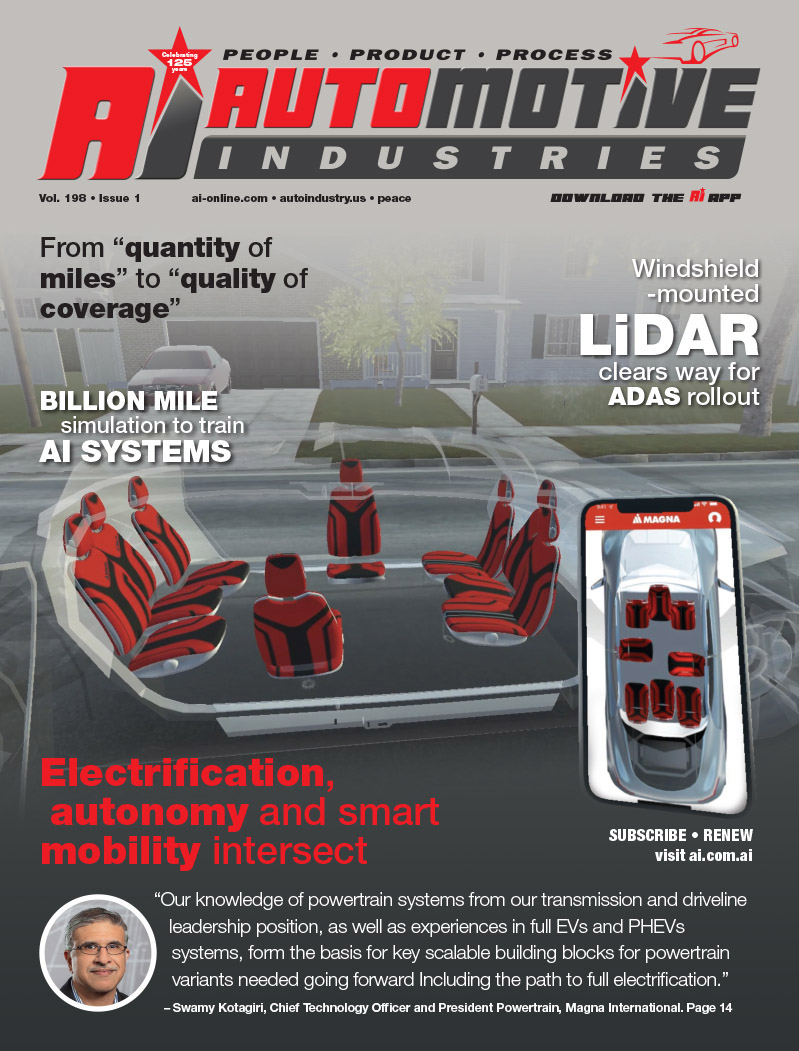
Aluminum accounts for over 75% of the content of the new Jaguar XE body – which makes it a class leader in the use of the lightweight material. Jaguar is adding to the green credentials of the vehicle by using recycled aluminum.
Automotive Industries (AI) asked Pierre Labat, General Manager Automotive at Novelis Europe, what the company’s contribution was to the development of the lightest, stiffest and most aerodynamic Jaguar sedan to date.
Labat: The lightweight XE is the only vehicle in the mid-size segment with an aluminum-intensive body structure, and is therefore setting new standards in its class. Novelis is proud to be the sole supplier of aluminum sheet to Jaguar Land Rover (JLR) for novel lightweight construction platforms, such as the XE.
AI: What alloys are used on the XE for skin sheet and structural applications?
Labat: The upscale design features unique Novelis AdvanzTM 6000 series-alloys which were developed for sophisticated automotive skin sheet and structural applications. Furthermore, the new XE is the first car in the world to use a new aluminum alloy made predominantly from recycled material specially designed by Novelis and JLR for the automotive industry.
AI: What is unique about the new alloys?
Labat: Our new Novelis AdvanzTM 6000 series-alloys set new standards in the industry for enhancing strength and toughness, formability and recyclability. And we are hard at work developing
new alloys for automotive applications that leverage a higher recycled content, adding even more sustainable efficiencies into the automotive supply chain. With automotive makers increasingly moving toward global platforms for their vehicles and as part of Novelis’ strategy to expand our automotive offering around the world, Novelis has rationalized its portfolio so that we can offer and produce the same products, regardless of region.
