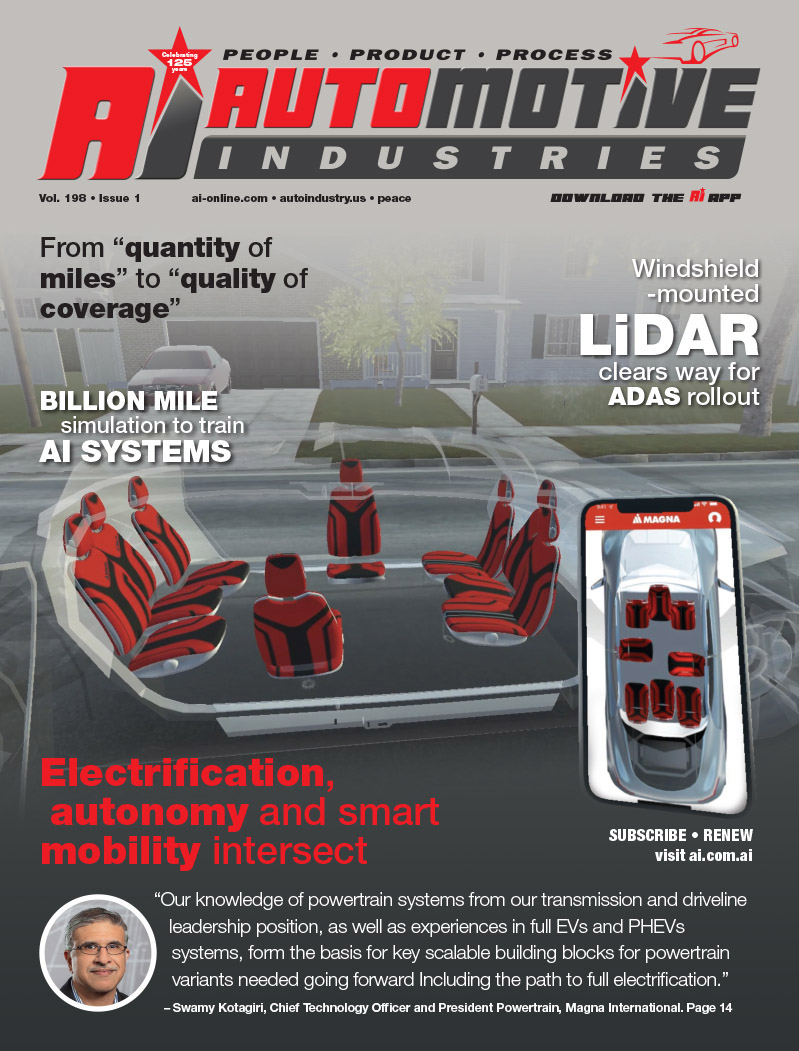
Robots and people are working side-by-side on production lines in order to maximize the abilities of both. An example is the 2,800,000 m2 Volkswagen plant in Salzgitter, Germany. It is one of the largest engines production plants in the world. Some 6,000 employees manufacture approximately 7,000 gas and diesel engines in over 370 variants every day.
The OEM recently deployed a collaborative industrial robotic arm from the Universal Robots for the purpose of inserting glow plugs into the cylinder heads. Production line staff had been stooping over the components in order to insert the glow plugs into concealed drill holes. This step is now being taken over by the six-axis UR5 lightweight robot from Universal Robots. It picks up the delicate glow plugs using a collaborative gripper system developed by system integrator Faude Automatisierungstechnik, and places them into the hard-to-reach drill holes. An employee is then responsible for fixing the glow plugs and insulating the cylinder head. “We would like to prevent long-term burdens on our employees in all areas of our company with an ergonomic workplace layout.
By using robots without guards they can work together hand in hand with the robot. In this way, the robot becomes a production assistant and can release staff from ergonomically unfavorable work,” explains Jürgen Häfner, project manager at Volkswagen’s Salzgitter plant. The robots are able to work alongside humans because of their integrated safety mode (matching Standard EN ISO [AJ1] 10218). If the robot comes into contact with an employee, it will stop operating without injury to the human.
