identified where mass and weight could be reduced because of the increased safety factors computed. Conversely there were zones identified where slight changes to design could be made which would result in an increase in component safety without any increase in local metal thickness.
More Stories
Towing Services Explained: 6 Key Facts You Need to Know
Environmental Factors That Influence Ceramic Coating Choices
Professional vs. DIY Tinting: What You Should Know