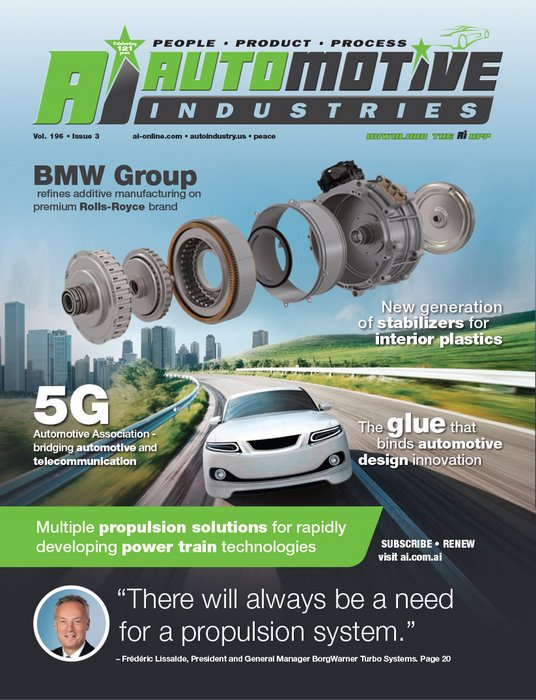
“There will always be a need for a propulsion system,” Frédéric Lissalde, President and General Manager BorgWarner Turbo Systems, told the media at a June 2017 briefing.
And propulsion systems need to be connected to the wheels to drive the vehicle forward. BorgWarner’s innovations covering combustion, hybrid and fully electric engines reflect the moves and advances being made by the industry.
Automotive Industries (AI) asked Lissalde to please give us some examples.
Lissalde: In the light vehicle segment BorgWarner supports major OEMs with several products for vehicles using combustion, hybrid or electric propulsion systems. The products include our advanced AWD technologies, starters and alternators, EGR-systems, thermal management solutions, electric drive motors, dual-clutch modules, variable cam timing solutions or the electric Drive Module (eDM).
For commercial vehicles, in addition to the eBooster® Electrically Driven Compressor
technology, BorgWarner offers the eTurbo™ electrically assisted turbocharger, which enables electric charging assistance for improved time-to-torque in the low rev bands, as well as energy recovery from the exhaust gas flow by utilizing its integrated electric machine as a motor or generator respectively.
Furthermore, BorgWarner develops key parts for an Organic Rankine Cycle (ORC) waste heat recovery system that is especially effective in long-haul applications. The ORC scavenges heat energy from the vehicle’s exhaust gas flow to operate a heat engine that sends the recovered power back to the vehicle. Our 48-volt eFan with its advanced electric motor design and lightweight modular package provides outstanding fan speed responsiveness for precise temperature control with low noise. The eFan adjusts its performance on demand and responds immediately to the engine’s cooling needs to save energy and contribute to improved fuel economy.
Another prime example of BorgWarner’s comprehensive approach across different segments is the company’s High Voltage Hairpin (HVH) 410 electric motors. The technology offers a high power density with a maximum efficiency of 95%.
BorgWarner has also developed an economical new series of multi-platform exhaust gas recirculation (EGR) coolers featuring a compact floating core. The company’s modular cooler family includes four highly adaptable standard designs for maximum flexibility covering a wide range of engine sizes from 2.0- to 16.0-liter displacement.
In addition, BorgWarner’s eBooster® electrically driven compressor delivers boost on demand until the turbocharger takes over, improving boost at low engine speeds and nearly eliminating turbo lag.
AI: What is your contribution to the development of cars such as the Audi Q5 and the Jaguar F-Pace.
Lissalde: We supply the Jaguar F-Pace with our pre-emptive on-demand transfer case which offers precise linear clutch actuation for immediate response, enhanced vehicle traction and stability control. We also supply turbochargers for a 2.0l diesel engine and a 3.0l TFSI gasoline engine of the Audi Q5. In addition, an Audi Q5 test vehicle is equipped with our eBooster® electrically-driven compressor which is also supplied to Daimler. The eBooster® technology provides boost on demand without perceptible turbo lag.
