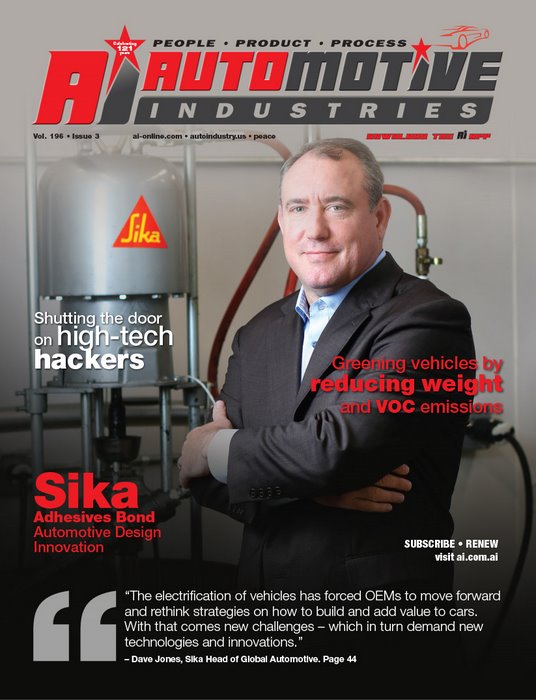
Bonding with Innovation in Evolutionary Times”
To demonstrate the bonding strength and the extremely fast cure time of its adhesives, Sika bonds a windscreen to a passenger car using its PowerCure® adhesive system – and the entire vehicle is lifted off the ground by a crane with only suction cups placed on the windscreen after just 60 minutes! That, for Sika Head of Global Automotive Dave Jones, is a clear illustration of a constant stream of technology breakthroughs which are allowing OEMs to re-engineer the way vehicles are designed, put together and even how they are being powered.
Jones describes to Automotive Industries (AI) how he feels about the introduction of technologies such as autonomous, electric and hybrid vehicles over the next few years.
Jones: It’s awesome. I’ve been in the industry for over 25 years, and we are now going through one of the most exciting evolutions of our business, with dynamic shifts transforming the automotive industry. The electrification of vehicles has forced OEMs to move forward and rethink strategies on how to build and add value to cars.
With that comes new challenges – which in turn demand new technologies and innovations. And that speaks directly to what we do. Sika is here to enable our customers to successfully work through this transformation.
AI: What makes Sika Automotive unique among suppliers to the automotive market within your segments?
Jones: We offer a full range of preformed part and bulk adhesive products for bonding, damping, sealing and reinforcing applications found throughout the vehicle. This position is unique to us, as most of our competitors have pieces of the solutions – either parts or bulk technology. We can supply both, depending on the needs of the particular customer. Sika products contributed as parts include SikaBaffle® acoustic baffles, SikaReinforcer® structural reinforcements and SikaDamp® panel dampers. Bulk product, which basically is everything that comes out of a drum, includes Sikaflex® and SikaPower® adhesive for assembly shop and body shop applications. Further we offer PSA’s (pressure sensitive adhesives), hotmelt adhesives and 2C (2-component) products under our SikaMelt®, SikaTherm® and SikaForce® brands for interior and exterior component assembly.
AI: What is Sika’s global footprint?
Jones: We are very proud of our global reach. Not only does it mean we have the technical know-how and capabilities in different regions, the advantage of having local employees that share the same culture and speak the same language as our customers cannot be overstated. Sika as a group is in over 100 countries worldwide with 200 factories, and over 17,000 plus employees. Specific to our automotive group we have over 60 dedicated sites including global manufacturing facilities with nine technical centers. Two regions in which we have been particularly successful are China, where we count many domestic Chinese OEMs as customers, and Brazil, where through an acquisition made in 2011 we now have a very strong regional footprint.
AI: How innovative are Sika’s automotive adhesive technologies?
Jones: We have a long and storied history of being very innovative. We have over 1,200 people working on research and development in our 19 technology and development centers throughout the Americas, Europe and Asia. Our R&D is driven by the mantra of “customer first” – we understand that the more successful our customers are, the more successful we are. We invite our customers to “bring us your problems, and we will solve them”.
