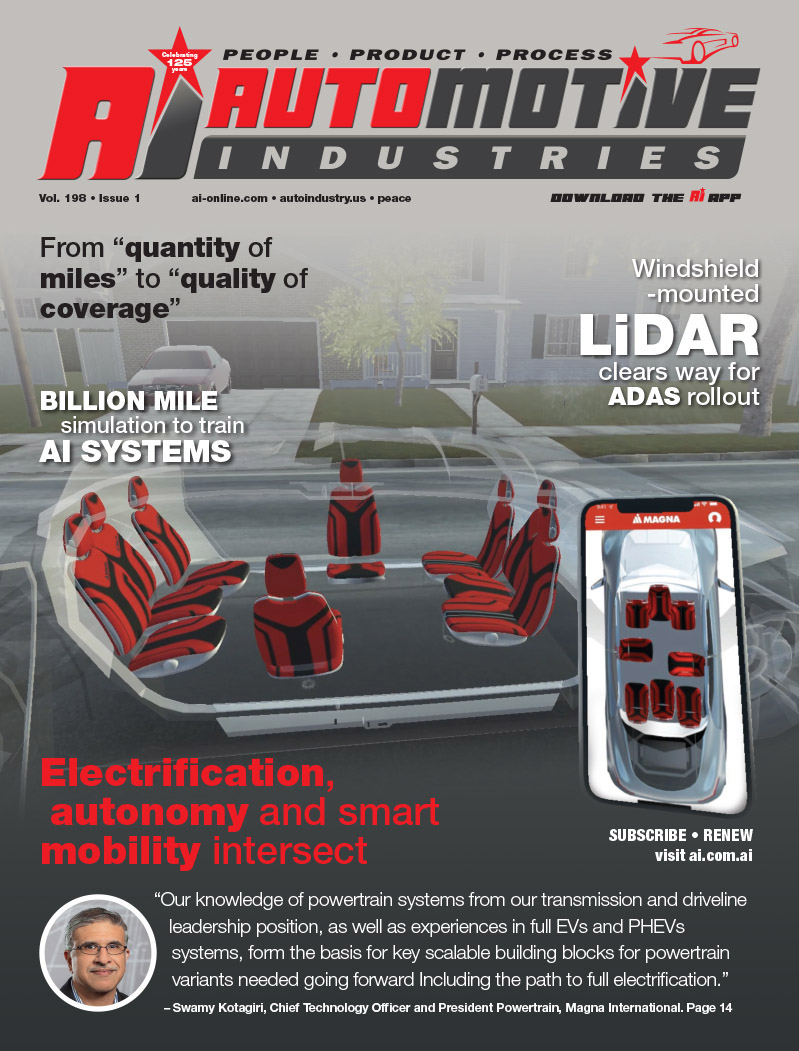

Visitors to the 35th International Vienna Motor Symposium hosted in May 2014 were introduced to the concept of a “mild hybrid” by two leading international automotive suppliers Schaeffler and Continental.
Their Gasoline Technology Car (GTC) joint project demonstrates how a networked integration of key mild hybrid technologies can cut fuel consumption as well as CO2 emissions by an additional 17% in the case of an already highly efficient car powered by a downsized 3-cylinder gasoline engine – the Ford Focus 1.0 l EcoBoost. “To achieve this level of hybridization, we have integrated and systematically networked key technologies from the Continental and Schaeffler portfolios into the GTC. The results we achieve with the vehicle point up the potential of this strategy in a car whose engine was nominated “International Engine of the Year 2012 and 2013” for its efficiency and performance,” says José Avila, Member of the Executive Board of Continental and President of the Powertrain Division.
Main elements of the integrative approach
The project partners report that they have optimized every aspect of the GTC’s powertrain engineering. Playing key roles are Continental’s 48 Volt Eco Drive System as mild hybridization and Schaeffler’s electronic clutch (e-clutch) for power transmission and its thermal management module. These are complemented by measures to reduce friction loss in the engine and an electrically heated catalytic converter (Emitec). With these components and the intelligent operating strategy, the GTC prototype not only improves fuel efficiency by 17% overall, it also meets the limits set by the upcoming Euro 6C emissions standard (2017/2018).
To ensure the driveability of the 3-cylinder, 1.0-liter engine despite the modified, rigorously ignition-timing-optimized operating strategy and to allow for use of additional hybrid driving strategies, the GTC features an independent second drive unit, the 48 V Eco Drive System. This includes an electric motor with integrated decoupling tensioner. The electric traction motor/generator is connected via a modified belt drive to the combustion engine. A DC/DC converter facilitates electrical energy flows between the 12 V voltage levels and the 48 V end with lithium-ion battery (dual-battery design). This hybridization supports the combustion engine electrically in the lower RPM range (e-boost function) to ensure attractive responsiveness without turbo lag.
The highly efficient 48 V recuperation provides the basis for this. In the NEDC, the GTC can recuperate almost twice as much momentum as the vehicle requires for its electrics. In line with the strict design-to-cost approach applied by the partners, the GTC prototype is equipped with a conventional six-gear manual transmission. Energy-saving functions such as coasting are also part of its drive strategy. The Schaeffler electronic clutch integrated into the vehicle decouples the engine from the drivetrain when the vehicle is coasting.
As no air needs to be compressed in the combustion chambers when the engine is idle, more energy is available for recuperation. This energy facilitates other efficiency-enhancing measures. One example is an electrically heatable catalytic con-verter. It uses the recuperation energy from the previous drive cycle to attain a working temperature faster in cold starts. In addition, a Schaeffler split cooling architecture with rotary slide valve facilitates graduated thermal management in the GTC. Its purpose is to master the challenges posed by hybrid drive strategies. The engine can be temporarily decoupled from the coolant cycle in order to attain the required tem-perature more quickly or to retain its temperature longer.
The rapid heatup reduces engine friction losses. As part of a forward-looking operating strategy cooling can also be switched off in time for an anticipated recuperation phase (downhill stretch):
The standard Continental engine control unit used in the GTC is designed to also relieve the combus-tion engine of the complex job of controlling the mild hybrid components, including the operating strategy. This engine control unit gets a head start on the upcoming EMS 3 strategy. Its open AUTOSAR-based system architecture flexibly supports various partitioning schemes and electronic topologies in conjunction with hybridization and electrification.
With manual transmission top vehicle efficiency is achieved when the driver, the optimized individual components, and the vehicle functions are in sync. For this reason, the engine control unit makes downspeeding-oriented switch point recommendations. The additional electric driving torque allows the driver to use these switch points without any negative impact on drivability and to achieve better fuel economy on the road.
More Stories
Towing Services Explained: 6 Key Facts You Need to Know
Environmental Factors That Influence Ceramic Coating Choices
Professional vs. DIY Tinting: What You Should Know