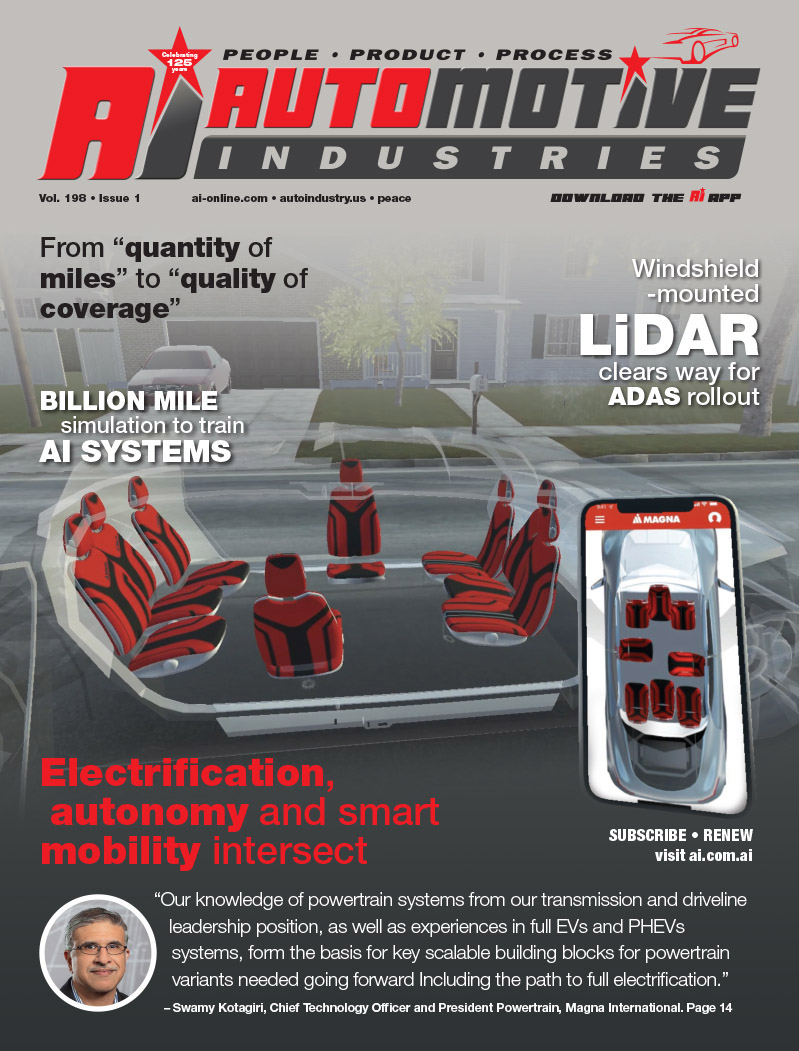
Of all the recent innovations and industry visions, nothing has captured the public’s attention and piqued its imagination like the autonomous vehicle. While some love the idea and others fear it, most experts agree that the road to autonomy will be bumpy.
There are a number of other related trends which are shaping the future of the motor industry. In this feature Automotive Industries (AI) takes a look at security, the savings offered by over the air updates, the connected car and additive manufacturing.
AI asked Oren Betzaleli, EVP, Redbend Product Strategy, Harman, how security concerns with firmware over the air (FOTA) are being managed.
Betzaleli: We have seen a growing concern for automotive cyber security with the rise of the connected car. It makes sense because the connected car is a pretty new phenomena that the market is still in the process of digesting and, as such, it is facing all sorts of “growing” issues like cyber security. But when it comes to Over-the-Air the situation is different. OTA is a not a new phenomenon, but rather a technology that has existed for more than 15 years. As such, it already handles many of the cyber security concerns. More specifically, there are several things to worry consider it comes to OTA cyber security:
Securing the connectivity and transport between the vehicle and the FOTA server – this is done through leveraging TLS (SSL in the past) secured connectivity, which is a common method in secured systems
- Assuring the vehicle is “talking” to the right FOTA server – done through standard keyed HMAC (hash message authentication code), which is part of the OMA-DM standard protocol
- Assuring update packages are authentic – done through “signing” the update package, and then verifying the signature at any step of the way, i.e. when the package is downloaded to the vehicle, when it is being delivered to the relevant ECU, and before it is actually installed (at the last mile). The signing of the packages is done with secured authentication authority (companies such as ESCRYPT) using a secrete key, and then they key is authenticated by the vehicle using public key (again, common security practices).