AI: How are you helping to ‘green’ automobiles and their manufacturing?
Jones: Our product range enables our customers to make greener vehicles by reducing weight and emissions of VOCs (Volatile Organic Compounds). SikaPower® structural adhesives are used by car makers to bond vehicle body structures for added strength and durability. Certain formulations are designed for joining lighter materials and also in mixed material bonding situations. For example, the new BMW 7 series body is lighter and stiffer than the previous generation thanks to the bonding of CFRP (carbon fiber-reinforced plastic) to steel with SikaPower®. In another revolutionary vehicle, the BMW i-3 electric vehicle, our Sikaflex® Ultra High Modulus adhesive is used to bond the CFRP passenger compartment to the aluminum chassis. In the past automotive pre-treatments for direct glazing, like cleaners, activators and primers, were solvent-based. Our new water based pre-treatment systems alone have helped reduce over 200,000 liters of VOC’s annually in vehicle manufacturing.
AI: How has SikaMelt® been a game changer in the industry?
Jones: SikaMelt is a unique product family with a wide range of capabilities and uses which allow our customers to reduce costs and manufacturing complexity. SikaMelt adhesives can also be formulated to join non-traditional lightweight materials. For press-lamination applications it can bond foam- backed textile, leather and carpet to different types of plastic carriers such as PP (polypropylene), ABS, TPO and natural fiber. The SikaMelt SF series of lamination adhesives have low isocyanate content, making it safer for workers while maintaining the excellent performance for demanding applications.
AI: How have safety-related products like SikaReinforcer® been key to OEMs?
Jones: Safety and Lightweighting are key drivers in the automotive design but they can also be a dichotomy of interests. How can vehicle safety not be compromised by making the car lighter? SikaReinforcer® is the answer to that question. Made of lightweight composite material and expandable structural foam, SikaReinforcer is a lightweight alternative to using steel or other metal reinforcement. More importantly, it can be designed to provide equivalent structural performance in the body structure without sacrificing safety and comfort, while also improving NVH characteristics of the total vehicle.
AI: tell us a little about SikaBaffle®
Jones: Our preformed acoustic product range is certainly a core competency area in our business and we continue to innovate the entire product range. Our new SikaBaffle®-230 is a rubber-based, highly-expandable elastomeric tape for sealing and acoustic treatments in the automotive body shop. It is engineered for reduced mass and high expansion, which helps to enable vehicle lightweighting initiatives. All SikaBaffle and SikaSeal® products are designed to have maximum application versatility, tenacious adhesion, wide substrate compatibility and excellent acoustic performance; certain products are even formulated for water sealing applications in wet areas.
AI: What is Sika’s strategy in the automotive aftermarket, and how has this grown over the past few years?
Jones: The way you repair a vehicle has changed markedly over the past 20 years, along with the introduction of new manufacturing techniques. The knowledge we have acquired working in partnership with OEMs and Tiers flows into the products we offer the automotive aftermarket. One example: the Sika system is the preferred choice of direct glazing professionals around the world. It is designed to work at all temperatures and under all climatic conditions. We also cover specific aftermarket needs for crash repair including structural adhesive, reinforcers, and acoustic baffles.
AI: What is Sika doing to continue being a major player in its market segments?
Jones: The automotive industry, by its nature, is ever-changing with global dynamics and megatrends. To remain relevant, we can’t be complacent and be satisfied with our existing share. We must focus our energy to develop sustainable growth. There are a few key elements to guide us. First, we are a company that is always looking to innovate with new products. Second, our innovations are always market and customer focused. Third, we always keep our eyes on the megatrends and we will develop products and acquire companies and technologies as needed to stay at the leading edge. Fourth, Sika continues to invest and expand capabilities on a global basis, open new factories and technology centers. And last, we will constantly reinvest in our R&D and our manufacturing capabilities to keep them invigorated.
Editor’s note: See the Sika windscreen demonstration
More Stories
Towing Services Explained: 6 Key Facts You Need to Know
Environmental Factors That Influence Ceramic Coating Choices
Professional vs. DIY Tinting: What You Should Know