Automotive Industries (AI) asked Thomas Visti, Vice President and CCO of Universal Robots whether it was true that BMW was looking at deploying the same safety technology to insert glow plugs into the engine block as VW.
Visti: BMW has collaborated closely with us from the time Universal Robots was a young and unknown company. We are working on numerous projects with them, but due to the confidential nature of our partnership we can only publicly talk about our car door application already released and installed at their plant in Spartanburg, South Carolina. In this setup, the UR10 robot (UR5’s big brother with a payload of 10 kilos) is performing a roll operation that follows the perimeter of a door panel, pressing a glue bead around the panel to create a watertight seal.
AI: Tell us a little about the relationship between Universal Robots and VW.
Visti: We first visited Volkswagen in Salzgitter in 2009, where I did a demo at their plant. At that time, Universal Robots was a brand new product and we had only sold around 100 robots – about the same amount that we sell per month right now. Not long after our visit, Volkswagen purchased the first robot. Since then, we’ve had regular meetings with them, but the primary contact for this project has been our competent distributor, Faude Automatisierungstechnik.
AI: How would you rate the success of your collaboration with VW and how do you see this impacting future automotive business?
Visti: Our collaboration with Volkswagen has been successful on all levels due to Faude Automatisierungstechnik’s ability to implement the solution. The fact that Volkswagen has integrated the first collaborative robot into its mass production facility has attracted a significant amount of interest around the world, both from automotive manufacturers and other companies seeking easy, affordable ways to automate production.
AI: How did Universal Robots and VW work together to maximize benefits?
Visti: Our distributor Faude Automatisierungstechnik worked closely with Volkswagen to develop a customized solution that was right for them. The robot grippers installed in the application have been specifically developed by Faude.
AI: How do you see this helping future advances in streamlining automotive manufacturing?
Visti: Our collaborative robots have pioneered a new trend within automation and robots – in all industries. Being able to work directly alongside a portable robot with no safety guards enables an unprecedented amount of cost saving and flexibility in your production; your new colleague can be a robot that optimizes both the production and alleviates workers of monotonous tasks, often promoting them to higher skilled positions. This concept is thrilling to many companies looking for new ways to stay competitive while also creating better working conditions for employees. Currently, 80% of Universal Robot installations worldwide operate with no safety shielding, but of course every installation depends on prior safety assessments.
Automotive Industries then asked Edward Mullen, National Sales Manager, Universal Robots USA what kind of business Universal Robots does in North America?
Mullen: Universal Robots introduced itself to the North American Market in September of 2012. Since then, we have implemented a high tech distribution channel throughout the US and Canada, giving us 100% coverage of all areas. Our distributors have done a phenomenal job penetrating a wide variety of industries including automotive, machine tools, medical, packaging, assembly, pharmaceutical, and electronics to name a few.
AI: Has it broken into the automotive sector?
Mullen: Yes absolutely. We have had tremendous success with BMW here in the US. In addition, we have the attention of most all other automotive manufacturers. Successful applications like parts placement, assembly, screwing, and gluing continue to help us grow through this industry.
AI: What benefits can North American automakers get from Universal Robots’ technologies?
Mullen: Our technology allows any small, medium and large company to successfully implement automation where it was impossible to in the past. The ability to potentially run unguarded, coupled with the flexibility to quickly reprogram or even reallocate our robot opens up endless possibilities to implement automation. Implementation is quick due to the user-friendly, intuitive nature of the robots. Often, programming and installation is done in a matter of hours.
AI: What are some of the advances in auto¬motive manufacturing that makes North America an important market for Universal Robots?
Mullen: I believe North American manufacturing is focused on becoming more efficient and keeping manufacturing here at home. It is, therefore, imperative to be able to convert existing process to automation. In addition, there is a major focus on ergonomics and of relieving workers of repeated, monotonous tasks.
AI: How do you see business growing in the region?
Mullen: We have only been here about a year now and see tremendous interest across the board in all industries. I truly believe the growth will be epic, as awareness grows around collaborative robots and the safety organizations continue to evolve the specifications.
More Stories
Auto Repair Services: Keeping Your Vehicle Road-Ready
Unleashing Creativity with Vidnoz: The Best Free AI Video Generator in 2025
The Connection Between Air Drying and Energy Efficiency in Industrial Settings