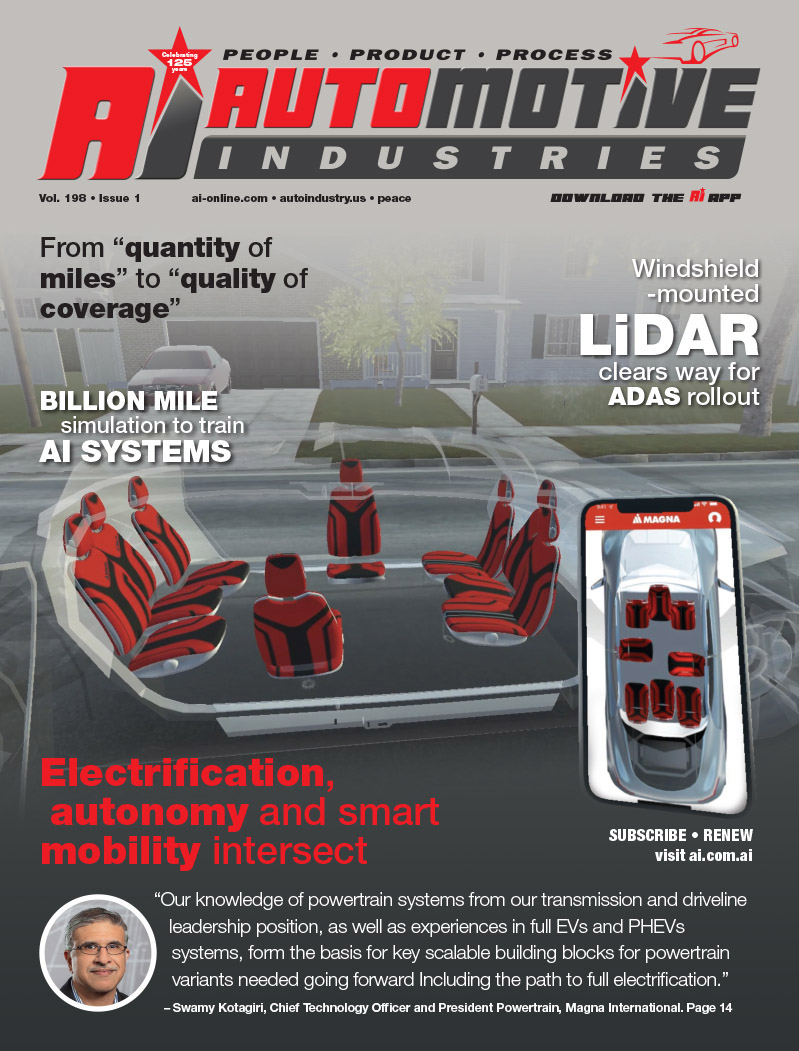
Innovations based on chemistry have helped to solve the challenges of the future since 1865, when BASF was founded.
The 150-year-old company is the leading chemical supplier to the automotive industry. The product range from BASF includes engineering plastics, polyurethane and specialty foams, coatings, pigments, catalysts, fuel additives, coolants and brake fluids, as well as battery materials.
Automotive Industries (AI) asked Dr. Tilo Horstmann, Vice President BASF Mobile Emissions Catalysts, how well positioned the company is in the catalysts market.
Horstmann: BASF is well positioned in the catalysts market. We have the latest technology, such as the EMPRO™ FWC™ four-way conversion catalyst and the patented EMPRO SCR.2F (selective catalytic reduction on filter) and are investing heavily in R&D and new plants. Our new manufacturing site in Poland is up and running. It has an excellent location to supply major automotive manufacturers across Europe with our innovative catalysts solutions. We also continue to invest in our facilities in Nienburg and Hannover, Germany, as well as around the world.
The relevant success factor in this industry is the provider’s ability to best serve customers through the key competitive differentiators. These include best available technology performance and consistent quality combined with a global presence. Precious metal services add to a complete customer service package. We think BASF is well equipped in the industry in each of these areas, which positions us to grow above the market average.
AI: Where do you see the biggest growth opportunity?
Horstmann: There is continued need for innovative solutions to meet the more stringent emissions regulations. Especially the hot topic of real driving emissions challenges the industry within the next years. For light duty gasoline vehicles, we see a strong focus on particulate matter emission. Here, BASF can offer coated filters with very low back-pressure.
