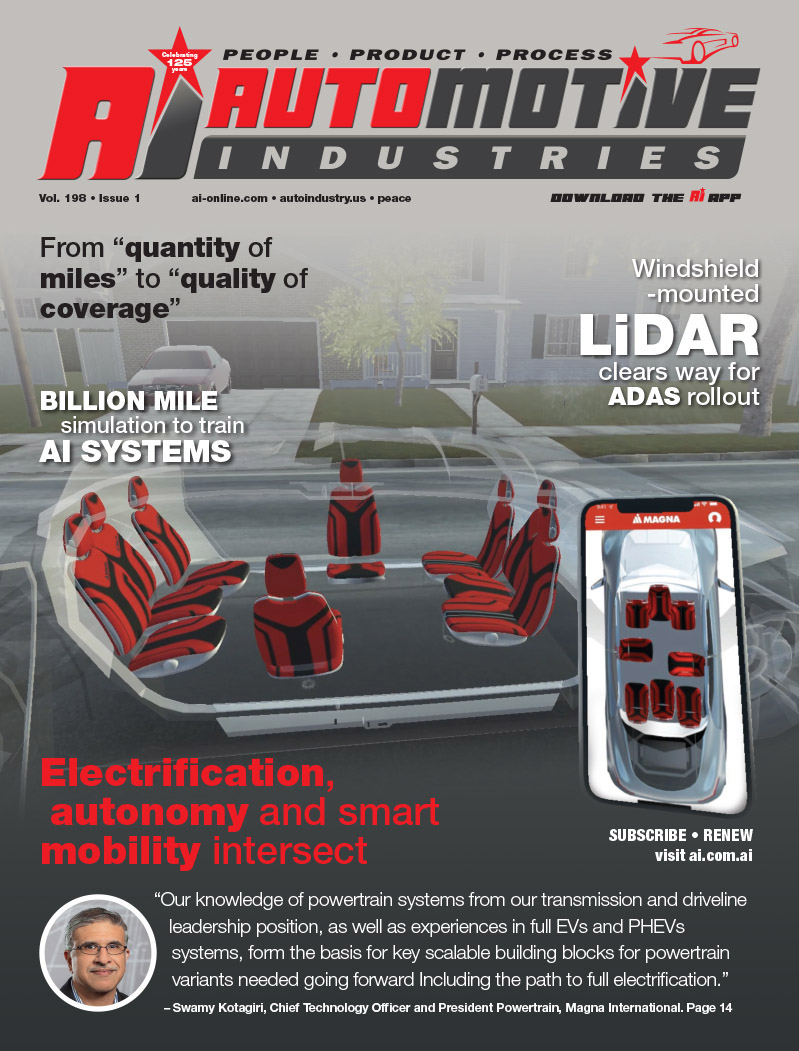
New machining technologies and systems are needed for the automotive industry to meet the large number of manufacturing challenges it faces with the advent of new power trains and ongoing pressure to reduce emissions and fuel consumption.
A leader in the machine tool field is the EMAG Group, which describes itself as the trendsetter in the market for vertical turning centers and multi-functional production machines. It has sales and service subsidiaries in 28 countries.
Founded in Bautzen, Saxony in 1867 as an iron foundry and engineering works, the company has been responsible for a number of world firsts. In 1992, EMAG developed the first vertical pick-up turning machine with a work spindle that traverses the main axes whilst the tooling systems are fixed. Since then, the machines have developed into multi-functional production centers that can also be used for drilling, milling, grinding, gear cutting and associated processes. In June 1998 EMAG introduced the VSC DS Turning and Grinding Center with an innovative combination of hard turning and finishing grinding technology. The acquisition of NAXOS-UNION, a leading manufacturer of crankshaft grinders, followed in 2002. The introduction of LaserTec laser welding machines, as well as in 2009 the addition of ECM (Electro Chemical Machining) processes extended its technological range.
Automotive Industries (AI) asked Dieter Kollmar, CMO EMAG Group, what are some of the reasons EMAG’s technologies are popular with the automotive sector.
Kollmar: The EMAG Group is in a unique position as a manufacturer of machine tools and production systems in that we cover the entire process stream in soft and hard machining. The wide range of technologies includes turning, drilling, milling, gear cutting, grinding, laser welding, ECM deburring, PECM machining and automation.
AI: Tell us a little about your prod¬uct lines for the automotive sector.
Kollmar: Our mission is to supply superior machining systems for the mass production of precision metal parts. At the EMAG Group we focus on what we call strategic components where we aim at offering clear benefits to our customers. Our machining solutions should be superior first of all in terms of cost per piece produced. Flexibility and energy efficiency are also important criteria for our product development.
AI: What makes the new vertical tuning machine VL 2 P a good solution for automakers?
Kollmar: The VL 2 P is ideal for the machining of work pieces with short runtimes. It offers short cycle times and exceptional component quality. These are features that will continue to draw attention. There are a great many factors that influence the cost of machining a component – from general output rates and tool life to the actual quality of the end product. We have kept a close eye on these factors during the development of our machine. As a consequence, the VL 2 P provides a comprehensive solution for the turning sector. It is a vibration-resistant machine, which leads to a better surface finish and increases tool life.
AI: What are some of the manufacturing challenges automotive manufacturers face and how can EMAG help?
Kollmar: The combustion engine will be partly replaced by electric propulsion systems. We anticipate a major change in power train components and, as a consequence of the machining applications involved. In total, however, the number of mechanical components for instance in hybrid drive systems, will probably remain relatively stable.
Ever stricter requirements towards fuel consumption and exhaust emission are leading to a general weight reduction of automotive parts in combination with higher accuracies. As a consequence the demand for rigid, high accuracy machine tools will rise proportionally.
What are some of the manufacturing challenges automotive manufacturers face and how can EMAG help?
Depending on the application, multi-tasking machines can also reduce the cycle time and the machine quantity.
AI: How do you see your Asian markets growing?
Kollmar: We are extremely positive about the prospects for EMAG. As the technological leader in our field, we believe in the future of high quality solutions for the mass production of accurate components. China has become and will remain the key market for our future growth. We intend to grow along with our Chinese customers. It is our challenge to keep abreast of our competition by continuously innovating our products and upgrading our services. We know that we can only be successful in China if our customers are successful.
AI: What has been your experience so far in China?
Kollmar: Over the last few years the size of our business in China has multiplied, which reflects both the strong growth of the market, as well as fact that our products are very well received in China.
AI: What are some of the new technologies EMAG is working on?
Kollmar: The strength of EMAG is the direct access to the broad array of basic machining technologies that we cover, and the extensive process know-how accumulated over the years. EMAG sets the technological standards for many world-class machining applications. To maintain our competitive edge and our leading position in the market for machining solutions for mass production is our main challenge. Permanent innovation is our answer and the key to our future.
We are constantly investigating solutions for new components and about ways to further optimise our machining platforms. We have several products in the pipeline that will be released soon. Besides innovating our products, we endeavor to reduce our production cost to the benefit of our customers. That is why we invest heavily into a new machine tool factory in Jintan.
More Stories
Towing Services Explained: 6 Key Facts You Need to Know
Environmental Factors That Influence Ceramic Coating Choices
Professional vs. DIY Tinting: What You Should Know