- Verifying that the vehicle has the authentic software – when the vehicle is started it can go through a reverification that the software it is going to load is indeed authentic, using verification of hashed keys, potentially running from a hardware based secured zone. This is not related to the software update process itself, but rather is a generic precaution that has to do with software to make sure no one changed the software by any means
- Encryption of the software – yet another layer of potential security measure, in which downloaded packages are encrypted by the OEM using a public key, and then decrypted by the vehicle using a secrete key stored in a secured area in the vehicle HW
- Overall IT security – OEMs and their suppliers must keep their backend and network systems secured. This is done by adopting common IT security measures, such firewalls, closing all irrelevant ports, filtering of URLs, passwords management, and more.
AI: Does FOTA help avoid direct and indirect costs?
Betzaleli: Usually people associate OTA updates to elimination of recall costs. However, OTA software management (above and beyond firmware), can reduce direct and indirect cost at any stage of the vehicle lifecycle. Here are some examples:
Engineering
OTA can shorten time-to-market. The process of designing and engineering the vehicle electronics involves many cycles of software reflashing done with development and test cars (mules and such). Each cycle today involves a large number of people physically getting into a car, plugging in a computer or some form of hand-held device, and wasting time installing a new version of the software before the next round of testing can start. This manual process can be eliminated almost completely with OTA distribution of revised software at the engineering site, which can be done over Wi-Fi.
Production lines
The growth in the quantity of software in a vehicle is causing concerns on the production line. At present loading software into a car on the production line is limited to a specific “station” on
the line, in which a physical cable is connected to the car. We have heard from our customers that the time window allocated for software reflash is many times not sufficient, and in some cases even causing bottlenecks in the plants, and even to a complete halt of the line in order to catch-up with delays (they call it “reflash parties”). OTA technology can simplify this process dramatically. Software flashing can start as soon as the battery is plugged in the car, and even afterwards when it is driven to the parking lot.
Staging
Further to the production savings OTA can simplify the software supply chain, where the factory simply install a generic, while the localization can be done at a later stage, over-the-air, when the vehicle arrrives at its destination. This is done in many cases today by manual labor, which is yet another cost element that can be saved.
Dealership
Many people think OTA threatens the dealers’ business model, but I think dealers can use OTA technology to save costs, as well improve the customer experience by shortening customer waiting time. Think about a scenario that when software recall is declared, the drivers will be invited to the dealer, they will get into kind of “drive through” lane at the dealer, where the software will be updated automatically from the dealer’s system, and the customer can be back on the road in a matter of minutes, rather than hours.
Customer ownership
This is where most people understand the cost savings, mainly around elimination of recalls and replacing them with OTA updates over a cellular network. But on top of that, leveraging a delta technology such as Redbend’s, can also save cellular connectivity costs. Such savings can reach hundreds of millions of dollars a year.
AI asked Michelle Avary, Vice-president, Automotive Product & Strategy, Aeris, what the connected car can offer in terms of safety features and how soon they see these features being implemented in cars.
Avary: Connectivity allows critical information to get to the people who help save lives when an accident happens. Connected vehicles with embedded telematics systems already offer safety features, including automatic collision notification and
Software flashing can start as soon as the battery is plugged in the car, and even afterwards when it is driven to the parking lot.
geo-assisted roadside support, which are more reactive safety and after the fact. With systems such as Toyota’s Safety Connect rolling out on more models, and GM’s OnStar standard on all U.S. models and rolling out globally, drivers will soon see more embedded connected safety systems once the European eCall mandate goes into effect in the spring of 2018.
Connectivity can make advanced driver assistance systems (ADAS) better in several ways. By obtaining more data sooner from “the field” on how systems and parts are performing, OEMs and Tier 1s can conduct analysis and make improvements. They can change designs and implement factory changes faster.
Eventually, descriptive and diagnostic analytics will lead to predictive and proscriptive analytics, resulting in updates to safety systems that are already on the road, over-the-air. This is already happening at Tesla, and it’s safe to say that nearly every OEM wants connectivity for analytics and OTA updates of their vehicles. While introducing OTA capabilities will take time, the economics are powerful motivators. It’s no longer the case of something we’ll see “sometime in the future.” It’s happening now, and we expect to see connectivity fostering improvements in vehicular safety very soon.
