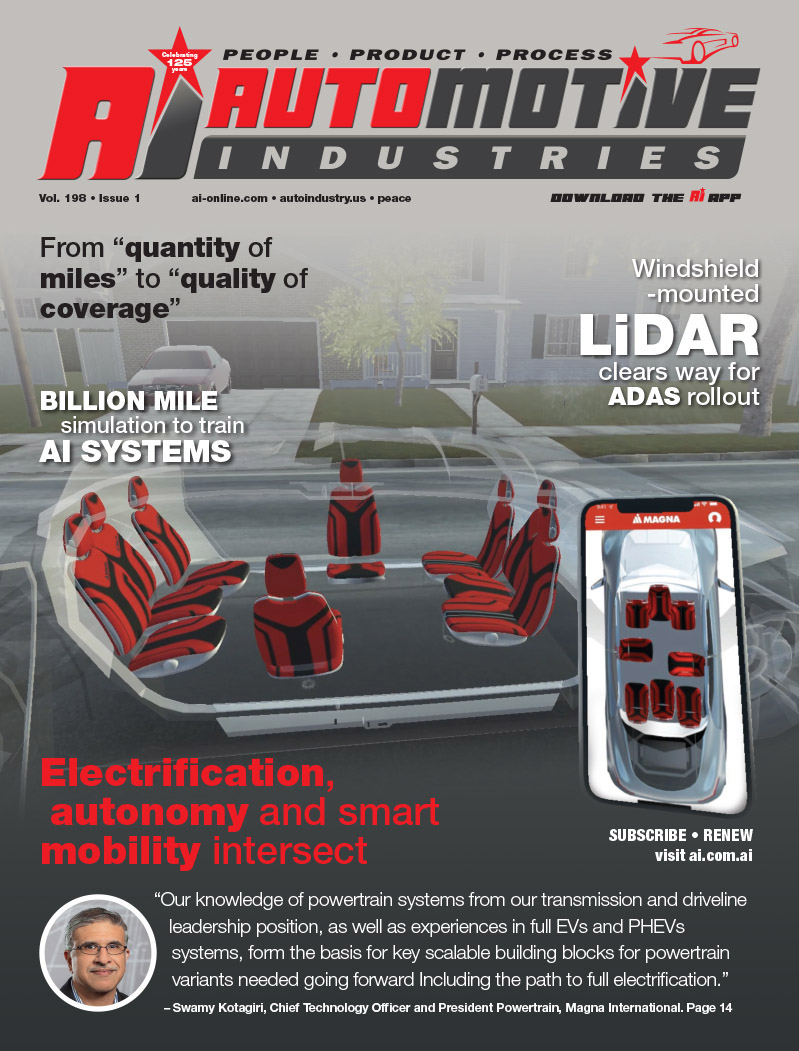
Styron collaborated with value chain partner Autocomponent in the creation of instrument panel components for the GAZelle Next and Lada Priora Face lifting platforms which were based on Styron’s VELVEX™ 5250. VELVEX™ 5250 has obtained its first commercial application in the GAZelle Next and is being evaluated for Priora Face lifting platforms.
The need for a high performance cost-efficient raw material solution
Autocomponent, a leading manufacturer and exporter of automotive components, was tasked with a development challenge of fabricating next generation instrument panel components for the GAZelle Next and Lada Priora Face lifting platforms that would meet industry needs for high performing cost efficient solutions. In order to meet that challenge, they were looking for a raw materials partner with whom they could collaborate. Autocomponent presented the advantage of having one material in one color for their instrument panel components for both platforms (Priora and GAZelle) as well as fulfilling requirements such as enhanced soft touch, scratch resistance and low gloss levels.
Styron with Autocomponent every step of the way
In the creation of the instrument panel components, Styron collaborated closely with the OEMS and Autocomponent in the development phase and was committed to going that extra mile to make this innovation project a success. In addition to providing the raw material solution, Styron provided the vehicle manufacturers and Autocomponent with expert technical support including design review and Moldflow® studies through our Application Engineering and Design Center, as well as extensive color lab work during the project start up. Furthermore, Styron’s Technical Service and Development group supported Autocomponent with technical trials to gauge the performance of VELVEX™ 5250s with existing tools, and additional trials were conducted to establish further ways to optimize the processing conditions. At the completion of the trials, Autocomponent concluded that VELVEX™ 5250 proved to be a good fit for the engineering challenge that it was confronted with. As a result, both the GAZelle Next and the Lada Priora Face lifting platforms benefit from interior parts with improved soft touch, scratch resistance, low gloss while meeting the need for cost-efficiency in raw material usage. This collaboration was part of a two-year project that culminated in the first commercialization.
“By going that extra mile, Styron helped fine-tune Autocomponent’s production process and ultimately helped them fulfill their objective to create high performing instrumental panel components in a cost-efficient way. This collaboration was part of a two-year project that culminated in the first commercialization of VELVEX™ 5250 worldwide, I am extremely proud of all the Styron team members that have collaborated to turn this project into a success;” explains Dagmar van Heur, Vice-President, Styron Automotive.
VELVEX™ 5250: designing a part that meets all requirements
Using Styron’s VELVEX™ 5250, Autocomponent developed instrument panel covers, trims and glove boxes with enhanced scratch resistance performance and low gloss levels at a competitive price, thus aligning with industry demands for cost-efficiency.
VELVEX™ 5250 is a reinforced elastomer/PP compound which provides a unique balance of part performance and easy processing and allows for a cost efficient high throughput production process. It also offers better scratch-and-mar resistance and a uniform low gloss than established materials such as most talc-filled PP, PA/ABS or ABS products. The best-in-class scratch and mar-resistance provides extended surface durability.
VELVEX™ 5250 offers a cost-efficient opportunity for premium surfaces, supporting the impression of luxury in vehicle interiors. Until now, the industry has had to choose between: unpainted materials that could not offer satisfying scratch resistance or uniform gloss, or alternatively, painted parts which demonstrated a good performance but increased cost because of the need for an additional painting step.
About Styron Automotive
Styron Automotive, a business unit of Styron, delivers breakthrough innovative solutions for automotive interior and exterior components. ABS, Polycarbonate, PC/ABS, LGF PP, TPOs and elastomeric materials from Styron Automotive are helping advance applications like mid and upper consoles, instrument panels, blow molded seat backs, bumper fascias, trim, and more.
From best-in-class scratch resistance and light weight to high heat resistance and low VOC levels, Styron Automotive resins offer exceptional durability, high-end aesthetics, and cost efficiencies to help OEMs differentiate their automobiles and brands.
To learn more about Styron Automotive visit our website: www.styronautomotive.com.
About Styron
Styron is a leading global materials company and manufacturer of plastics, latex and rubber, dedicated to collaborating with customers to deliver innovative and sustainable solutions. Styron’s technology is used by customers in industries such as home appliances, automotive, building & construction, carpet, consumer electronics, consumer goods, electrical & lighting, medical, packaging, paper & paperboard, rubber goods and tires. Styron had approximately USD 5.5 billion in revenue in 2012, with 20 manufacturing sites around the world, and 2100 employees. More information can be found at www.styron.com.
More Stories
Towing Services Explained: 6 Key Facts You Need to Know
Environmental Factors That Influence Ceramic Coating Choices
Professional vs. DIY Tinting: What You Should Know