AI: What do they bring in terms of vehicle dynamics, handling and response, and safety?
Labat: These aluminum solutions make the XE as strong and light as possible enabling exceptional vehicle dynamics, agile handling, class-leading steering response and highest levels of crash safety.
AI: How do you help JLR to reduce its carbon footprint?
Labat: Since 2013, the Novelis recycling plant in Latchford, UK offers JLR a closed-loop recycling solution by converting the car manufacturer’s aluminum scrap metal into new material for automotive sheets. The benefits of the emerging closed-loop manufacturing model are tremendous. It reduces the environmental footprint of Novelis’ own and its customers’ operations, as well as the end consumers who buy and use the product on a daily basis.
Novelis is working closely with JLR to increase the amount of recycled material in its products, as well as to reduce its overall carbon footprint. The XE’s aluminum lightweight construction contributes to increased fuel efficiency and lower emissions on the combined cycle of less than 100g/ km. Novelis and JLR will extend their strong sustainability efforts on all future platforms using a high aluminum content and recycled material alloys, which will help achieving their ambitious sustainability goals.
AI: What model do you use for your recycling solutions with JLR and what are the benefits?
Labat: The closed-loop model strengthens our cooperative, long term relationship with JLR, driving the development of innovative new products and processes that expand the use of aluminum and reflects the aligned growth paths of both companies in reaching our respective sustainability goals.
AI: You just opened the world’s largest aluminum recycling facility in Nachterstedt, Germany. How does it fit with your strategy of moving from linear approach to an increasingly closed loop model?
Labat: The Nachterstedt recycling center is a significant step toward our goal to be the world’s low-carbon aluminum sheet producer, shifting our business model from a traditional linear approach to an increasingly closed-loop model. This project is the latest in a series of recycling expansions launched by Novelis over the past three years. Since 2011 Novelis has invested approximately US$500 million to expand its recycling network. This has doubled its recycling capacity to 2.1 million metric tons per year, and raising the recycled content from 30% to 46%. The company’s goal is to achieve 80% recycled content by 2020. Recycling aluminum saves 95% of the energy and emissions associated with the production of primary metal.
Located adjacent to the company’s rolling mill in Nachterstedt, Germany, the €200 million recycling center will process up to 400,000 metric tons of aluminum scrap annually, turning it back into high-value aluminum ingots to feed the company’s European manufacturing network. The new facility further strengthens Novelis’ leadership in Europe, and together with our major recycling operations in Asia, North America and South America, solidifies Novelis’ position as the global aluminum recycling leader.
AI: How will the development of new products and processes by Novelis encourage the OEMs to increase the use of aluminum contents of the vehicle?
Labat: As part of our commitment to innovation we are continuing to advance aluminum’s role as a material of choice among the world’s auto makers by building upon our 40-year track record of technical excellence. Novelis is more than just a material supplier. Our engineers and metallurgists are working closely with our customers’ design teams at the early stages of development to help ensure the next generation of vehicles is built to maximize the attributes of aluminum.
AI: What is next for Novelis?
Labat: Globally we expect a 30% compound annual growth rate (CAGR) for automotive aluminum through the end of this decade and are continuously expanding to meet this growing demand. We’re aggressively increasing our capacity to produce automotive sheet across the globe. In less time than it takes an automaker to design and launch a new vehicle (approx. 2.5 years), Novelis can build a new automotive finishing line. Currently we are building new automotive finishing lines at our plants in Oswego, N.Y. and Nachterstedt, Germany with a capacity of 120,000 metric tons per year each. When the new lines are commissioned in late 2015, Novelis’ global automotive sheet capacity will reach approximately 900,000 tons per year, a three-fold increase from just a year ago.
To support the automotive growth, we provide world-leading technical support and constantly develop new innovations at our Research and Technology Centers in Kennesaw, GA and Sierre, Switzerland. The facilities include heat treatment capabilities for automotive combined with our state-of-the art lab technology, which allow our scientists to test alloys and their formability, anti-corrosion, bonding, hemming and other properties. We are committed to “sustainable innovation” in automotive – focused on vehicle lightweighting and closed-loop recycling.
More Stories
DuPont materials science advances next generation of EV batteries at The Battery Show
How a Truck Driver Can Avoid Mistakes That Lead to Truck Accidents
Car Crash Types Explained: From Rear-End to Head-On Collisions