As a global connectivity provider to several OEMs, including Hyundai, Honda and Chrysler, Aeris also provides secure OTA updates to connected devices and is at the forefront of creating automotive grade OTA capabilities. Combined with global connectivity, connected vehicle management platform and analytics, Aeris offers OEMs a truly global solution for OTA.
AI: Software update discussions have primarily been focused on bug fixes, recalls and security patches. However, with so many of the car’s capabilities being provided via
software, AI asked Matt Jones, President, GENIVI Alliance & Head of Future Infotainment, Jaguar Land Rover, whether he sees updates providing flexibility that the industry has yet to fully realize.
Jones: The future of In Vehicle Infotainment (IVI) is based upon feature additions via software over the air (SOTA) updates. The customers expectations have been well and truly set by the smart phone ecosystems, and not just the apps stores but also the frequent feature additions to the base platform.
AI: How has over the air software updates changed the way automotive companies can offer the latest in-vehicle features?
Jones: Going forwards SOTA solutions, such as GENIVI’s free and open source project, will enable the next generation of companies to more easily join the automotive supplier ecosystem. Each will depend to the economies of scale and being able to rapidly and easily deploy to a range of OEM vehicles; and finally fulfilling the customers desires for the latest features.
AI asked Justin Fishkin, Chief Strategy Officer, Local Motors, how he sees manufacturing technologies evolving over the next few years.
Fishkin: Since the days of Henry Ford the automotive industry has defined efficiencies based on economies of scale — limited product mix, high volume production, low profit margins, and amortization of product-specific tooling and productive capacity over many years due to high upfront tooling costs. Local Motors is defined by our economy of scope — we generate higher profit margins on fewer units of more models, because we don’t need to re-tool to produce new products.
We are a tool-less manufacturer which designs and delivers at the speed of digital. We achieve this through our proprietary process called Direct Digital Manufacturing (DDM), which is the fabrication of components in a seamless manner from computer design to actual part in hand. Often synonymous with “3D printing” or “additive,” “rapid,” “instant,” “on-demand” manufacturing, DDM uses 3D computer-aided design (CAD) files to drive the computer-controlled fabrication of parts. Unlike traditional machining methods, which involve working from a rough mold and then cutting away to achieve the desired complex shape, DDM creates the shape precisely using mostly additive fabrication.
In the same way we rapidly commercialize vehicle innovations, Local Motors leverages the power of community engagement within the digital domain to provide rapid product development and innovative manufacturing techniques in other relevant industry verticals. We call this white label platform “Open.io.” Our approach in offering Open.io combines micro-production with online co-creation to identify ideas, develop prototypes, and bring innovative products to market faster than traditional commercialization processes, and at lower costs. Today, the majority of companies in hardware industry verticals are stuck in a mid-20th century product development model – therefore there are many opportunities to be a leader in hardware using this rapid commercialization method.
By combining our ideas, concepts, and designs with a strong set of core competencies in 3D-printing, Direct Digital Manufacturing, and additive manufacturing; Local Motors has developed a product
development process that is unequaled in industry.
Strategic benefits of our Open.io platform for businesses in other industries include:
- Injects the benefit of open innovation into product development (brand, exogenous ideas, multi-faceted reward, camaraderie)
- Identifies leaders within the industry who can solve, purchase early, or perhaps even join the core team
- Increases the speed of product development by generating ideas and concepts through open interaction, and rapidly prototyping new products through low-volume manufacturing
- Leverages the benefits of digitalization on both product development and business planning by interacting directly with a community of experts and consumers. This can mean better defensive product introductions in addition to the discovery of new products for grow and scale. This also means better and faster identification of new suppliers with less work.
- Increases speed of discovery of issues, which allows the system to promote safety and improvement first and continuously
AI: How has your open platform, FirstBuild, changed the manufacturing scenario?
Fishkin: Our partnership with GE’s appliance division, FirstBuild, has co-created nearly a dozen products in its first year, uniting Makers, University of Louisville students and other local partners. FirstBuild is the first example of our collaboration with GE and other large-scale manufacturing partners, illustrating success of rapid innovation through co-creation and micro-production
More Stories
Towing Services Explained: 6 Key Facts You Need to Know
Environmental Factors That Influence Ceramic Coating Choices
Professional vs. DIY Tinting: What You Should Know