AI: What is BorgWarner’s contribution to the development of more efficient internal combustion engines, hybrid and electric cars?
Lissalde: We are connected to all of these trends. Even though they impact the industry in different ways, at the end of the day, they all require a propulsion system to get vehicles from point A to point B. For combustion engines we support trends like engine downsizing. Our turbochargers, variable cam timing and exhaust gas recirculation solutions meet our customer needs by providing better fuel economy, decreased emissions and improved performance.
For hybrid electric vehicles we offer a broad range of technologies such as the one-way clutch, the off-axis P2 module, an electric rear drive module (eRDM), the 48-volt Integrated Belt Alternator Starter (iBAS) or an electric all-wheel drive (eAWD) to just name a few. With regard to fully electric vehicles we already supply products for four out of the five main segments: electric motors, transmissions, power electronics and thermal management systems.
AI asked Stefan Demmerle, President and General Manager PowerDrive Systems at BorgWarner, what makes the EFR turbochargers so effective.
Demmerle: Our EFR (Engineered For Racing) turbochargers offer an unprecedented combination of advanced technologies, such as low-weight Gamma-Ti turbine wheels and shaft assemblies for quick boost response, patent-pending dual ceramic ball bearing cartridges for more thrust capacity, durability and turbine efficiency at low expansion ratios and stainless steel turbine housing for increased efficiency, improved durability and corrosion resistance. In addition, our engineers perform infinite element analysis to optimize wheel strength, calculate air and exhaust gas flows, and assess durability based on realistic driving cycles. Finally, aerodynamic components are tested on customized turbocharger test stands.
AI: How does BorgWarner juggle the twin aims of providing power to cars while making them more fuel efficient and environmentally viable?
Demmerle: Every one of our products follows the goal of lowering emissions. Our turbochargers for example are always perfectly matched to the engine to improve fuel efficiency and emissions while also contributing to increased torque. In addition, by developing and offering solutions, such as the eBooster® electrically driven compressor and the eTurbo™ electrically-assisted turbocharger we enhance fuel economy by enabling further downsizing and downspeeding. Moreover, our electric drive module (eDM) with the included HVH 250 electric motor delivers a maximum power output of 305 kW and up to 408 Nm of torque. AI asked Dr. Jürgen Adam, Business Director eBooster®, BorgWarner Turbo Systems, to tell us about the company’s eBooster® technology.
Adam: There are multiple different solutions to meet the high demands in terms of fuel efficiency and performance. One is the development of strategies to boost fuel economy through powertrain electrification with 48-volt electrical systems. These higher-voltage power supplies offer significant improvements in efficiency and enable new approaches, such as electric boosting for enhanced low-end torque and transient response.
Our eBooster® electrically driven compressor was designed to improve boost pressure and transient engine behavior at low engine speeds without increasing exhaust back pressure and negatively impacting on the engine gas exchange since no additional turbine is needed. With this solution we developed an excellent and highly efficient addition to the conventional turbocharger to improve engine fuel economy, transient response and consequently allow the engine power density to be increased. In addition, improvements in fuel efficiency and the optimization of emissions, particularly in the case of diesel engines, are facilitated by matching the eBooster® electrically-driven compressor and turbocharger as an overall system.
AI: What changes did BorgWarner make to its turbocharger in order the use it along with your eBooster® technology?
Adam: As a system supplier we have the advantage of being able to perfectly match the eBooster® technology with our advanced turbocharging solutions to achieve a homogenous package. The turbocharger/eBooster® configuration depends on the customer’s requirements and the targets to be achieved.
More Stories
Cybord warns of dangers of the stability illusion
Automotive Industries interviews Bahar Sadeghi, Technical Director, Car Connectivity Consortium (CCC)
Hexagon’s MAESTRO reinvents CMM systems through digitization