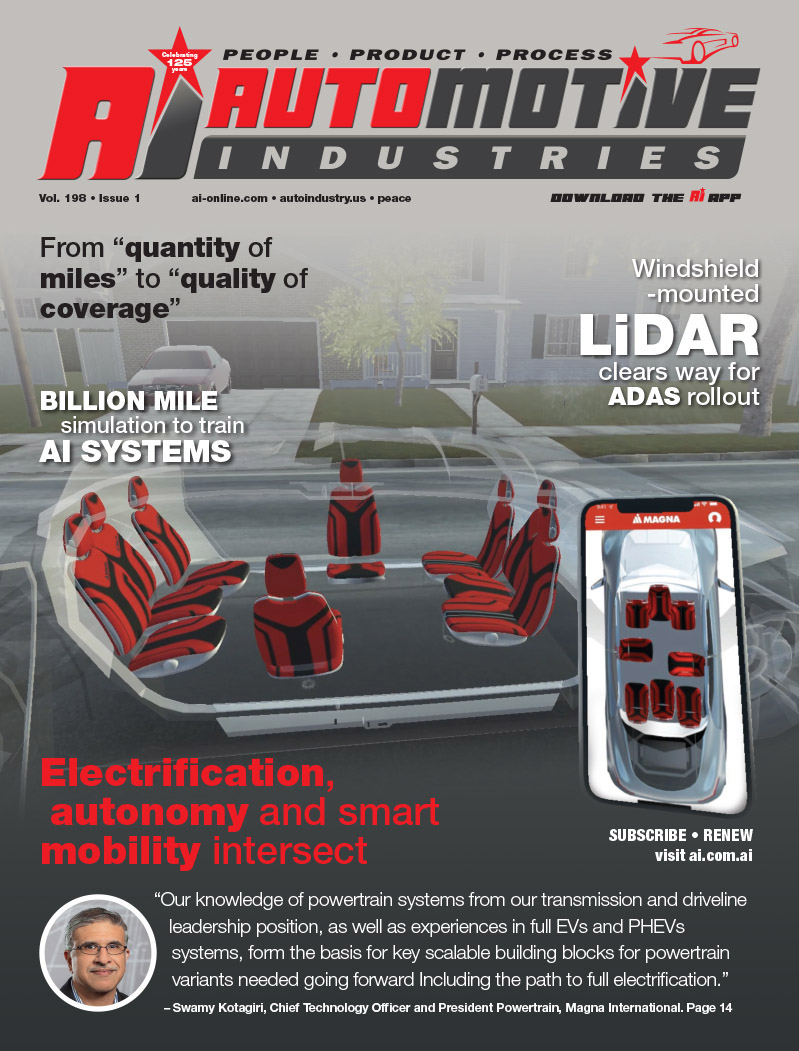
“Always on” is becoming a reality not only for car drivers, but also for workshops: Patricia Stich, business administration specialist and Head of Diagnostics & Services at Continental, explains which new diagnostic solutions, and with which benefits, Continental is offering authorized workshops.
Automotive Industries (AI): Continental is increasingly offering OE diagnostic solutions to car makers. What are the arguments in favour of these products, and what highlights did you present at the IAA 2015 in Frankfurt?
Stich: Our diagnostic and service solutions for the authorized aftermarket include intuitively operated diagnostic equipment and innovative fault analysis solutions. At the heart of our range is our modular software. It allows any combination of six software modules – for diagnosis, troubleshooting, programming of control units, maintenance instructions, data inquiries and system administration. For example, the OEM can create a package which is optimally matched to its authorized workshops.
Our portfolio also contains this year’s IAA highlights for the aftermarket. We presented Remote Diagnostics solutions and our “Connected Technician” concept at this show.
AI: What does “Connected Technician” entail?
Stich: “The Connected Technician” is a new and intuitive concept study matched to the technician’s needs and providing, in the right context and at the right time, relevant information for diagnostic, repair and maintenance work.
AI: A key element of Connected Technician will be Augmented Reality (AR) applications. Will AR kill off the classic workshop manual?
Stich: We regard this technology as a supplement to the familiar workshop manuals and other media. Going beyond that, our ambition is of course to integrate the Augmented Reality solutions into workshop information systems.
AI: What benefits would accrue from integration into digital workshop information systems?
Stich: The provision of a centralized workshop information system that also covers Augmented Reality applications enhances efficiency in the working procedures at an authorized workshop. For example, visual inspections can be conducted more rapidly and more accurately thanks to this technology.
AI: In which regions do you currently see the greatest potential for Augmented Reality in authorized workshops?
Stich: Augmented Reality will be employed mainly in regions where the repair process requires more visual backup, either because the mechanics are trained to a lower standard or because of heavy employee fluctuation, as is the case in Asia, for example. This allows training costs, for example, to be reduced in authorized workshops even with high staff turnover.
AI: How is the “Connected Technician” concept proceeding?
Stich: A “Proof of Concept” (POC) is currently in progress. Applications are being defined jointly with the customer as part of the POC. In this way we can verify the feasibility of the projects with due consideration of customer requirements.
AI: Remote Diagnostic solutions have in some cases already attained production maturity. What do they offer a workshop?
Stich: It’s true that a number of solutions are available in the independent aftermarket. But most of these dongle solutions only cover level 1 data. OE-specific data are often not taken into account. Some service providers try to compensate for the missing information by means of algorithms. This can lead to significant inaccuracies.”
Our solution uses OE-specific information and makes it available to the service provider. Another advantage is that the dongle does not have to be preconfigured. It is configured to OE-specific parameters after installation. AI: Which hardware does Continental intend to start off with here? Are you going for external systems like an OBD dongle or for systems completely integrated into the vehicle architecture?
Stich: Both. In the independent aftermarket (IAM) we’ll be using dongle or similar technology. In Original Equipment Services (OES), we’ll be using a hardware solution to be integrated into the vehicle architectures.
AI: Has any practical experience already been gained with these systems?
Stich: We’ve been conducting field tests for the past 12 months, on more than 200 vehicles from a variety of partners, customers and even Continental employees. We’re using the feedback from those involved for continual improvements to our solution.
More Stories
Towing Services Explained: 6 Key Facts You Need to Know
Environmental Factors That Influence Ceramic Coating Choices
Professional vs. DIY Tinting: What You Should Know