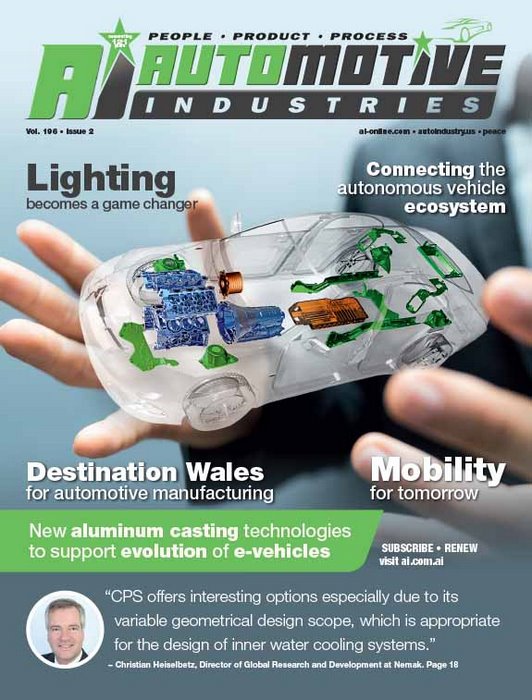
Electric drive units are becoming so complex and compact that they have sparked innovation in the casting industry in order to ensure that production can meet demand.
A 2016 Roland Berger Global Automotive Supplier Study on page 29 predicts that there will be a significant increase in the volumes of electric and hybrid vehicles produced over the next eight years. “On the powertrain side, the development of e-mobility is gaining a lot of “momentum – while technological hurdles prevail and a convincing business case for the end customer is nowhere close to accomplishment yet, tightened emission regulations by supranational and local bodies will likely have a catalytic impact over the coming years,” predicts the report.
The swing will be so marked that traditional combustion engines will lose market share. By 2025 hybrids will account for 13.2% of new vehicle sales, electric vehicles 4.6%, and plug- in hybrid electric vehicles (PHEVs) 7.1%. In 2015 the combined market share of all three types of propulsion was just 2.1%, according to Roland Berger. By 2030 the market share of internal combustion engines is predicted to fall to 60%.
At the same time the vehicle markets are still expected to grow. Lightweighting becomes more and more important in the light of powertrain electrification. Due to its preferred combination of low weight and good mechanical and physical properties the share of aluminum in electrified vehicles is being boosted, and aluminum castings, stampings, extrusions and sheet metal products are capturing a wide range of applications. New production methods are being developed and combinations of various components are built into sub-assemblies to ensure the new market requirements will be met – not only in terms of volumes but also in terms of functionality of the components.
The aluminum casting expert estimates that the industry will need to make around 455 million aluminum castings a year in 2025 – up from 319 million in 2015. Of these 109 million castings will be for hybrid vehicles, and seven million for electric vehicles. In 2015 there were just 10 million aluminum castings for electric and hybrid vehicles combined. The number of castings for internal combustion engines will flatten out at around 338 million by 2025.
According to Christian Heiselbetz, Director of Global Research and Development at Nemak, the design of electric motor housings, batteries and control units is fast approaching the complexity of components in a conventional combustion engine in response to some of the “technical hurdles” identified in the Roland Berger study. There is a significant shift away from the design of earlier e-drives. “A huge leap of development is perceptible in this area,” he says.
New production processes are being developed to meet the demand of producing high volumes of components with high power density and increasing functional integration – often accompanied by complex inner cooling configurations. “At the moment it is not clear which casting processes will be selected in future for these components,” he says.
Some of the automotive industry’s best minds are fine-tuning existing casting technology and exploring new approaches to meet the growing demand for cast aluminum components for both electric and conventional vehicles. Roland Berger sees the global demand for new cars reaching around 119 million in 2025 – of which 25% will have some form of electric drive.
Nemak has engineers in 11 product development centers around the world driving lightweight design by increasing complexity of the cast components and continuously improving the casting processes. “We are well-positioned to partner with OEMs to co-design, engineer and test components,” says Heiselbetz.
The company has been focusing on e-mobility since 2011, with serial production of some components commencing in 2013. It has developed multifaceted e-drive applications, battery housings, and e-motor components, including a single part casting process with complex shaped cores. With two-part components the challenge is to ensure the two halves will seal correctly. “During the product development phase attention must be given to the quality of the sealing surface, which is achieved by special treatments as part of the casting process, as well as an optimized machining and in-line joining procedure,” says Heiselbetz.
He says Nemak has a number of proven casting options available for serial production. The choice is determined by the complexity and the required volumes which need to be produced. Preferred processes are the low pressure die casting (LPDC) or the core package sand core casting (CPS® – Core Package System). LPDC is suitable for electric engine housings due to its nearly rotational symmetry. The laminar flow of the molten aluminum into the cavity guarantees a minimum of non-metallic inclusions and secures the required high level on quality. CPS will be selected as an alternative casting process whenever the level of integration increases, for example by joining electrical energy management components, the electric power plant and the transmission into a single housing. “CPS offers interesting options especially due to its variable geometrical design scope, which is appropriate for the design of inner water cooling systems,” he says. Nemak is adding value to its castings by providing machined components where required.
A new field of application for castings is battery housings. These housings usually have flat and broad sides which are well suited to high pressure die casting. “But some designs which have complex cooling channels which cannot be produced using the usual high pressure die casting process. For those components LPDC is the recommended process because it allows complex structures to be produced,” he says
More Stories
Cybord warns of dangers of the stability illusion
Automotive Industries interviews Bahar Sadeghi, Technical Director, Car Connectivity Consortium (CCC)
Hexagon’s MAESTRO reinvents CMM systems through digitization