For light duty diesel vehicles increased DeNOx performance (reduction of nitrogen oxides) is required to meet Euro 6c emission regulations. This additional DeNOx capability can be achieved with Lean NOx Traps, SCR (selective catalytic reduction), SCR on Filter or a combination of these technologies.
AI: Do you differentiate between gasoline and diesel?
Horstmann: BASF has unsurpassed expertise in developing innovative emission control technologies for a wide range of applications, including gasoline and diesel, to keep the air clean for a sustainable future. We are the emissions professionals, and are proud to introduce EMPRO as the new brand for BASF Mobile Emissions Catalysts. The EMPRO brand represents what makes BASF unique as value added solutions provider. With a creative, open, responsible and entrepreneurial approach we help our customers meet regulations for both gasoline and diesel applications – and to be more profitable.
AI: What are the new products on show at IAA Frankfurt?
Horstmann: IAA is the showcase for new catalysts and battery materials that enable vehicles to have a lower environmental impact, whatever powertrain technology they use. They include the single-component EMPRO FWC four-way conversion catalyst, the patented EMPRO SCR.2F (Selective Catalytic Reduction on Filter) technology, advanced cathode materials and electrolytes that offer high power, high energy, safety and improved efficiency for lithium-ion batteries.
AI: How does the single-component EMPRO FWC help automakers meet emission regulations like Euro 6c while reducing system complexity, tooling and overall system cost?
Horstmann: The traditional three-way-conversion catalyst, used for gasoline-engines, removes carbon monoxide (CO), hydrocarbons (HC) and nitrogen oxides (NOx). However, the new emission regulations also require a reduction in emissions of particulate matter. The EMPRO FWC four-way conversion catalyst combines the functionality of a three-way-conversion catalyst with an additional filter in the exhaust system to remove all four pollutants with just one component. That way we help our customers to meet the new tight regulations and to reduce system complexity, tooling and overall system cost.
AI: How does the EMPRO SCR.2F technology work?
Horstmann: It combines SCR with a diesel particulate filter to control NOx and particulate matter emissions from diesel engines on a single substrate, saving weight and space. To operate, urea is injected upstream of the SCR.2F and is hydrolyzed to ammonia. NOx in the exhaust stream reacts with ammonia in the presence of the SCR catalyst on the filter to produce nitrogen and water. The exhaust flows through the SCR.2F where particulate matter is filtered. The engine management system enables active soot regeneration in order to keep the back-pressure of the system at the designed level. This technology offers the performance to meet current and future emission limits.
AI: What does BASF advanced cathode materials and electrolytes offer in terms of power, energy, safety and efficiency for lithium-ion batteries?
Horstmann: For electromobility to realize its potential we know that new battery technologies and materials need to be developed at scale. The future depends on batteries that can provide higher energy density, greater power, longer lifetime at high safety and lower cost. As the global leader in chemistry, and the largest chemical supplier to the automotive industry, BASF has the global reach, the depth of technical resources, and the strong financial position to excel in this market. We see tremendous potential to advance the industry and secure our place as a leading supplier of materials and solutions to battery manufacturers around the globe.
BASF’s battery materials business has an ambitious growth strategy which currently is in the implementation phase. As part of this strategy we recently established a joint venture “BASF TODA Battery Materials LLC” in Japan. The joint venture will conduct research and development, production, marketing and sales for a broad range of cathode materials, particularly NCA (nickel cobalt aluminum oxide), LMO (lithium manganese oxide) and NCM (nickel cobalt manganese oxide) in Japan. These materials are used in lithium-ion batteries for the automotive, consumer electronics, and stationary storage markets. Internationally, the company will leverage BASF’s global network and reach to drive growth in the battery materials market, which BASF has identified as a key growth field for the future.
AI: What about the next 150 years for BASF?
Horstmann: We supply and develop functional materials and solutions that enable vehicles to be built more efficiently and have a lower environmental impact, whatever powertrain technology they use. For the future we will continue to offer innovative solutions for sustainable mobility.
More Stories
Towing Services Explained: 6 Key Facts You Need to Know
Environmental Factors That Influence Ceramic Coating Choices
Professional vs. DIY Tinting: What You Should Know