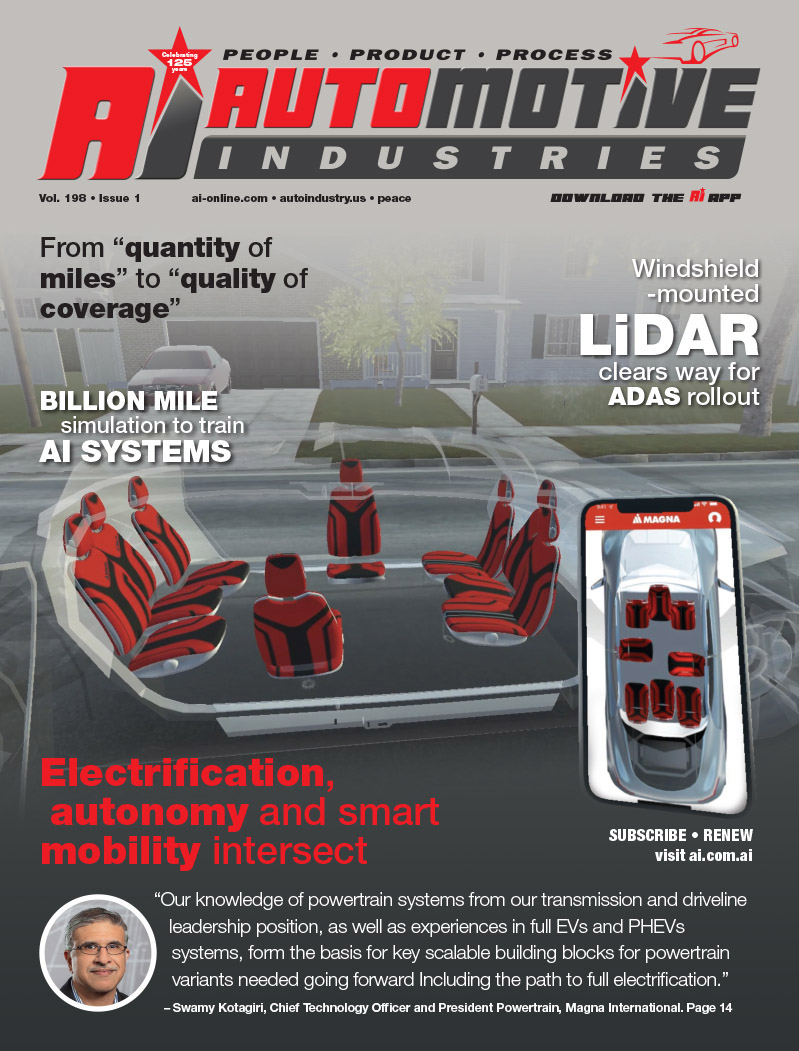
Securing feedstock for polyolefin base resins by Borealis through a joint venture with the Abu Dhabi National Oil Company in Abu Dhabi, UAE has paved the way for continuing advances in the use of plastics in automotive manufacturing.
Once completed, the Borouge 3 mega-project will deliver an additional 2.5 million tons of polyolefins, bringing its capacity to 4.5 million tons, and making it the biggest integrated polyolefins complex in the world. It will bring the combined Borealis and Borouge polyolefin capacity to eight million tons a year.
Borealis has also increased its long-term feedstock flexibility for its petrochemical plant in Stenungsund, Sweden, by signing a 10-year agreement with Antero Resources to supply ethane from the United States. The project includes a shipping agreement with Navigator Holdings, a related multi-million dollar investment in an upgrade of the cracker, and the construction of an ethane storage tank. The ethane supplied from the US complements the ethane supply contract with Statoil, providing Borealis with attractive alternative sources of feedstock. Automotive Industries (AI) asked Nicholas Kolesch, Borealis Head of Marketing Automotive, how important it is for the company to be so involved in the polyolefin value chain.
Kolesch: The full backward integration within the Borealis polyolefin production complexes is of key strategic importance in order to guarantee and secure consistent supply to the automotive industry. Furthermore, with much of our monomer supply coming from our own crackers, Borealis can provide outstanding polymers with excellent product consistency and the highest purity. When combined with our innovation capability we are able to design the right polymers, RTPOs and PP compounds to meet the needs of our customers. Working closely with major Tiers and OEMs, this value chain participation also allows Borealis to position itself as a trend-setter, as the automotive industry is continuously looking for new solutions to reduce the weight of cars. Borealis offers lightweight solutions for visible exterior and interior parts with its new low density Daplen grades (e.g. Daplen EE112AE, Daplen EE058AI, Daplen EE001AI). In the area of structural parts throughout the car, Borealis is a market leader with its Fibremod grade family. Borealis proprietary Fibremod post-reactor technology is a powerful tool to support our customers to design parts to get maximum material performance while avoiding over-engineering, which can increase the weight of the parts. Recently, a significant programme was kicked-off in Borealis to bring lightweight construction to the next level by developing foamable compounded PP grades with “Class A” surface for visible interior and exterior automotive applications.
AI: What is the significance to OEMs in the region of the new plant in Itatiba, Brazil?
