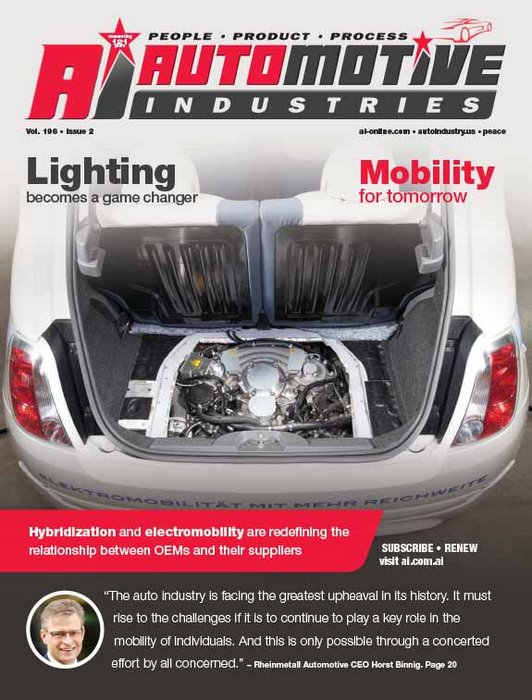
Megatrends such as growing urbanization accompanied by new business models of urban mobility, the spread of interconnectivity and the greater and greater use of electromobility are transforming our world – including the automotive industry.
Over the next five years the automotive industry globally will be undergoing greater changes than over the past 100. “The auto industry is facing the greatest upheaval in its history. It must rise to the challenges if it is to continue to play a key role in the mobility of individuals. And this is only possible through a concerted effort by all concerned,” says Rheinmetall Automotive CEO Horst Binnig. New business models are required to meet the challenges of growing complexity in the automotive sector. One of the most challenging areas is the electrification of the drive system, which covers such a variety of factors that it is impossible for a single auto manufacturer, or an auto industry supplier for that matter, to handle it with their own resources and without any external assistance – especially since the mainstream of future drive system technologies is not yet clear.
Simply looking at the establishment of an integrated recharging infrastructure it becomes clear that it will take a partnership between different parties involved in electromobility to install an effective and well-functioning network of charging points. It is therefore logical that BMW, Daimler, Ford and Volkswagen have agreed to work together to set up an ultra-fast, high-power charging network along major highways in Europe.
This is comparable to the 48 charging corridors which the United States is building along 25,000 miles of highways across 35 US states. It is the result of collaboration between the U.S. Department of Transportation (DOT), State authorities, auto manufacturers and utility companies. The plan is for charging stations to be located every 50 or so miles along the routes.
While it is too soon to predict with confidence whether the dominant technology will be plug-in hybrid electric vehicles (PHEVs) or battery electric vehicles (BEVs or some other technology), it can be expected that hybridization and electromobility will redefine the classical relationship between manufacturers and their suppliers – if only for technical reasons.
Hybrid and battery-powered vehicles require a large number of new vehicle components – which inevitably translates into a redefinition of the supply chain. Existing component suppliers like Rheinmetall are designing and manufacturing components for drives and storage systems which did not even exist a few years ago. The company believes that both Tier companies and their own suppliers have to reinvent themselves. They also need to work together to ensure that the new technology is environmentally sustainable and has the smallest possible footprint.
“It will help our industry move forward if we are able to master the challenges ahead. Completely new opportunities will open up of which we have no notion now. As a group we enjoy a strong
position in the international auto industry thanks to our heavy spending on R&D,” says Binnig.
Shorter development cycles are adding to the pressure on OEMs. The response to the challenges requires a well-functioning technical interlinkage at all levels between the various parties. As a drive system specialist with a history going back over more than 100 years, Rheinmetall Automotive says it has recognized these “signs of the times,” and is adapting its research and development and product portfolio accordingly.
“If I take a look at the products we currently supply for the purpose of optimizing the drive train on an internal combustion engine and compare these with what we currently have in our development pipeline for future types of drive systems, I
arrive at a substantial growth in value. In terms of figures, this could be almost double our share of sales per unit. As early as 2020, electrification will account for over one-half of our sales,” says Binnig.
Among the new products being developed by Rheinmetall Automotive are castings for the battery holders of electric vehicles and highly complex, cooled aluminum housings for the electric drive units themselves. Added to these are electrically-powered auxiliary units, extremely lightweight structural parts, heat-pump components and range extenders.
Rheinmetall is also drawing on its experience in the defense sector to enhance cyber security within a vehicle and to provide 360 degree virtual reality views around a vehicle.
More Stories
DuPont materials science advances next generation of EV batteries at The Battery Show
How a Truck Driver Can Avoid Mistakes That Lead to Truck Accidents
Car Crash Types Explained: From Rear-End to Head-On Collisions