Kolesch: Brazil is a dynamic economy and very important automotive market. In addition, it plays a leading role as the largest producer of cars in South America. Most global OEMs and Tiers are active in Brazil and expect local supply and support from their suppliers. As Borealis is committed to providing state-of-the-art solutions to our customers in all the markets in which we operate, the new plant in Brazil lives up to this standard and ensures that Borealis is well positioned.
AI: How many plants do you now have around the world?
Kolesch: Borealis and Borouge operate at 15 sites around the world. Within this network there are several Borealis plants producing TPOs and PP compounds for the automotive industry, including in Monza, Italy; Beringen, Belgium; Schwechat, Austria; Itatiba, Brazil; and Shanghai, China. In addition we have well established innovation and product development capability at our global Innovation Headquarters in Linz, Austria, at the Borouge Application Development Centre in Shanghai and at our location in Itatiba. We are also developing our supply capability in North America. This inter-connected network of plants and development facilities ensures industry leading global coverage.
AI: Please tell us about the cooperation with BMW which led to the development of the new Daplen EE112AE grade for the front bumper of the BMW i8 electric sports car BMW i8.
Kolesch: Borealis and BMW have had a very close relationship for many years, which has led to many significant innovations. Both companies developed the first long glass fiber foamed instrument panel carrier using Fibremod GB215HP or Fibremod GB601HP-AR plus Daplen EE002AE. This solution was first implemented in the BMW 7 series and has in the meantime been adopted by all BMW series. Another innovation was the fender module of the BMW X-vehicles where Daplen EF341AI replaced steel, resulting in a lighter weight and improved pedestrian safety compared to the steel fender, as well as a higher level of integration of additional components. The success of the primerless paint solution Daplen EE112AE for the bumpers of the BMW 3-series and BMW i8 reinforces our belief that fostering close collaboration with our customers is the right way forward.
AI: Are you working with other OEMs on similar projects?
Kolesch: Yes, Borealis is engaged with many OEMs to support innovations on weight reduction, surface aesthetics and sustainability. Our unique approach to partnership is based on integrated OEM teams providing dedicated points of contact for the OEMs. In most cases our OEM Managers and development engineers are located close to the OEM headquarters for a fast and efficient interface.
AI: What are the advantages of developing a new grade for a specific model or application?
Kolesch: The world looks to the automotive industry for advancements in technology and material solutions. Together with the OEMs and Tiers, Borealis strives to make improvements to each new generation of vehicles. This is not just to meet the consumers’ continuous demand for the latest aesthetic change, it is an opportunity to improve performance, bringing economic and environmental benefits in all three lifecycle phases of a vehicle: manufacture, use and end-of-life. These benefits are translated directly into CO2 reduction during manufacture and use, pedestrian safety improvement and recyclability.
As a company fundamentally interested to Keep Discovering, we are ready to work with our customers to develop the best possible solution for the next generation of vehicles – and it’s also fun to see your latest innovation passing by on the street!
AI: Does this not add to the costs of the vehicle?
Kolesch: Not necessarily. You need to look at the total system cost— not just at the material cost —of the innovation. For example, by reducing overall vehicle weight other components like brakes can be down-gauged as well, which will lead to further weight reduction and cost optimization. Or if you see it from the other side it allows you to equip the car with further functionalities without adding weight compared to the former model, which adds value to the end user. Our innovations can also bring down the cost of production. An example is the development of primerless paint solutions, which reduce the number of paint layers from three to two.
AI: What are some of the areas in which OEMs could be making more use of plastics?
Kolesch: Plastics and composites are the future of the automobile. Advances in the material science of reinforced polypropylene compounds make them suitable for an ever increasing number of parts. In the coming years you will see plastic use increasing in the area of glazing and body panels, in particular tailgates. The biggest growth potential for structural parts we see is in the under the bonnet area, seats, door modules and instrument panels. There is a certain probability that entire car concepts — how cars are built — will dramatically change in the future. Newcomers like Tesla and Google are introducing their electrically powered and/or self-driving cars to the market. We have also seen how Apple can revolutionize an industry and would not be surprised if they bring their formidable skills to the automotive industry. We are ready and able to work with these companies to develop the right material solutions of the future.
AI: Will plastics continue to take market share from metals?
Kolesch: We believe the answer is yes. However, it is difficult to predict the extent to which this will happen. Metal producers are also continuously innovating for the automotive industry. High strength steel or new lightweight metal alloys are increasingly prevalent and the amount of aluminum used in vehicles, particularly in the high end of the market, continues to increase. However, plastics bring significant advantages that can never be matched by metal, both in terms of their light weight and, particularly in the case of polypropylene, their low cost in use and recyclability. As the trend to lightweight will continue, we expect to see the amount of plastic in vehicles continue its steady climb. Similar to metals, plastic use in vehicles can also help close the recycling loop, with post-consumer recycled (PCR) polypropylene content to be used in vehicles. For example, our new Daplen portfolio of PP compound grades with PCR and virgin content has been conceived for interior, exterior and under-the-bonnet applications
More Stories
Dürr and GROB concept battery factory uses 50% less production space
DuPont materials science advances next generation of EV batteries at The Battery Show
Cybord warns of dangers of the stability illusion